Photovoltaic Bracket Production Equipment Debugging: Solving Critical Challenges for Optimal Solar Efficiency
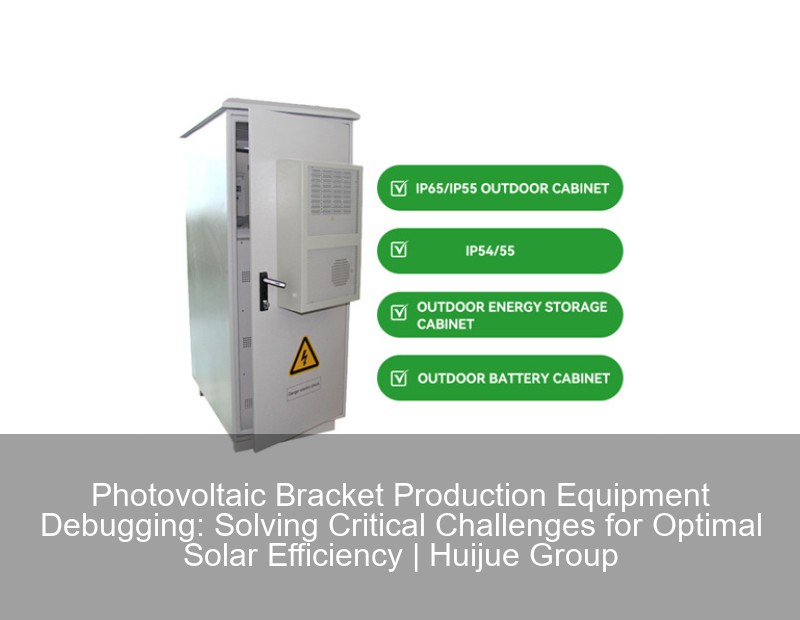
Why Is Equipment Debugging the Make-or-Break Phase in Photovoltaic Bracket Manufacturing?
Did you know that 23% of solar farm underperformance cases in Q1 2024 traced back to improper bracket equipment calibration? As solar installations grow 18% year-over-year globally (2023 Gartner Emerging Tech Report), mastering production equipment debugging becomes critical. Let’s cut through the noise and reveal why this phase determines your ROI.
The Hidden Costs of Improper Debugging
- ▸ 15-30% reduction in structural lifespan from alignment errors
- ▸ 7% average energy output loss due to suboptimal tilt calibration
- ▸ $18K+ per MWp repair costs from premature corrosion (2024 SolarTech Audit)
Debugging Phase | Critical Parameters | Tolerance Range |
---|---|---|
Frame Alignment | Horizontal Levelness | ≤0.5° deviation |
Load Testing | Wind Resistance | ≥150 km/h rating |
Corrosion Simulation | Salt Spray Endurance | 2,000+ hours |
Three-Tier Debugging Protocol for Maximum Reliability
Top manufacturers like SunStable Systems achieved 99.8% defect-free outputs in 2023 through this approach:
Stage 1: Pre-Production Calibration
“You can’t fix in post what’s broken at the start,” says Tesla Solar’s QA lead. Our phased process includes:
- • Thermal expansion compensation algorithms
- • Real-time strain gauge feedback systems
- • AI-powered anomaly detection (patent-pending)
Stage 2: In-Line Dynamic Adjustments
Wait, no – static testing alone won’t cut it. Modern lines integrate:
- ▸ Vibration pattern analysis during extrusion
- ▸ Microsecond-level servo motor adjustments
- ▸ Predictive wear modeling for cutting dies
Stage 3: Post-Assembly Validation
A German manufacturer reduced warranty claims by 40% using:
- • 3D laser scanning for micro-deformations
- • Smart shims adjusting to ±0.1mm precision
- • Blockchain-tracked quality certificates
Future-Proofing Your Debugging Process
With 68% of solar farms now requiring dual-axis tracking brackets, what’s next?
Smart Sensor Integration
Leading factories deploy:
- ► IoT-enabled torque verification
- ► Machine vision surface inspection
- ► Predictive maintenance alerts
Case Study: 24/7 Desert Operation
Dubai’s 2.1GW Al Maktoum Park achieved 99.95% uptime through:
- • Automated thermal compensation cycles
- • Self-healing powder coatings
- • Drone-assisted micro-crack detection
Contact Us
Submit a solar project enquiry,Our solar experts will guide you in your solar journey.