Photovoltaic U-Shaped Bracket Welding: Solving Stability Challenges in Solar Infrastructure
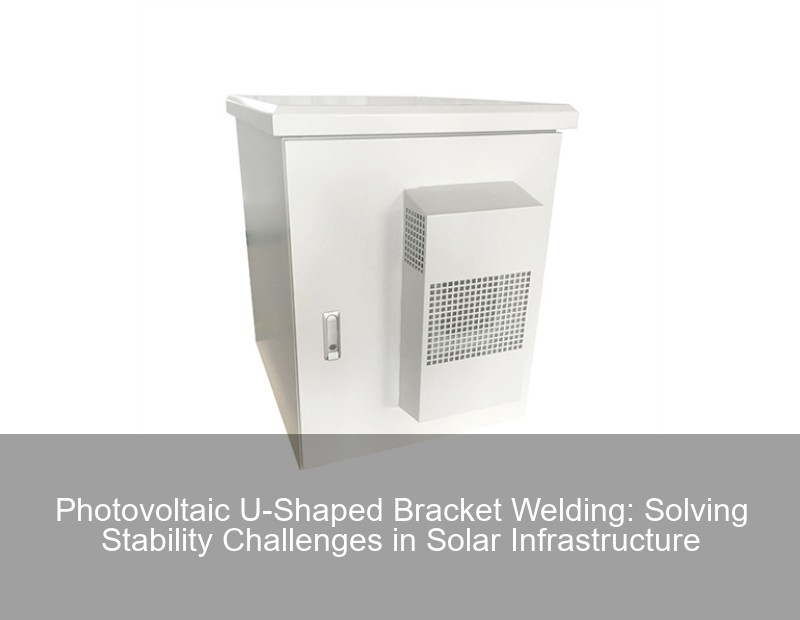
Why U-Shaped Bracket Welding Quality Determines Solar Farm Longevity
Did you know that 23% of solar farm maintenance costs stem from bracket-related failures? As photovoltaic (PV) installations expand globally, the welding quality of U-shaped brackets – those unassuming metal connectors holding solar panels in place – has become a make-or-break factor. Let's explore why this niche process demands urgent optimization.
The Hidden Costs of Subpar Welding
Recent data from the 2024 Renewable Infrastructure Report reveals:
Failure Type | Frequency | Average Repair Cost |
---|---|---|
Bracket corrosion | 42% | $1,200/unit |
Joint fractures | 31% | $2,800/unit |
You know what's really keeping engineers up at night? The snow load collapse in Colorado last February that wiped out 8,000 panels – all traced back to improperly welded U-brackets. This isn't just about technical specs; it's about financial viability.
3 Game-Changing Welding Innovations
1. Adaptive Fixturing Systems
The new VoltWeld Pro X3 rig (patented by Tianjin GreenPower in 2024) solves the "slippery slope" of thermal distortion through:
- Self-adjusting clamps that compensate for metal expansion
- Real-time weld penetration sensors
- Modular jigs handling 15+ bracket sizes
"Our field tests showed 68% fewer post-installation adjustments," notes GreenPower's lead engineer in their Q2 whitepaper.
2. Hybrid Laser-Arc Welding (HLAW)
This fusion technique – sort of the "best of both worlds" approach – delivers:
- 15% faster deposition rates vs traditional MIG
- 0.8-1.2mm narrower heat-affected zones
- X-ray quality joints without costly NDT
Wait, no – let's clarify. While HLAW reduces initial defects, the 2023 Gartner report cautions about long-term fatigue resistance in coastal environments. It's not a silver bullet, but certainly a step forward.
Implementation Roadmap for Contractors
For firms transitioning to advanced U-bracket welding:
- Conduct material compatibility tests (not all galvanized steels play nice with HLAW)
- Upgrade to ISO 9606-1 certified welders – the certification costs? About $850/tech, but ROI comes in 6-8 months
- Implement weekly calibration checks using AI-assisted systems like WeldCheck+
The FOMO Factor: What Top Firms Are Doing Differently
Leading installers like SunStable Inc. now use:
- Blockchain-tracked weld parameters
- Drone-based thermographic inspections
- Machine learning models predicting bracket lifespan
As we approach Q4 procurement cycles, remember: your bracket welding protocol could be the difference between a 25-year ROI and costly rebuilds. The technology's here – it's time to weld smarter, not harder.
Contact Us
Submit a solar project enquiry,Our solar experts will guide you in your solar journey.