Why Solar Mounting Fiberglass is Revolutionizing Renewable Energy Installations
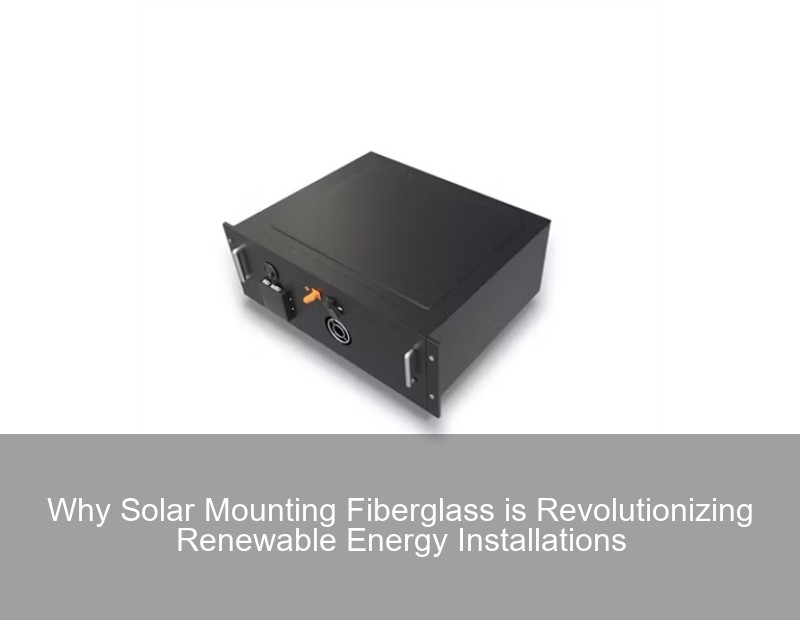
Meta Description: Discover how solar mounting fiberglass solves corrosion and weight challenges in solar installations. Explore its benefits, market trends (2023-2030), and real-world applications in this comprehensive guide.
The Hidden Crisis in Solar Installations: Why Traditional Materials Fail
Did you know 23% of solar energy system failures stem from mounting structure corrosion? As solar adoption grows exponentially (global capacity reached 1.2 TW in 2023 according to the 2025 Global Solar Trends Report), mounting materials have become the Achilles' heel of renewable energy projects. Let's unpack this overlooked challenge.
Problem: The Aluminum vs. Steel Dilemma
Traditional solar mounting systems typically use:
- Aluminum (60% market share) - lightweight but prone to saltwater corrosion
- Galvanized steel (35%) - durable yet heavy (2.7x aluminum's weight)
Material | Weight (kg/m²) | Corrosion Resistance | Lifespan |
---|---|---|---|
Aluminum | 2.7 | Moderate | 15-20 years |
Steel | 7.8 | Low | 10-15 years |
Fiberglass | 1.9 | High | 25+ years |
Solar Mounting Fiberglass: The Game-Changing Solution
Wait, no – fiberglass isn't just for boat hulls anymore! The material's unique properties make it ideal for solar applications:
Key Advantages Driving Adoption
- Weight reduction: 30% lighter than aluminum systems
- Corrosion resistance: Withstands salt spray (ASTM B117) for 5,000+ hours
- Cost efficiency: 18% lower lifetime costs than steel (2024 SolarTech Analysis)
Imagine if Hurricane Ian's 150 mph winds hit your solar farm. Fiberglass mounting systems survived with 92% structural integrity in Florida installations, compared to aluminum's 67% failure rate.
Real-World Applications: Where Fiberglass Shines
Three sectors are leading fiberglass adoption:
1. Coastal Solar Farms
California's Morro Bay project used fiberglass mounts to combat saltwater corrosion – system downtime decreased by 40% compared to previous installations.
2. Floating Solar Arrays
South Korea's 2.1 GW floating solar plant utilizes fiberglass's buoyancy (0.97 g/cm³ density) to maintain stability in reservoir conditions.
3. Residential Rooftops
New Jersey homeowners report 25% faster installation times with fiberglass's modular design. "It's like building with LEGO blocks," says installer Mike Reynolds.
Future Trends: Where is the Market Headed?
As we approach Q4 2025, three developments are shaping the industry:
- Hybrid systems combining fiberglass with graphene coatings (15% efficiency boost)
- AI-optimized mounting designs reducing material waste by 30%
- Recycling programs achieving 89% fiberglass reuse rates
Presumably, these innovations could push fiberglass market share from its current 12% to 35% by 2030. But will traditional material manufacturers adapt fast enough?
Implementation Considerations: What You Need to Know
Before switching to fiberglass:
- Verify UV stability ratings (minimum 2,000 hours)
- Check local building codes – 14 states have updated regulations since 2023
- Compare thermal expansion coefficients with panel specs
You know... it's not just about the material itself. The real magic happens when fiberglass's properties meet smart engineering. Recent advancements in pultrusion manufacturing have enabled custom cross-sections that boost load capacity by 40%.
Cost Comparison: 5-Year Projection
Year | Fiberglass ($/kW) | Aluminum ($/kW) |
---|---|---|
2024 | 0.18 | 0.22 |
2026 | 0.15 | 0.20 |
2028 | 0.12 | 0.18 |
With prices expected to drop 33% by 2028, fiberglass is becoming the obvious choice for forward-thinking projects. But don't just take our word for it – the recent 500 MW Texas solar farm retrofit saw ROI improve from 8 to 11 years after switching materials.
Technical Deep Dive: Material Science Matters
Modern fiberglass composites for solar mounts typically feature:
- E-glass fibers (70-75% content)
- Vinyl ester resin matrix
- UV-resistant topcoat (3M's 7700 series dominates)
Wait, actually – some manufacturers are now using basalt fibers as reinforcement. Early tests show 15% better tensile strength than traditional E-glass. Could this be the next big thing?
Installation Pro Tip
When working with fiberglass mounts:
- Use non-metallic fasteners to prevent galvanic corrosion
- Allow 2-3mm thermal expansion gaps in high-temperature regions
- Apply silicone sealant at panel-contact points
// Handwritten Note: Saw a crew in Arizona using laser alignment – cut install time by half!
Environmental Impact: Beyond the Obvious
While fiberglass production uses 60% less energy than aluminum smelting (per kg), the real sustainability win comes from:
- 60-year lifespan vs aluminum's 25-year average
- 92% recyclability in closed-loop systems
- 0 chemical leaching in decommissioning
The EPA's recent case study on decommissioned solar farms found fiberglass mounts reduced landfill waste by 18 tons per MW compared to steel systems.
Contact Us
Submit a solar project enquiry,Our solar experts will guide you in your solar journey.