Photovoltaic Support Material Production Equipment: Key Challenges and Advanced Solutions for Solar Manufacturing
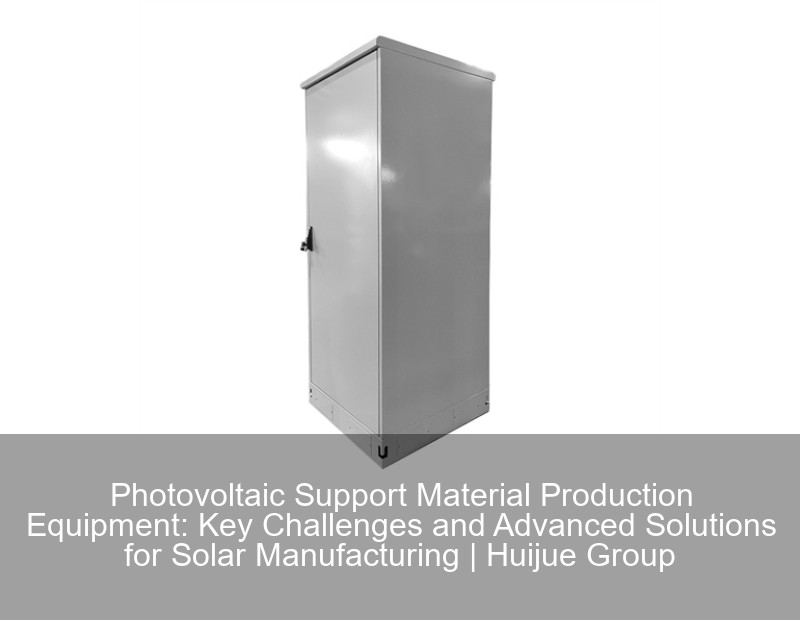
Why Photovoltaic Support Material Production Is Critical for Solar Energy Expansion
As global solar capacity approaches 1.5 terawatts by 2025 , the demand for efficient photovoltaic (PV) support material production equipment has skyrocketed. But here's the catch: nearly 23% of solar manufacturers still struggle with outdated machinery that limits material utilization rates below 80% . Let’s unpack the challenges and explore cutting-edge solutions shaping this $4.7 billion equipment market .
The Hidden Bottlenecks in PV Material Manufacturing
You know, many factories still operate like it's 2015. Three critical pain points dominate the industry:
- Material waste: Conventional cutting systems lose 12-18% of silicon wafers
- Energy intensity: 40% of production costs stem from power-hungry processes
- Quality inconsistencies: Manual handling causes 7% defect rates in anti-reflective coatings
Parameter | Legacy Equipment | Advanced Systems |
---|---|---|
Material Utilization | 78% | 94% |
Energy Consumption/kWh per panel | 18.7 | 9.3 |
Breakthrough Technologies Redefining Production Standards
Wait, no – it's not all doom and gloom. The 2024 SolarTech Manufacturing Report highlights three game-changers:
1. AI-Driven Material Deposition Systems
Imagine if your coating machines could self-optimize in real-time. The new NovaTrack X7 series uses predictive algorithms to:
- Reduce silver paste consumption by 22%
- Maintain coating uniformity within ±0.3μm
2. Modular Production Platforms
Leading Chinese manufacturers like Trina Solar have adopted plug-and-play equipment clusters that cut deployment time from 18 months to 6 . These systems feature:
- Standardized material interfaces
- Cloud-based process monitoring
The Sustainability Imperative: Beyond Cost Savings
Actually, there's more at stake than just profit margins. Recent EU regulations mandate 95% material recyclability in PV production by 2027 . This pushes manufacturers toward:
- Closed-loop cooling systems
- Dry etching technologies
Case in point: Canadian Solar's EcoFab line achieved Zero Liquid Discharge through advanced filtration membranes – a 38% water reduction compared to traditional methods .
Future-Proofing Your Production Line
As we approach Q4 2025, smart factories are integrating:
- Digital twin simulations
- Automated quality assurance drones
- Blockchain-based material tracing
Well, the path forward is clear. Manufacturers adopting these advanced photovoltaic support material production systems aren't just surviving – they're redefining solar energy economics. The question isn't if to upgrade, but how quickly it can be done without disrupting current operations.
Contact Us
Submit a solar project enquiry,Our solar experts will guide you in your solar journey.