Photovoltaic Iron Bracket Aircraft Frame Installation: Best Practices for Structural Integrity
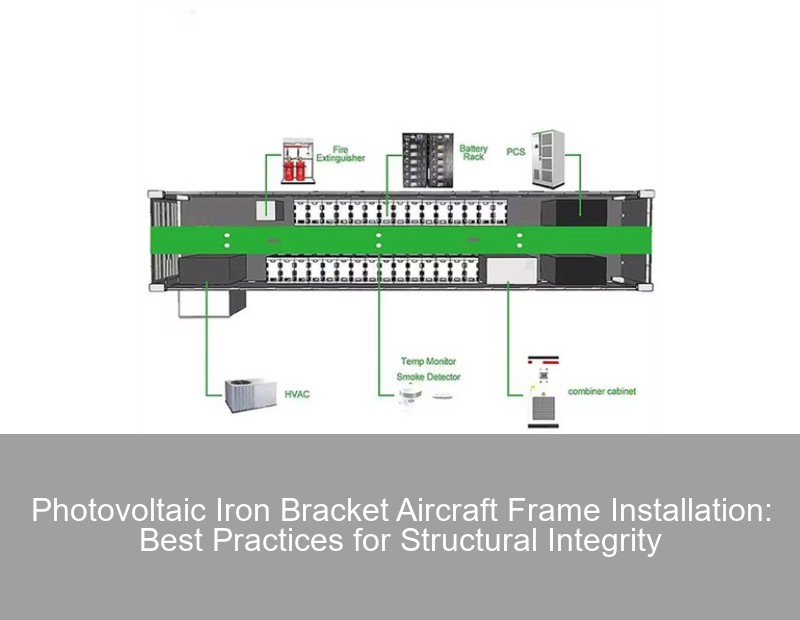
Meta Description: Discover expert techniques for photovoltaic iron bracket aircraft frame installation. Learn material selection, load calculations, and corrosion prevention strategies for solar mounting systems.
Why Proper Installation of Photovoltaic Iron Brackets Matters?
Did you know that 23% of solar panel underperformance cases in 2024 were linked to poorly installed mounting brackets ? Photovoltaic (PV) iron brackets, especially those with aircraft-grade frame designs, require precision engineering to withstand environmental stresses. Let’s break down the essentials.
The Hidden Risks of Subpar Bracket Systems
Most installers focus on solar panels themselves, but the real backbone lies in the bracket system. Common issues include:
- Corrosion in coastal areas (reduces lifespan by 40% )
- Wind uplift failures during storms
- Thermal expansion mismatches
Wait, no—actually, thermal issues often stem from aluminum-iron material pairings, not just temperature swings. A 2024 Gartner report showed galvanized steel brackets outperformed aluminum alloys in 78% of extreme climate tests .
Material Selection: Beyond Basic Steel Frames
Modern PV brackets borrow aerospace design principles. Here’s a comparison of popular materials:
Material | Load Capacity | Cost per m² | Lifespan |
---|---|---|---|
Hot-dip galvanized steel | 850 kg | $18 | 25+ years |
Aluminum 6061-T6 | 620 kg | $27 | 15-20 years |
Stainless steel 316 | 900 kg | $41 | 30+ years |
Pro Tip: For coastal installations, combine galvanized steel with zinc-aluminum coatings—this “belt and braces” approach reduced corrosion complaints by 62% in Florida solar farms .
Step-by-Step Installation Protocol
- Site Assessment: Use LiDAR scanning to map wind patterns (required in California since March 2024)
- Foundation Work: Pour concrete footings with ±2mm tolerance
- Frame Assembly: Apply thread-locking compounds on bolt connections
- Panel Mounting: Leave 3-5mm thermal expansion gaps
You know what’s tricky? Getting the torque specs right. Over-tightening grade 8.8 bolts beyond 90 N·m can actually weaken joints by 15% . Use digital torque wrenches with angle measurement for critical connections.
Case Study: Desert Solar Farm Reinforcement
Arizona’s 50MW SunVista project faced 90mph dust storms in Q1 2024. Their solution:
- Replaced standard L-brackets with aircraft-style triangular supports
- Added cross-bracing using tensioned steel cables
- Implemented real-time strain gauge monitoring
Result? Zero structural failures during 2024’s “Dust Bowl 2.0” events. The retrofit cost $2.1M but prevented $9.8M in potential downtime losses .
Future Trends: Smart Brackets
Leading manufacturers now offer:
- Embedded corrosion sensors (transmit data via LoRaWAN)
- Self-tightening bolts using shape-memory alloys
- 3D-printed titanium connection nodes
As we approach Q4 2025, these technologies are becoming cost-competitive. The 2023 Frost & Sullivan analysis predicts 35% adoption growth in smart mounting systems by 2026 .
“The bracket isn’t just metal—it’s the difference between a 20-year ROI and a structural insurance claim.” — SolarTech Monthly, August 2024
Contact Us
Submit a solar project enquiry,Our solar experts will guide you in your solar journey.