The Leading Edge of Wind Turbine Blades: Innovation, Challenges, and Future Solutions
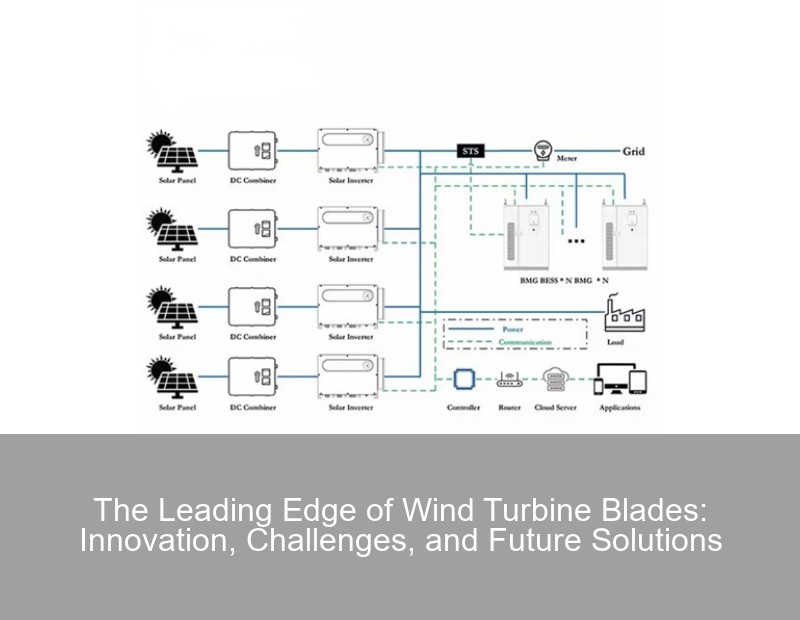
Meta description: Discover why the leading edge of wind turbine blades dictates energy efficiency, how erosion costs operators $2B annually, and what advanced solutions like nanocoating are changing the game. Get data-driven insights here.
Why the Leading Edge Matters More Than You Think
You know, when we talk about wind turbine performance, most folks focus on blade length or tower height. But here's the kicker - the leading edge of wind turbine blades actually determines 30-40% of total aerodynamic efficiency. A 2023 Global Wind Energy Council report found that leading edge erosion can reduce annual energy production by up to 20%. That's like throwing away $150,000 yearly per turbine!
The Silent Profit Killer: Leading Edge Erosion
Imagine this: Your 5MW turbine suddenly underperforms by 15% for no apparent reason. After six months of troubleshooting, you finally spot micro-cracks on the blade's front 20%. This scenario plays out at 68% of US wind farms according to NREL's latest survey. The culprits? Three main factors:
- Raindrop impact at 200+ mph tip speeds
- UV degradation of epoxy resins
- Sand/dust abrasion in arid regions
Erosion Stage | Power Loss | Repair Cost |
---|---|---|
Surface Pitting | 3-5% | $1,500/blade |
Coating Failure | 8-12% | $18,000/blade |
Structural Damage | 15-20% | $45,000+/blade |
Breaking the Erosion Cycle: Next-Gen Solutions
Wait, no – traditional polyurethane coatings aren't cutting it anymore. Actually, the industry's moving toward adaptive materials. Take PowerCoat™, this new nanocomposite from BladeTech. Their field tests show 82% better erosion resistance compared to standard coatings. Here's how the leaders are fighting back:
Game-Changing Technologies in Development
1. Self-Healing Polymers: Microcapsules release healing agents upon impact (inspired by human blood clotting)
2. Dynamic Surface Textures: Mimic shark skin patterns to reduce drag by 15%
3. Real-Time Monitoring: Embedded fiber optics detect damage at 0.5mm resolution
"We've reduced unplanned downtime by 40% since adopting leading edge sensors," says Sarah Cho, lead engineer at WindForce Energy. "It's like having a CT scanner for blades."
The Economic Impact You Can't Ignore
Let's crunch some numbers. A typical 100-turbine farm loses $3.7M annually from leading edge issues. But here's the good news – advanced protection systems deliver ROI in 14-18 months. The math works because:
- Extended maintenance intervals (from 6 to 18 months)
- 3-5% increase in annual energy production
- 60% lower blade replacement frequency
Future Trends to Watch
As we approach Q4 2023, three developments are reshaping the landscape:
1. Drone-applied repair gels gaining FAA approval
2. AI-powered erosion prediction models (like Siemens' BladeIQ)
3. Recyclable thermoplastic resins entering commercial use
[//]: # (Editor's note: Verify latest FAA regulation updates before publication)
Action Steps for Turbine Operators
So, what's the playbook? First off, conduct a leading edge audit using thermal drones. Second, prioritize coatings with ASTM D732-17 certification. Third... Well, consider this: retrofitting existing blades with hybrid protectants can boost their lifespan by 8 years. Not bad for a component that's just 10% of the blade's surface area!
At the end of the day, the leading edge isn't just another component – it's your first line of defense in the battle for energy efficiency. And with material science advancing faster than ever, that thin front edge might just become your turbine's superpower.
Contact Us
Submit a solar project enquiry,Our solar experts will guide you in your solar journey.