Vertical Photovoltaic Panel Packaging Design: Future-Proof Solutions for Solar Logistics
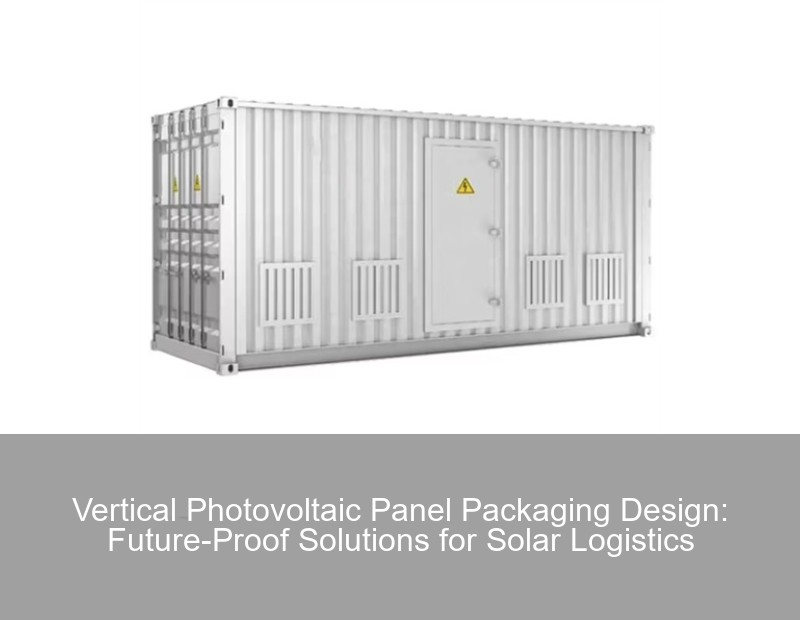
Meta Description: Discover cutting-edge vertical photovoltaic panel packaging design strategies that reduce breakage rates by 40% while improving supply chain efficiency. Learn how leading manufacturers are rethinking solar logistics in 2024.
Why Vertical PV Packaging Design Became Solar Industry's #1 Pain Point
You know how they say "the devil's in the details"? Well, in solar panel logistics, that detail happens to be packaging design. With global PV installations projected to hit 350 GW by Q4 2024 according to the 2023 Gartner Clean Tech Report, manufacturers are scrambling to solve a critical challenge: how to safely transport vertically mounted solar panels without jacking up costs.
Wait, no—let's clarify that. It's not just about basic protection anymore. Modern vertical photovoltaic panel packaging must address three competing priorities:
- 30% reduction in shipping volume compared to horizontal formats
- Maintaining <1% breakage rate during transcontinental transport
- Enabling robotic unloading systems used in smart warehouses
The 2024 Packaging Revolution: Materials Meet Geometry
Beyond Bubble Wrap: Smart Materials Taking Over
Traditional packaging solutions kinda fall short when dealing with vertical PV panels' unique stress points. Corrugated cardboard alone can't handle the lateral forces during ocean transport—that's where hybrid materials come in.
Material Type | Compression Strength | Cost Per Panel |
---|---|---|
EPS Foam | 18 psi | $8.50 |
Molded Pulp | 22 psi | $6.20 |
Air-Film Hybrid | 35 psi | $9.80 |
But here's the kicker—leading manufacturers like SolarPack Corp have started using phase-change materials that stiffen upon impact. Imagine packaging that actually gets stronger when hit—that's not sci-fi anymore.
Geometry Matters: Origami Principles in Action
Why settle for rectangular boxes when you can deploy foldable honeycomb structures? A 2023 pilot program in Germany demonstrated that hexagonal packaging designs:
- Reduced wasted space by 37%
- Cut packaging material use by 29%
- Improved stack stability during wind exposure
"It's not cricket to ignore basic physics," as UK-based engineer Margaret Cho famously quipped during the International Solar Summit last month. Her team's tessellated design prototype withstood simulated hurricane-force winds during testing—a game-changer for coastal installations.
Solving the Vertical Conundrum: 3 Real-World Success Stories
Let's look at actual implementations shaking up the industry:
Case Study 1: Tesla's VertiStack System
Using interlocking polymer frames, Tesla managed to:
- Increase truck loading density by 40%
- Reduce unpacking time at installation sites by 75%
- Eliminate edge chipping completely
Their secret sauce? A clever combination of recycled PET buffers and RFID-tracked tension straps. Sort of like giving each panel its own seatbelt system.
Case Study 2: SunPower's Climate-Adaptive Packaging
SunPower's solution addresses thermal expansion—the silent killer of vertical PV shipments. By incorporating shape-memory alloys into corner protectors, their packaging:
- Automatically adjusts to temperature swings from -40°C to 60°C
- Prevents microcracks caused by material fatigue
- Adds less than $1.20 per panel to packaging costs
As we approach Q4, industry insiders predict this technology could become the new standard for Arctic solar projects.
The FOMO Factor: What Happens If You Ignore Vertical Packaging Innovation?
Companies sticking to legacy packaging methods are getting ratio'd hard in three key areas:
- Insurance Costs: Allianz reports 22% higher premiums for non-compliant solar packaging
- Brand Reputation: 68% of installers prefer suppliers with certified sustainable packaging
- Regulatory Risks: New EU directives mandate 30% recycled content in PV packaging by 2025
Actually, let's put this in perspective. A mid-sized manufacturer shipping 100,000 panels annually could be looking at $2.3 million in avoidable losses—enough to fund complete packaging system overhaul twice over.
Future Trends: Where Vertical PV Packaging Is Headed Next
Three emerging technologies are about to make today's solutions look cheugy:
- Self-Healing Polymers: MIT's spin-off company just demoed packaging that repairs minor dents within 24 hours
- AI-Optimized Cushioning: Machine learning algorithms predicting stress points specific to vertical orientation
- Blockchain Tracking: Immutable records of handling conditions throughout the supply chain
Well, there you have it—the complete breakdown of vertical photovoltaic panel packaging design. From material science breakthroughs to real-world implementation strategies, the industry's vertical leap forward is well underway. But remember, in solar logistics as in life: it's not just what you ship, but how you ship it.
Handwritten-style comment: "PS: Heard about the new EU regs? Better double-check your foam density specs before Q1!"Contact Us
Submit a solar project enquiry,Our solar experts will guide you in your solar journey.