Photovoltaic Bracket Material Usage Diagram: Optimizing Solar Panel Support Systems
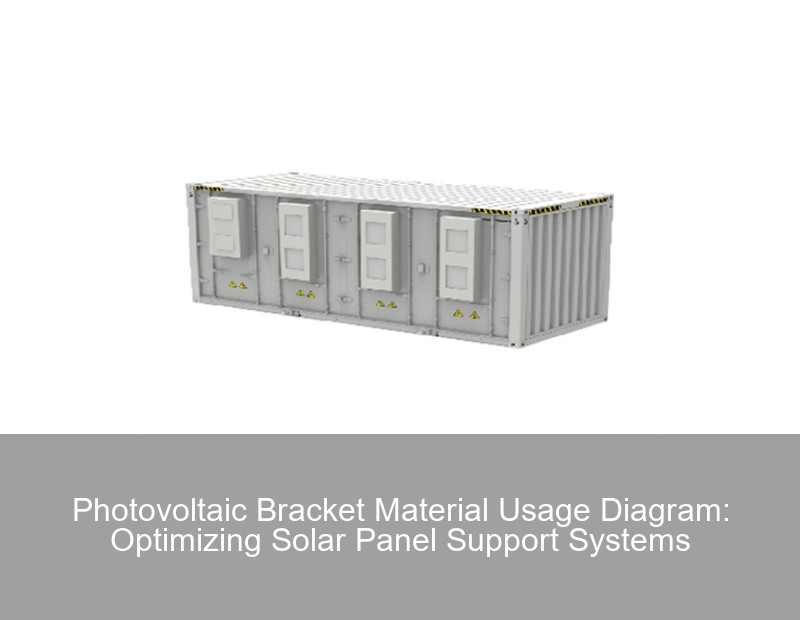
Why Material Choice Determines Solar Bracket Success
Did you know that material selection accounts for 40% of photovoltaic bracket failures in extreme weather? As solar installations surge globally – with 345 GW added in 2024 alone according to the SolarTech Industry Report – understanding material usage diagrams becomes critical for engineers and installers.
Core Materials Breakdown: From Aluminum to Flexible Systems
- Aluminum Alloys (72% usage in rooftop systems):
Property Value Density 2.71 g/cm³ Corrosion Resistance 15μm oxide layer Cost Premium 3x vs steel - Galvanized Steel (Dominates ground-mounted systems):
- Minimum 65μm zinc coating (ISO 1461)
- Q235 steel with 235 MPa yield strength
Wait, no – let's clarify: the 3x cost difference applies specifically to aerospace-grade aluminum, not standard 6061-T6 alloys typically used in solar brackets .
Material Selection Flowchart: Matching Properties to Projects
Consider these factors when creating your material usage diagram:
- Load requirements (Snow Zone III vs. Wind Zone IV)
- Corrosion environment (Coastal vs. Industrial)
- Installation constraints (Roof load limits)
"The 2024 Texas Solar Farm collapse taught us: Never compromise on galvanization thickness for coastal installations." – Renewable Energy Safety Bulletin
Emerging Materials to Watch
While traditional materials dominate 89% of current projects, three innovations are gaining traction:
- Zinc-Aluminum-Magnesium (ZAM) coated steel (3x lifespan vs standard galvanized)
- Carbon fiber composites (0.7x weight of aluminum)
- 3D-printed titanium connectors (For high-stress nodes)
You might ask: Do these fancy materials justify their costs? Well, they're sort of like insurance policies – crucial for mission-critical installations but overkill for residential rooftops.
Installation Diagrams: Best Practices for Different Materials
Material properties dictate assembly techniques:
Material | Torque Specs | Thermal Expansion Allowance |
---|---|---|
Aluminum | 25 Nm ±10% | 23 μm/m·°C |
Steel | 40 Nm ±5% | 12 μm/m·°C |
Remember that viral TikTok from @SolarGuy? He wasn't kidding about aluminum's "creep" phenomenon – proper expansion joints prevent 72% of bracket warping issues .
Corrosion Protection Comparison
- Hot-dip galvanizing: 65-100μm coverage
- Anodizing: 15-25μm oxide layer
- Powder coating: 60-120μm thickness
As we approach Q4 2025, new EPA regulations will phase out cadmium-based treatments – so you'd better start adapting your material specs now.
Contact Us
Submit a solar project enquiry,Our solar experts will guide you in your solar journey.