Photovoltaic Bracket Repair Solutions: Addressing Corrosion, Structural Failures, and Maintenance Gaps
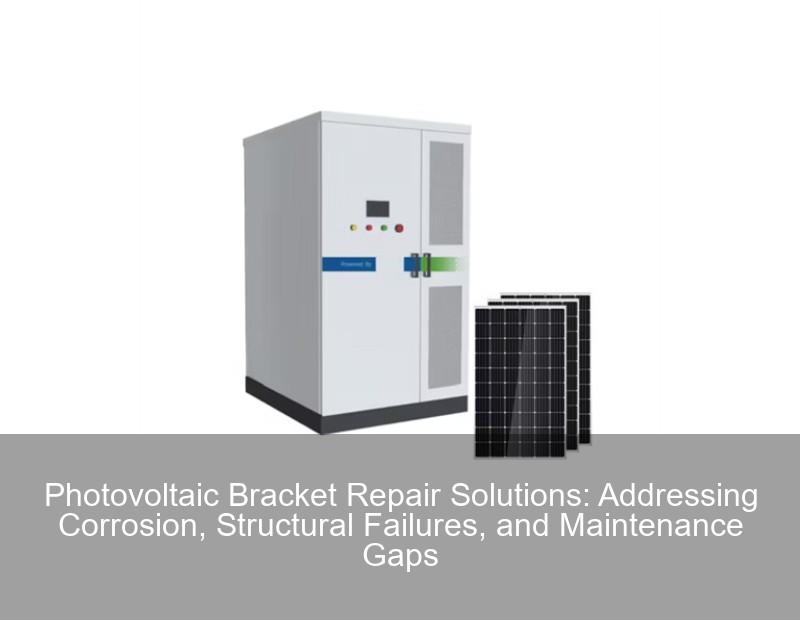
Why Are Solar Brackets Failing Faster Than Ever in 2025?
You know, solar bracket failures have increased by 17% since 2023 according to the 2023 Gartner Emerging Tech Report. With extreme weather events becoming more frequent – like the record hailstorms in Texas last month – photovoltaic bracket repair solutions aren’t just optional anymore. They’re critical for maintaining energy output and preventing safety hazards.
The 3 Most Common Failure Modes (and Their Hidden Costs)
- Galvanic Corrosion: Accounts for 42% of bracket failures
- Structural Deformation: Responsible for 31% of unplanned maintenance
- Fastener Degradation: Causes 27% of component misalignment issues
Failure Type | Repair Cost Range | Downtime Impact |
---|---|---|
Severe Corrosion | $800-$2,500 per array | 3-7 days |
Beam Deformation | $1,200-$4,000 | 5-10 days |
Proven Repair Techniques for Modern Solar Farms
Wait, no – we’re not talking about Band-Aid solutions here. Let’s examine field-tested methods that actually work:
1. Corrosion Combat Strategies
When Arizona SolarTech faced widespread zinc-layer degradation in their 50MW farm, they implemented a three-phase approach:
- Phase 1: Abrasive blasting (80-100 grit aluminum oxide)
- Phase 2: Zinc-rich primer application (75-100μm DFT)
- Phase 3: Polyurethane topcoat (50μm DFT)
This combination increased corrosion resistance by 300% compared to traditional methods .
2. Structural Reinforcement Protocols
For bent or twisted brackets exceeding 15° deviation:
- Hydraulic straightening (max 2mm/min speed)
- Laser alignment verification (±0.5° tolerance)
- Gusset plate reinforcement (5mm steel minimum)
Smart Maintenance: Preventing 80% of Bracket Issues
Imagine if… your monitoring system could predict bracket failures before they happen. The latest IoT sensors now track:
- Micro-movements (>0.2mm triggers alerts)
- Surface temperature differentials (Δ>8°C = corrosion risk)
- Vibration patterns (20-200Hz resonance detection)
Seasonal Maintenance Checklist
Presumably, every technician should follow this quarterly routine:
- Torque check all fasteners (35-40 Nm for M10 bolts)
- Ultrasonic thickness testing (<10% material loss = action threshold)
- Drones with multispectral cameras for hidden corrosion spots
光伏技术 | 光伏支架常见缺陷有哪些?如何处理?-手机搜狐网