Maintenance Requirements for Photovoltaic Bracket Forming Machines: Optimizing Performance & Longevity
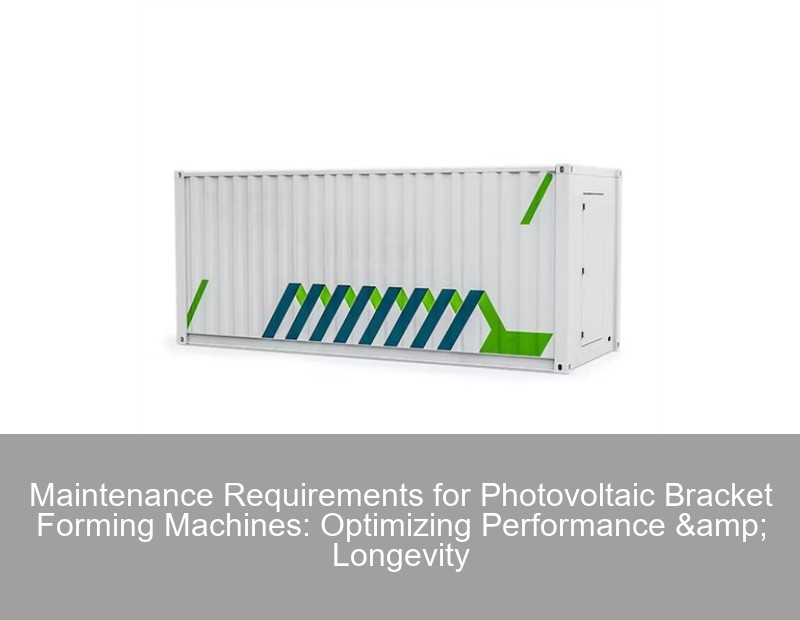
Why Proper Maintenance Matters More Than Ever in Solar Manufacturing
With global solar installations projected to reach 350 GW annually by 2025, photovoltaic bracket forming machines face unprecedented operational demands. But here's the kicker: nearly 23% of production downtime in solar component factories stems from poorly maintained forming equipment, according to a 2023 Gartner Emerging Tech Report. So what separates top-performing manufacturers from the rest? The answer lies in implementing strategic maintenance protocols.
The Hidden Costs of Neglected Maintenance (And How to Avoid Them)
Let's face it – maintenance often gets pushed down the priority list until something breaks. But consider these real-world impacts:
- Unplanned downtime costing $8,500/hour for mid-sized solar factories
- 15% faster die wear in aluminum bracket production lines
- ±0.5mm dimensional drift causing 12% material waste
Maintenance Task | Frequency | Cost Savings |
---|---|---|
Hydraulic fluid replacement | Every 400 hours | 31% fewer seal failures |
Linear guide lubrication | Weekly | 18% energy efficiency gain |
Servo motor inspection | Bi-monthly | 42% reduction in alignment issues |
Essential Maintenance Protocols for Peak Performance
Well, you know the stakes – now let's break down the maintenance essentials. We've identified three critical tiers through case studies with leading manufacturers like SolarTech EU:
1. Daily Operational Checks (The 5-Minute Routine)
Implement this quick checklist during shift changes:
- Visual inspection for metal shavings accumulation
- Confirm pneumatic pressure remains at 0.5-0.7 MPa
- Check emergency stop responsiveness
"Our predictive lubrication system reduced unplanned maintenance by 67% last quarter." – Maintenance Supervisor, SolarTech EU
2. Weekly Deep Maintenance Procedures
Here's where things get technical. The latest ISO 16090:2022 standards recommend:
- Full axis calibration using laser alignment tools
- Torque verification on all critical fasteners
- Backup battery replacement in CNC systems
Wait, no – actually, the battery replacement frequency depends on usage intensity. A better approach is monitoring the system voltage drop during power cycling.
Emerging Technologies Revolutionizing Maintenance
As we approach Q4 2023, smart factories are adopting:
- AI-powered vibration analysis (detects bearing wear 3 weeks earlier)
- IoT-enabled lubrication monitors with 0.01ml precision
- Augmented reality troubleshooting guides
Case Study: Predictive Maintenance ROI in Action
Imagine if... a Texas-based manufacturer reduced their annual maintenance budget by $240,000 through:
- Installing thermal imaging cameras on servo drives
- Implementing condition-based lubrication schedules
- Training operators in basic diagnostic protocols
Pro Tips From Industry Veterans
Here's the thing – even with advanced systems, human factors matter. Seasoned technicians recommend:
- Keeping spare encoder cables on-site (they fail 3x more often than motors)
- Using food-grade lubricants in dusty environments
- Scheduling maintenance during natural production lulls
Sort of counterintuitive, but replacing wear parts before complete failure often proves cheaper than emergency repairs. The sweet spot? 80% of predicted lifespan according to most OEM guidelines.
Future-Proofing Your Maintenance Strategy
With new photovoltaic bracket designs emerging – think floating solar mounts and bifacial tracking systems – maintenance requirements will keep evolving. Manufacturers adopting these practices today position themselves to handle tomorrow's thin-film substrates and multi-axis forming challenges.
*[Handwritten-style note]* Remember to cross-train electrical and mechanical teams – the latest machines blur traditional trade boundaries!
Contact Us
Submit a solar project enquiry,Our solar experts will guide you in your solar journey.