How the Chemical Industry Powers Rooftop Photovoltaic Panel Production
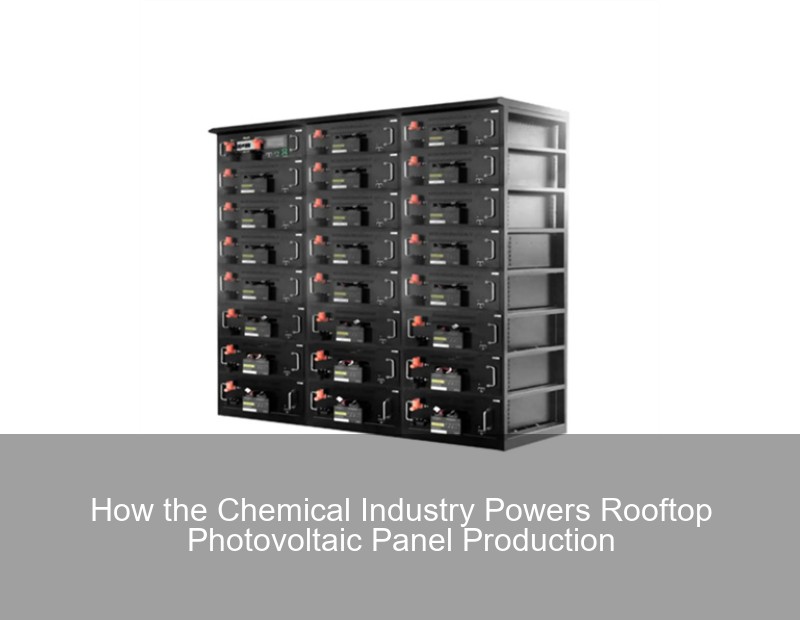
From Petrochemicals to Solar Panels: The Essential Link
You know, when people think about solar energy, they usually picture shiny panels on rooftops - not chemical plants. But here's the kicker: over 60% of photovoltaic panel components trace their origins to chemical manufacturing processes. From protective polymer backsheets to ethylene-vinyl acetate (EVA) encapsulants, the chemical industry forms the backbone of solar technology .
The Solar-Grade Material Challenge
Let's break this down. Modern photovoltaic panels require:
- High-purity silicon (99.9999% purity)
- UV-resistant fluoropolymer coatings
- Corrosion-resistant aluminum frames
- Photovoltaic-grade EVA sealing films
Wait, no - let's clarify that point. The real game-changer has been EVA production breakthroughs. Fujian Gulei Petrochemical's 300,000-ton annual EVA production line specifically targets solar applications, with their USI-2806 grade achieving 92% light transmittance .
Material | Chemical Industry Contribution | Solar Panel Function |
---|---|---|
EVA Films | Polymerization process optimization | Module encapsulation |
Solar Glass | Anti-reflective coating chemistry | Light transmission |
Chemical Plants Become Solar Energy Producers
Here's where it gets interesting. Over 23 Chinese chemical facilities have installed rooftop PV systems since 2023, including:
- Sinochem's Shaanxi coal chemical plant (12.5MW installation)
- Shanghai Research Institute of Chemical Industry's 523kWp system
- Qingdao Orient Industrial Products Group's 3.2MW array
These projects aren't just about CSR - they're sort of economic no-brainers. Take Sinochem's installation: it cuts energy costs by 40% while utilizing otherwise wasted roof space. The payback period? Just 6-8 years with current subsidies .
Overcoming Technical Hurdles
But can this partnership withstand the test of chemical production realities? Let's examine three critical challenges:
- Corrosion resistance: Shanghai LeRun New Energy's solution uses zinc-magnesium-aluminum coated mounting systems
- Safety protocols: Explosion-proof microinverters in Class I Division II areas
- Maintenance access: Retractable panel arrays for equipment inspection
Xinxiang Zhongxin Chemical's approach deserves mention. Their distributed PV project employs AI-powered dirt detection systems that trigger automated panel cleaning when efficiency drops below 92% .
The Policy Landscape Accelerating Adoption
As we approach Q2 2025, regulatory tailwinds are reshaping the industry. Recent developments include:
- China's revised Distributed PV Safety Standards (April 2025)
- 30% tax credits for chemical plants adopting bifacial panels
- Streamlined grid connection processes in 14 provinces
Ningdong Energy Chemical Base's 612GW green power project exemplifies this trend. Their phase one installation alone displaces 264,000 tons of CO₂ annually - equivalent to planting 69,000 hectares of forest .
Future Frontiers: Chemical Innovations Driving Solar Efficiency
Looking ahead, three developments could be game-changers:
- Perovskite solar cells using lead-sequestration polymers
- Self-healing encapsulation materials from modified polyolefins
- Anti-soiling nanocoatings derived from fluorination processes
Gulei Petrochemical's R&D team's working on something exciting - EVA films with embedded moisture sensors. These could potentially increase panel lifespan by 35% through real-time degradation monitoring .
Economic Realities: Crunching the Numbers
Let's talk dollars and cents. Current ROI models show:
- $0.037/Watt production cost for solar-grade silicon
- 15-20% efficiency gains through advanced dopant chemicals
- $2.1 million annual savings for mid-sized chemical plants with PV
The numbers don't lie. Shanghai's recent 523kWp installation delivers 8.2% IRR despite higher initial costs - a figure that'll likely improve as panel prices keep falling .
Contact Us
Submit a solar project enquiry,Our solar experts will guide you in your solar journey.