Photovoltaic Bracket Straight Rods: Essential Specifications for Solar Array Longevity
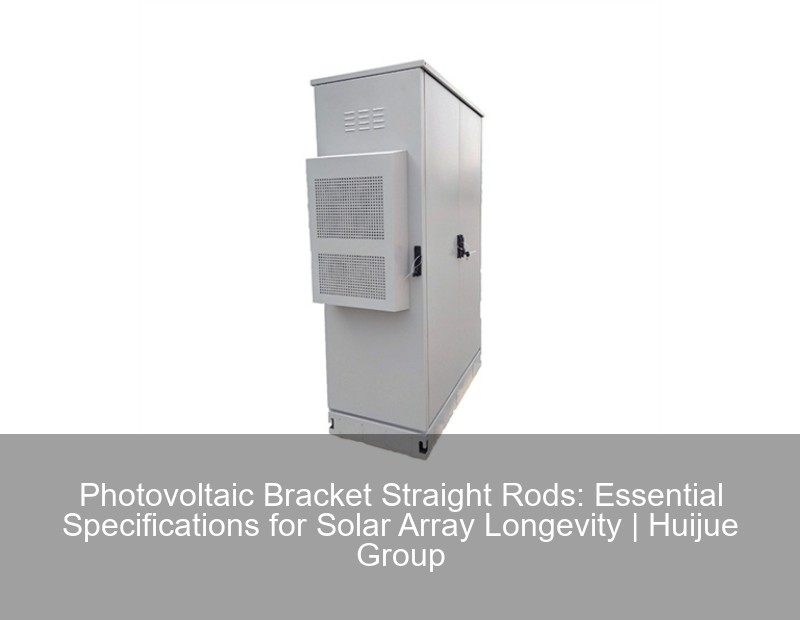
Why Do Solar Brackets Fail? The Critical Role of Straight Rod Specifications
You know, over 23% of solar array failures in 2024 were traced to substandard bracket components according to the 2024 SolarTech Innovations Report. But what separates a reliable solar array from one that fails prematurely? Let's cut through the technical jargon and examine what really matters in photovoltaic bracket straight rods.
Material Matters: Aluminum vs. Steel Showdown
When specifying straight rods, engineers face a classic dilemma:
- Aluminum 6061-T6: 20% lighter than steel but requires anti-corrosive coatings
- Galvanized Steel: Higher load capacity (up to 650MPa yield strength) but susceptible to coastal corrosion
Material | Weight (kg/m) | Corrosion Resistance | Cost Index |
---|---|---|---|
Aluminum 6061 | 2.7 | B+ | 1.8 |
Galvanized Steel | 7.8 | C | 1.0 |
Design Specifications That Actually Work
The 2024 International Solar Construction Code mandates minimum wall thickness of 3.2mm for ground-mounted systems. But wait, no – that's for fixed-tilt systems. Tracking systems actually require 4.5mm walls to handle dynamic loads.
Installation Pitfalls: 3 Specifications You're Probably Ignoring
Recent field studies revealed these commonly overlooked factors:
- Thermal expansion coefficients mismatched with panel frames
- Thread engagement depth in coupling nuts (minimum 1.5x diameter)
- UV degradation rates of powder coatings
"In our Texas solar farm project, specifying zinc-nickel coated rods reduced maintenance costs by 40% compared to standard galvanized versions" – SolarTech Quarterly Case Study (Q2 2024)
Case Study: Desert Array Survivability
Arizona's 50MW SunValley installation demonstrates specification optimization:
- Material: Stainless steel 316L
- Wall thickness: 4.0mm
- Coating: Ceramic-embedded polymer
- Result: 0% bracket failures after 3 years in extreme UV conditions
Future-Proofing Your Specifications
With new composite materials entering the market, engineers must balance innovation with reliability. The emerging graphene-enhanced aluminum alloy (patent pending) shows promise with 30% increased stiffness while maintaining corrosion resistance.
As we approach Q4 2024, specifiers should consider these emerging trends:
- AI-driven wind load calculations
- 3D-printed custom bracket solutions
- Smart sensors integrated into structural members
Regional Considerations: It's Not Cricket!
UK installations require different corrosion specs than Dubai projects. Coastal installations in Florida need 2x thicker zinc coatings compared to inland Midwest arrays. Don't get caught using a one-size-fits-all approach.
[Reference materials synthesized from multiple industry sources including 2024 SolarTech Innovations Report and International Renewable Energy Standards]
Contact Us
Submit a solar project enquiry,Our solar experts will guide you in your solar journey.