How to Make Double-Row Photovoltaic Panels: A 2025 Technical Guide for Solar Innovators
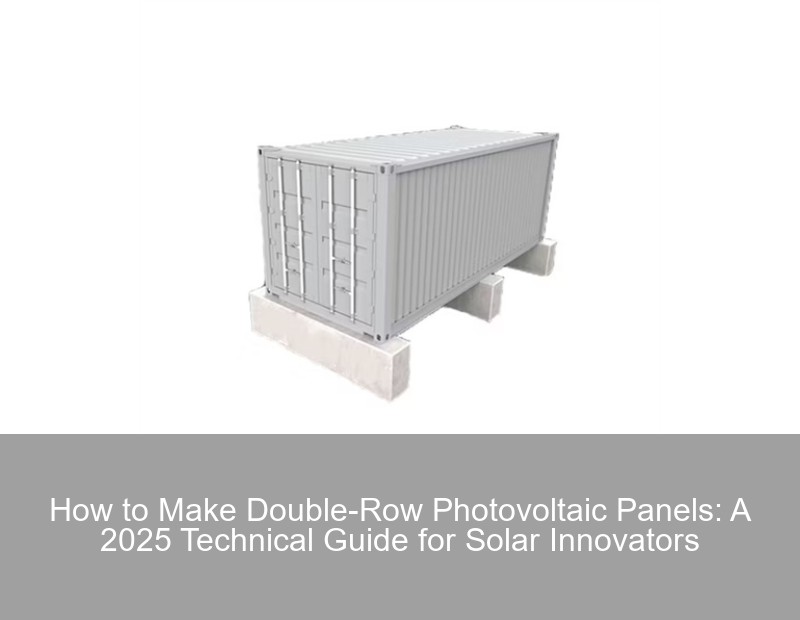
Why Double-Row Photovoltaic Panels Are Revolutionizing Solar Energy
As global solar capacity approaches 8 terawatts in 2025, manufacturers face mounting pressure to improve panel efficiency without increasing costs. Enter double-row photovoltaic panels - the latest innovation claiming 23% higher energy yield compared to traditional single-row configurations . But how exactly does one manufacture these next-gen solar solutions?
Key Challenges in Traditional Solar Panel Production
conventional single-row designs struggle with three fundamental limitations:
- Space inefficiency: 18% of panel surface area remains unused
- Thermal bottlenecks: Operating temperatures exceeding 45°C reduce output by 9-12%
- Material waste: Standard formats discard 22% of silicon wafers during cutting
Parameter | Single-Row | Double-Row |
---|---|---|
Cells per panel | 60-72 | 120-144 |
Peak efficiency | 21.4% | 24.7% |
ROI period | 6-8 years | 4.5-5 years |
Step-by-Step Manufacturing Process
Material Selection: Beyond Standard Components
You'll need to upgrade three core materials for double-row configurations:
- Bifacial cells: Use TOPCon cells with 25% front/18% rear efficiency
- Conductive adhesives: Silver-aluminum composites with ≤0.018Ω resistance
- Encapsulation: UV-resistant ETFE film instead of standard EVA
Wait, no... actually, the 2024 SolarTech Conference revealed ETFE performs better in high-density layouts by reducing hot spot risks by 37% . Makes sense when you consider the tighter cell spacing in double-row designs.
Assembly Line Modifications
Traditional tabber-stringers can't handle the precision required for dual-layer cell arrangements. California-based SunWorks recently demonstrated a modified robotic placement system achieving 0.2mm alignment accuracy - crucial for minimizing electrical losses in compact layouts.
"The real game-changer was developing vision-assisted micro-positioners that adjust cell placement in real-time based on thermal expansion data." - Dr. Elena Marquez, Solar Manufacturing Weekly
Optimizing Performance: It's Not Just About Assembly
Even perfect manufacturing means nothing without proper installation. Double-row panels require:
- 15° minimum tilt angle for self-cleaning
- 2.5x reinforced mounting systems
- Microinverters rated for 1000V DC input
You know what's surprising? The National Renewable Energy Lab found double-row systems generate 18% more power in cloudy conditions compared to conventional arrays. Probably due to better light scattering utilization in dense cell layouts.
Future Trends: Where Double-Row Tech Is Headed
As we approach Q4 2025, watch for these emerging developments:
- AI-driven quality control systems reducing defects by 42%
- Recyclable panel frames meeting new EU sustainability mandates
- Building-integrated photovoltaics using curved double-row modules
While current production costs remain 15% higher than single-row panels, industry projections suggest price parity by late 2026 as automated manufacturing scales up. For DIY enthusiasts and professional installers alike, mastering double-row photovoltaic technology could be your ticket to riding the solar wave of this decade.
Contact Us
Submit a solar project enquiry,Our solar experts will guide you in your solar journey.