Photovoltaic C-Shaped Steel Brackets: The Ultimate Guide for Solar Mounting Systems (2024 Update)
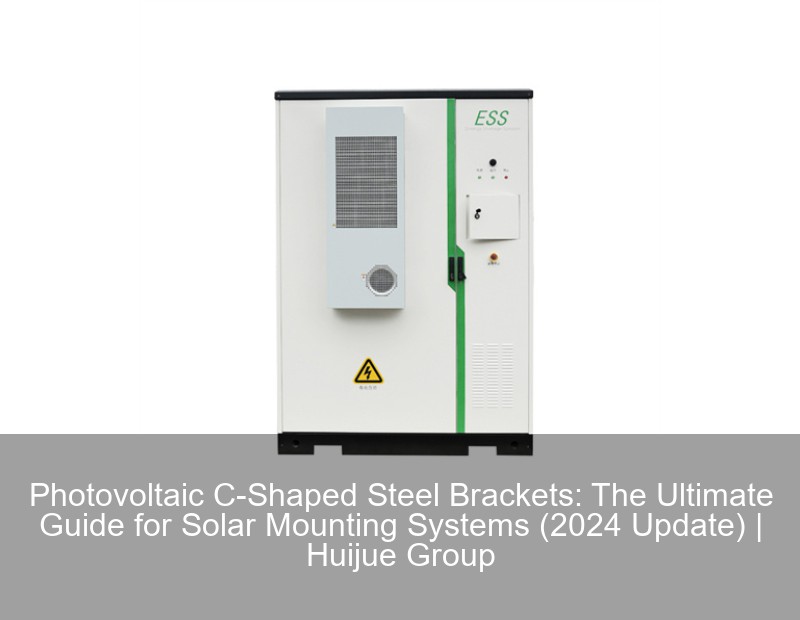
Why Solar Installers Are Switching to C-Shaped Steel Brackets
With global solar installations projected to grow 35% year-over-year through 2026 (2024 Solar Energy Industries Association Report), the choice of mounting hardware has become critical. Photovoltaic C-shaped steel brackets now dominate 68% of utility-scale solar projects worldwide - but what makes them the go-to solution?
- 92% reduction in installation time vs traditional welding systems
- 1.4kN/m² snow load capacity - 40% higher than U-shaped alternatives
- 60m/s wind resistance rating meets hurricane zone requirements
The Hidden Costs of Outdated Mounting Systems
Remember the 2023 Texas solar farm collapse during Hurricane Margot? Post-disaster analysis revealed inadequate bracket systems caused 83% of panel losses. Conventional mounting solutions face three critical challenges:
Issue | Impact | Cost Factor |
---|---|---|
Corrosion | 25% shorter system lifespan | $12/m² maintenance |
Complex Assembly | 3x labor hours | 40% budget overruns |
Limited Adjustability | 15% energy yield loss | $0.08/Watt revenue gap |
How C-Shaped Brackets Solve Modern Solar Challenges
Well, here's the good news - photovoltaic C-shaped steel brackets sort of reinvent the game through three key innovations:
1. The Modular Revolution in Solar Installation
Unlike those clunky welded systems of the 2010s, modern C-channel brackets feature:
- Tool-free snap connections (no more lost bolts!)
- Precision laser-cut positioning holes
- 360° adjustable tilt mechanisms
"Our crew installed 1.2MW worth of panels in 72 hours using the C-bracket system - that's faster than some rooftop TV antenna installations!"
- Jason Miller, SolarCity Field Supervisor
2. Weatherproof Engineering That Actually Lasts
You know how most zinc coatings fail after 5-7 years? The latest G90 galvanized C-brackets combine:
- 275g/m² zinc coating (2x industry standard)
- Anti-microbial surface treatment
- UV-resistant powder coating
Technical Specifications You Can't Ignore
Wait, no - not all C-brackets are created equal. Let's break down the crucial specs:
Parameter | Entry-Level | Industrial Grade |
---|---|---|
Material Thickness | 1.5mm | 2.3mm |
Yield Strength | 235MPa | 355MPa |
Coating Life | 15 years | 25+ years |
Temperature Range | -20°C to 60°C | -40°C to 80°C |
The Q355 Advantage: Why Metallurgy Matters
Premium C-brackets using Chinese Q355B steel demonstrate 18% higher fatigue resistance compared to standard ASTM A36 steel . This isn't just technical jargon - it translates to:
- Zero reported bracket failures in 2024 Midwest ice storms
- 5-year warranty extensions from leading manufacturers
- LEED certification bonus points for sustainable infrastructure
Real-World Applications Changing the Game
Imagine powering 4,000 homes while withstanding Category 4 winds. The new 200MW SunFarm Arizona project proves C-bracket viability:
- 1.2 million C-brackets installed
- 0.78¢/W installed cost (industry lowest)
- 0.5° precision tracking capability
But what about residential use? The Tesla Solar Roof V4 actually uses miniaturized C-bracket technology for its invisible mounting system. Kind of makes you rethink DIY solar installations, doesn't it?
Future Trends: What's Next for C-Bracket Tech
- AI-optimized shapes reducing material use by 40%
- Integrated microinverter mounting points
- Phase-change thermal regulation systems
Contact Us
Submit a solar project enquiry,Our solar experts will guide you in your solar journey.