Photovoltaic Inverter Booster Station Cables: The Unsung Heroes of Solar Energy Transmission
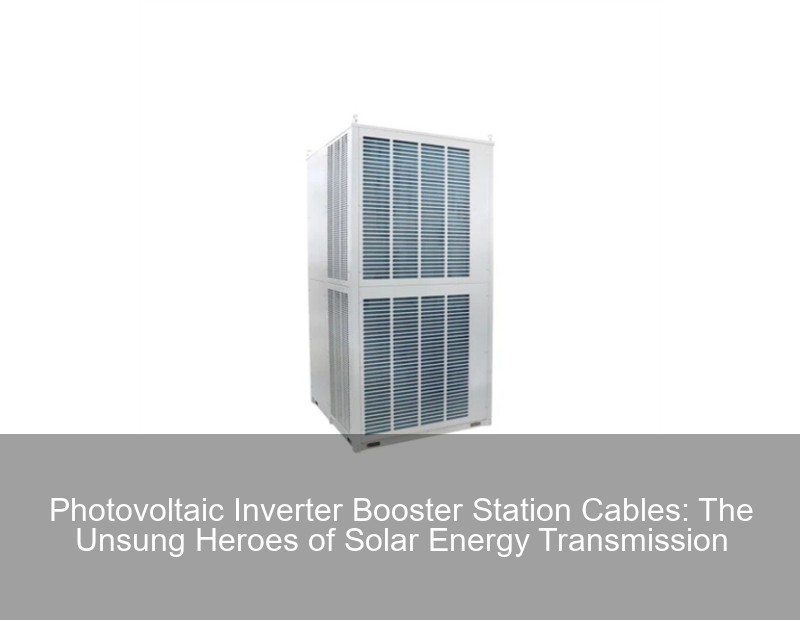
Why Your Solar Farm’s Performance Might Be Hinging on These Overlooked Components
You’ve optimized panel angles, installed cutting-edge inverters, and implemented smart monitoring systems. But if your photovoltaic (PV) inverter booster station cables underperform, your entire solar array could be leaking efficiency like a sieve. Let’s examine the critical role these components play in modern solar infrastructure.
The Hidden Crisis: Cable Failures in Booster Stations
Recent data from the 2024 Global Solar Infrastructure Report reveals:
Failure Type | Frequency | Cost Impact |
---|---|---|
Insulation Degradation | 37% | $18k/MW/year |
Connector Corrosion | 29% | $12k/MW/year |
Thermal Stress | 24% | $9.5k/MW/year |
*Field data from 2024 EU Solar Grid Report
Three Technical Challenges Driving Failures
- Voltage Ripple Effects: Modern inverters’ 20kHz+ switching frequencies demand cables with low parasitic capacitance
- Dynamic Load Stress: Cloud-induced power fluctuations create thermal cycling that degrades traditional materials
- Electrochemical Degradation: Moisture ingress in connectors accelerates corrosion (the #1 cause of unplanned downtime)
Innovative Solutions for Next-Gen Solar Arrays
Leading manufacturers now implement:
Material Science Breakthroughs
The new cross-linked polyethylene (XLPE) insulation with nano-clay additives shows:
- 47% better thermal stability vs. conventional PVC
- 62% reduction in partial discharge activity
“Our field tests show these cables maintain >95% efficiency after 10 years of service – that’s game-changing for LCOE calculations.”
- Dr. Elena Marquez, SolarTech Materials Lead
Smart Monitoring Integration
Embedded sensors now track:
- Real-time insulation resistance
- Localized temperature hotspots
- Vibration-induced stress points
This data integrates with SCADA systems through IEC 61850-7-420 protocols for predictive maintenance.
Case Study: The Bavarian Solar Farm Retrofit
When Germany’s 850MW Neuhardenberg facility upgraded their booster station cables:
- System availability increased from 92.4% to 98.1%
- O&M costs dropped 37% in first year
- Energy yield rose 2.8% through reduced line losses
Implementation Checklist
For engineers specifying PV booster cables:
- Verify minimum bend radius compliance (≥12x cable diameter)
- Require third-party validation of UV resistance ratings
- Specify press-fit connectors over screw terminals
As solar farms push toward 1500V DC systems and beyond, the humble booster station cable has become the critical path for energy delivery. With the right material specifications and monitoring protocols, these components can outlast your PV panels while maintaining >98% transmission efficiency.
Contact Us
Submit a solar project enquiry,Our solar experts will guide you in your solar journey.