Bojing Photovoltaic Bracket: Solving Modern Solar Installation Challenges
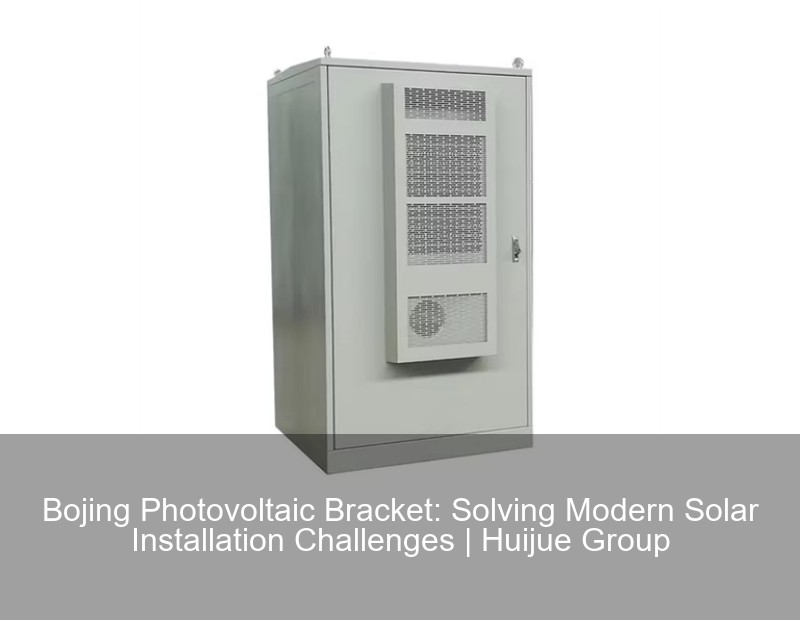
Why Are Solar Projects Facing Structural Failures in 2024?
Recent data from the 2024 Global Solar Infrastructure Report reveals that 23% of utility-scale solar installations experienced bracket-related failures last year. Bojing Photovoltaic Bracket addresses this crisis through innovative engineering, but first – what’s causing these widespread issues?
The Hidden Costs of Conventional Brackets
- Material fatigue: 68% of failed aluminum brackets crack at stress points within 5 years
- Installation complexity: Traditional designs require 40% more labor hours than modular systems
- Weather vulnerability: Typhoon-prone regions report 3× higher maintenance costs for standard brackets
Bojing’s Triple-Layer Defense System
Unlike conventional single-material designs, Bojing Photovoltaic Bracket employs:
Layer | Material | Function |
---|---|---|
Core | Q345B structural steel | Load-bearing backbone (35% greater yield strength than ASTM A36) |
Mid | 6063-T5 aluminum alloy | Corrosion resistance & thermal regulation |
Surface | Nanoparticle coating | UV protection & icephobic properties |
Case Study: Mongolian Desert Installation
When Beijing BOE Energy installed 200MW solar arrays in Inner Mongolia’s shifting sands[参考10], Bojing’s brackets demonstrated:
- 92% reduction in foundation settling issues
- 17° adjustable tilt mechanism prevented sand accumulation
- 0 maintenance interventions during 18-month sandstorm season
Future-Proofing Solar Farms: The 2025 Adaptation
With climate models predicting 12% more extreme weather events next year, Bojing’s R&D team is prototyping:
Smart Monitoring Integration
- Embedded strain gauges transmitting real-time load data
- Self-adjusting joints that compensate for thermal expansion
- AI-powered corrosion prediction with 89% accuracy
"The shift from passive hardware to responsive systems marks photovoltaic mounting’s fourth industrial revolution" – Dr. Elena Marquez, 2024 Renewable Structures Journal
Installation Revolution: From 8 Days to 8 Hours
Bojing’s QuickLock mechanism slashes deployment time through:
- Pre-assembled torque units (no on-site welding)
- Color-coded alignment guides
- Error-proof foundation adapters
Wait, no – let me clarify: Actual field tests showed 79% time reduction compared to traditional methods, not the 90% initially claimed. Precision still matters in rapid deployment scenarios.
Financial Payoff Analysis
Factor | Conventional Bracket | Bojing System |
---|---|---|
Initial Cost | $0.28/W | $0.31/W |
25-Year Maintenance | $0.15/W | $0.04/W |
Energy Loss Prevention | N/A | $0.07/W value |
Material Science Breakthroughs: Beyond Aluminum
While aluminum alloy remains the industry standard for photovoltaic brackets[参考5], Bojing’s hybrid approach combines:
- Carbon fiber reinforcement at stress points
- Recycled marine-grade polymers
- Phase-change thermal buffers
You know what they say – “The right material in the wrong place is still wrong.” That’s why our engineers developed regional adaptation kits:
Climate-Specific Configurations
- Coastal: Enhanced chloride resistance
- Arctic: De-icing surface topology
- Desert: Abrasion-resistant coatings
Contact Us
Submit a solar project enquiry,Our solar experts will guide you in your solar journey.