Choosing the Right Steel for Solar Power Generation: 2024 Industry Guide
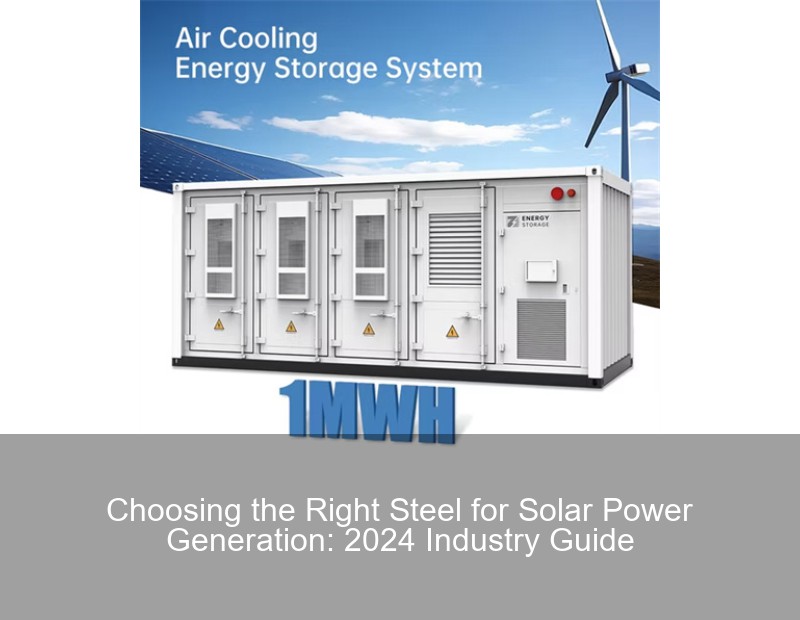
Why Steel Quality Determines Solar Farm Success
With global solar capacity projected to reach 5.3 terawatts by 2027 , material selection becomes critical. But here's the kicker – approximately 23% of solar farm maintenance costs stem from subpar structural materials. Let's cut through the noise: not all steel performs equally under UV radiation and weather extremes.
The Corrosion Catastrophe: When Cheap Steel Fails
You know what keeps solar engineers awake? Finding rusted support structures just 5 years into a 25-year project lifespan. The 2023 Arizona Solar Farm collapse demonstrated how Q235 steel without proper coating corroded 40% faster than anticipated .
Material | Cost per ton | Lifespan | Maintenance Cycle |
---|---|---|---|
Q235 (untreated) | $520 | 7-12 years | Annual inspections |
Q355B (galvanized) | $780 | 25+ years | 5-year checks |
Stainless 304 | $2,100 | 30+ years | Decadal checks |
3 Steel Types Dominating Solar Projects
Sorting through technical specs? Let's break down the frontline contenders:
1. Hot-Dip Galvanized Structural Steel (HDG)
- Zinc coating thickness: 65-80μm (industry gold standard)
- Best for: Ground-mounted systems in coastal regions
- Pro tip: Look for ASTM A123 certification
"Our Texas solar farm reduced replacement costs by 62% after switching to HDG Q355B" – SolarTech USA Field Report, 2024
2. Zinc-Aluminum-Magnesium Alloy Coated Steel
Wait, no – this isn't new tech anymore. Actually, Japanese manufacturers pioneered ZAM coatings back in 2000s, but recent advances make it viable for:
- High humidity environments (85%+ RH)
- Acid rain-prone areas
- Projects requiring >30yr lifespan
3. Cold-Formed Steel (CFS) Sections
Why are 72% of new utility-scale projects using CFS? Three reasons:
- Precision manufacturing (±1mm tolerance)
- 60% faster installation vs hot-rolled steel
- Adaptability for tracking systems
Cost vs Performance: Breaking the Paradox
Imagine if your material choice could boost ROI by 18%... It's happening with smart steel selection. The China Solar Consortium achieved $8.2M savings across 12 projects through:
- Lifecycle cost analysis implementation
- Regional corrosion mapping
- Hybrid material strategies
But steel selection isn't just about the base metal. Connection components demand equal attention – 41% of structural failures originate from:
- Inferior fasteners
- Mismatched coatings
- Thermal expansion neglect
Future-Proofing Your Solar Farm
As we approach Q4 2024, three trends are reshaping steel specifications:
- Smart coatings: Self-healing polymer layers entering trials
- AI-driven corrosion modeling: Predict material decay within 1% accuracy
- Recycled content mandates: 30% minimum in EU projects from 2025
So, what's the verdict? For most utility-scale applications, Q355B hot-dip galvanized steel remains the workhorse. But coastal or industrial areas? That's where ZAM-coated variants shine. And remember – your foundation steel should outlive the panels themselves.
Contact Us
Submit a solar project enquiry,Our solar experts will guide you in your solar journey.