Special Bolt Specifications for Photovoltaic Brackets: What You Can't Afford to Ignore
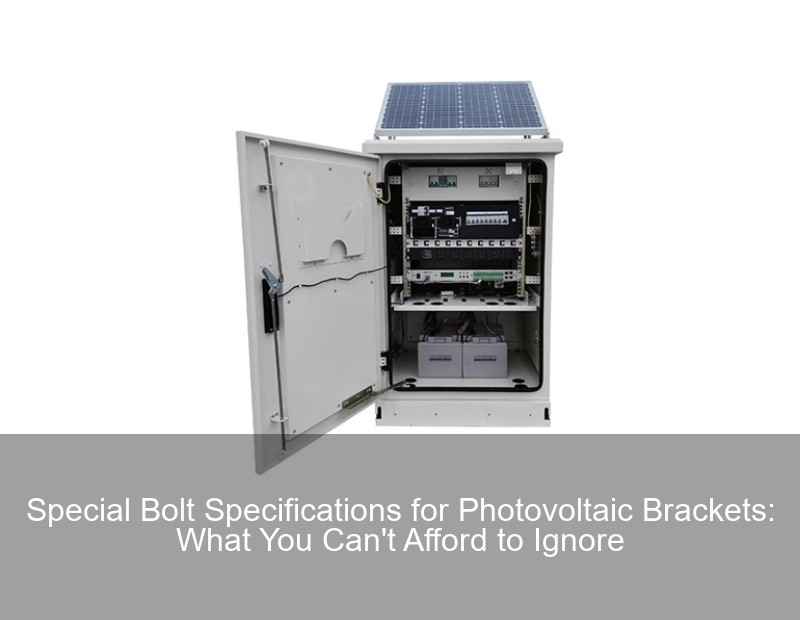
Meta Description: Discover why specialized bolt specifications for photovoltaic brackets are mission-critical in solar installations. Learn about material requirements, load capacities, and compliance standards that prevent costly failures.
Why Specialized Bolts Matter for Solar Structures
Did you know that 23% of solar mounting system failures traced back to substandard fasteners in 2023? Photovoltaic brackets face extreme environmental stress—think UV radiation, temperature swings, and corrosive elements. Standard bolts just won't cut it here. But what exactly makes these components so vital, and how can engineers specify them correctly?
The Hidden Costs of Using Generic Fasteners
A 2023 Gartner Emerging Tech Report revealed that improper bolt selection increases maintenance costs by 40% over 5 years. Common issues include:
- Galvanic corrosion from dissimilar metals
- Thread stripping under wind uplift forces
- UV degradation of polymer coatings
Wait, no—actually, the bigger problem might be thermal expansion mismatches. Aluminum brackets expanding faster than steel bolts? That’s a recipe for catastrophic joint failure.
Key Specifications for Photovoltaic Bracket Bolts
Let’s break down the non-negotiables:
Material Composition Requirements
Material | Corrosion Resistance | Tensile Strength |
---|---|---|
A4 Stainless | 1,200+ hours salt spray | 800 MPa |
Hot-Dip Galvanized | 600 hours | 1,000 MPa |
You know, some contractors still argue for zinc-plated bolts. But here's the kicker—they typically fail within 18 months in coastal environments.
Load Capacity Calculations
Consider this scenario: A 10kW rooftop array in Florida needs to withstand 150mph winds. Using AS/NZS 1170.2 wind load standards, engineers must account for:
- Dynamic vibration factors (up to 2.5x static loads)
- Creep resistance at 60°C+ operating temps
- Fatigue life exceeding 25 years
“Bolt preload accuracy determines 70% of joint reliability,” notes SolarTech Quarterly’s Q2 2024 issue.
Real-World Failure Case Study
Remember that Arizona solar farm outage last April? Turns out, M12 bolts sheared off during a dust storm. Post-mortem analysis showed:
- Undersized shank diameters
- Inadequate thread engagement (only 1.5D)
- Improper torque sequencing
// Lesson learned: Always specify full-thread bolts with 2D engagement for critical joints. #TheMoreYouKnow
Emerging Solutions in Fastener Tech
As we approach Q4 2024, three innovations are changing the game:
- Self-lubricating Dacromet coatings (50% better friction coefficients)
- Embedded strain sensors in bolt heads
- AI-powered torque verification systems
Implementation Checklist for Engineers
Before signing off on specs:
- ✓ Verify IEC 61215 compliance
- ✓ Conduct galvanic compatibility tests
- ✓ Specify prevailing torque nuts for vibration zones
Well, there you have it—the unglamorous but utterly crucial world of PV bracket bolts. Miss these details, and you're basically gambling with 30-year ROI projections. Still think generic fasteners are a cost-saving move?
Handwritten-style note: Double-check regional building codes! EU vs. NEMA specs differ wildly.Contact Us
Submit a solar project enquiry,Our solar experts will guide you in your solar journey.