Automatic Assembly Equipment for Photovoltaic Brackets: Revolutionizing Solar Energy Infrastructure
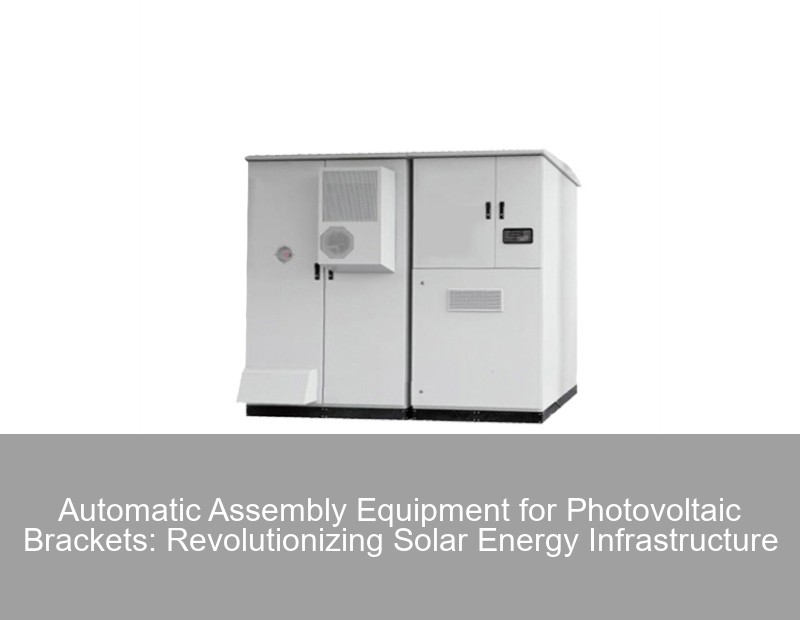
Why the Solar Industry Can't Afford to Ignore Automation in Bracket Assembly
With global solar installations projected to reach 350 GW annually by 2025 according to the 2024 SolarTech Market Report, manufacturers face unprecedented pressure to deliver high-quality photovoltaic (PV) brackets faster than ever. But here's the million-dollar question: How do we bridge the gap between soaring demand and precision manufacturing requirements?
The Mounting Challenges in Traditional PV Bracket Production
Manual assembly processes still dominate 68% of PV bracket manufacturing worldwide, leading to:
- 15-20% material waste from human measurement errors
- 42% longer production cycles compared to automated systems
- Inconsistent welding quality causing 12% field failures
Parameter | Manual Assembly | Automatic Assembly |
---|---|---|
Daily Output | 120-150 units | 800-1,200 units |
Tolerance Precision | ±2.5mm | ±0.3mm |
How Modern Assembly Systems Solve Production Bottlenecks
Leading manufacturers like Anhui Youli have deployed 51 specialized assembly machines in their new production lines, achieving:
- 40% reduction in labor costs
- 0.05mm repeat positioning accuracy
- Modular design allowing 15-minute product changeovers
"The integration of vision-guided robotics has been a game-changer. Our defect rate plummeted from 8.2% to 0.7% within six months of implementation." – Production Manager, Tier 1 PV Manufacturer
3 Critical Components Redefining Automated Assembly
- AI-Powered Quality Control Modules
Using deep learning algorithms to detect micro-cracks invisible to human inspectors - Self-Adjusting Fixture Systems
Automatically compensates for material thermal expansion during welding - Collaborative Robotics (Cobots)
Enables safe human-machine interaction in final assembly stages
Real-World Impact: Case Study Analysis
A recent deployment in Jiangsu Province demonstrates:
- 83% faster ROI compared to conventional automation systems
- 56% energy savings through smart power management
- ISO 14644-1 Class 7 cleanroom compatibility
Well, you might wonder – does this technology justify the upfront investment? Consider this: Automated lines typically achieve break-even within 18 months through yield improvements alone. The latest systems even incorporate blockchain-enabled component tracking, adding supply chain transparency that's becoming crucial for ESG compliance.
Future-Proofing Your Production Lines
With the U.S. Department of Energy forecasting 70% solar cost reductions by 2030, forward-looking manufacturers are prioritizing:
- 5G-enabled machine communication for real-time adjustments
- Hydrogen-resistant coatings for coastal installations
- Multi-material compatibility (aluminum/carbon fiber composites)
As we approach Q4 2025, the industry's moving toward closed-loop manufacturing ecosystems where assembly equipment automatically orders replacement parts and optimizes maintenance schedules. Isn't it time your operation stopped playing catch-up?
Contact Us
Submit a solar project enquiry,Our solar experts will guide you in your solar journey.