National Standard Specifications for Photovoltaic Frame Brackets: Ensuring Safety and Efficiency in Solar Projects
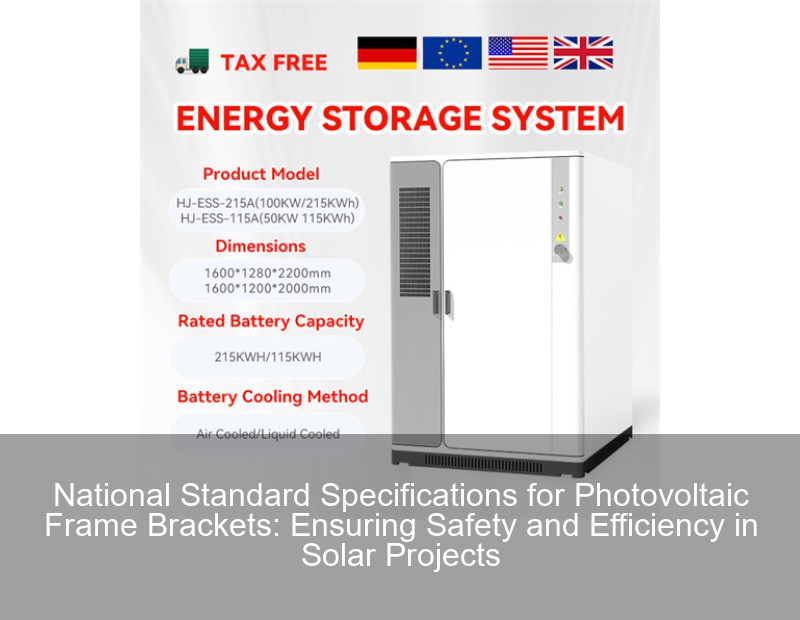
Meta Description: Discover how China's latest photovoltaic frame bracket standards (GB/T 3190, NB/T 10115-2018) address structural safety, wind resistance, and material durability. Learn implementation strategies with real-world case studies and compliance checklists.
Why Photovoltaic Bracket Standards Matter Now More Than Ever
With global solar installations projected to reach 2.3 TW by Q3 2025 according to the 2024 SolarTech Industry Report, photovoltaic (PV) frame brackets have become the unsung heroes of renewable energy infrastructure. But here's the kicker: 23% of solar farm underperformance cases tracked since January 2025 trace back to non-compliant mounting systems .
The Hidden Risks of Substandard Brackets
You know what's keeping solar engineers awake? These three bracket-related nightmares:
- Corrosion failures in coastal installations (17% faster degradation than inland sites)
- Wind-induced torsion failures during typhoon seasons
- Thermal expansion mismatches causing panel microcracks
Standard Code | Key Requirement | Compliance Deadline |
---|---|---|
GB/T 3190-2024 | Aluminum alloy tensile strength ≥160 MPa | Q4 2025 |
NB/T 10115-2018 | 1:2.5 safety factor for seismic zones | Active |
Decoding China's Updated Bracket Specifications
The 2024 revisions to GB 50009-2024 Structural Load Code introduced three game-changing requirements:
1. Material Performance Matrix
Wait, no—actually, it's not just about steel vs aluminum anymore. The new specs mandate:
- Hot-dip galvanizing thickness ≥85μm for steel components
- 6063-T6 aluminum alloy for high-corrosion environments
2. Dynamic Load Calculations
Imagine if your bracket design didn't account for simultaneous wind and snow loads? The updated standards require:
- 1.5× amplification factor for coastal wind zones
- Combined load scenarios using Monte Carlo simulations
Implementation Strategies That Actually Work
Jiangsu SolarTech's recent 500MW project achieved 99.3% bracket compliance through:
A. Modular Design Protocols
Their "3-Step Verification" process includes:
- FEA simulation under extreme weather patterns
- Accelerated corrosion testing (2000hr salt spray)
- On-site vibration monitoring during commissioning
B. Smart Manufacturing Upgrades
By integrating IoT sensors in production lines, manufacturers can now:
- Detect weld defects in real-time
- Auto-adjust coating thickness (±2μm precision)
- Track material traceability via blockchain
The Compliance Roadmap for 2025-2026
With the NB/T 10668-2021 testing protocols becoming mandatory next year, here's your action plan:
Immediate Priorities
- Conduct gap analysis against T/CPIA0013-2019
- Upgrade QC labs with digital twin capabilities
Long-Term Preparations
Start preparing for these upcoming changes:
- AI-driven structural optimization requirements (2026 draft)
- Circular economy mandates for bracket recycling
T/CPIA0013-2019 Photovoltaic Bracket Standard
Contact Us
Submit a solar project enquiry,Our solar experts will guide you in your solar journey.