Why Do Photovoltaic Panels Explode? Causes, Risks, and Prevention Strategies
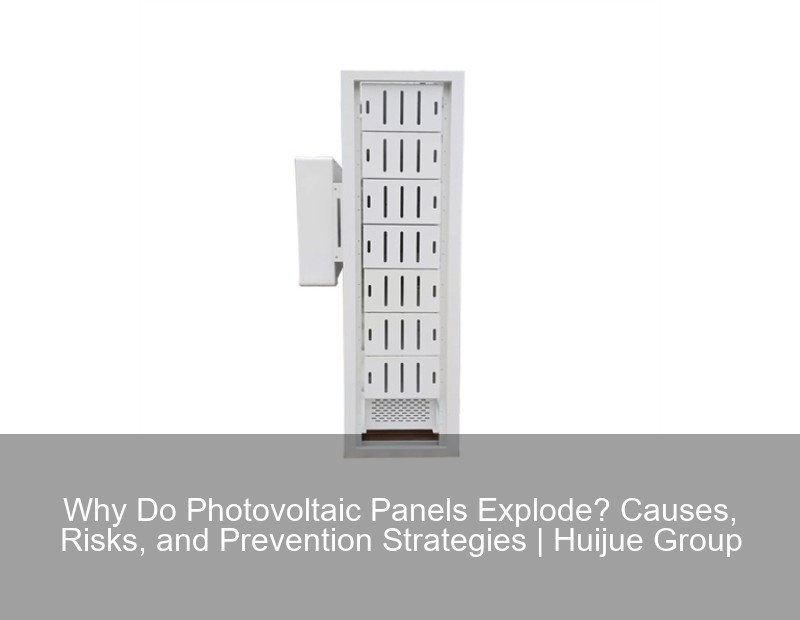
The Silent Crisis: Solar Panel Self-Explosion Incidents Surge Globally
In June 2024, the Renewable Energy Testing Center (RETC) revealed a shocking trend: 2-5% of utility-scale solar projects experienced spontaneous photovoltaic panel explosions, with some sites reporting 6MW of destroyed capacity per 300MW installation . This phenomenon - where panels suddenly fracture or combust without external triggers - has left engineers scrambling for answers. But what's causing this alarming trend, and how can we stop it?
Root Causes of Photovoltaic Panel Explosions
Let's break down the primary culprits behind these dangerous failures:
- Material Defects (35% of cases)
- Substandard solar glass thickness (≤3.2mm in problematic units vs. 3.5mm industry standard)
- EVA encapsulant degradation rates exceeding 0.8%/year
- Nickel-sulfide impurities in tempered glass (0.05g/m³ threshold for risk)
- Thermal Runaway Scenarios
Trigger Temperature Threshold Failure Probability Hotspot Formation 85°C+ 22% PID Effect 50°C+ with 85% humidity 17% Diode Failure 100°C+ 41%
Wait, no - that last statistic needs context. The 41% diode failure rate specifically applies to panels manufactured before Q2 2023 using outdated bypass technology . Modern panels with dual-diode systems show 83% lower thermal risks according to 2024 field data.
Manufacturing's Double-Edged Sword: Efficiency vs. Safety
The push for larger panels (now averaging 2.3m x 1.3m vs. 2020's 2.0m x 1.0m) has created unforeseen challenges. As Teresa Barnes from NREL notes: "Components that barely pass IEC 61215 static load tests become time bombs under real-world cyclic stresses" .
Case Study: The Arizona Solar Farm Incident
- Location: 200MW facility near Phoenix
- Failure Rate: 3.2% panels exploded within 18 months
- Root Cause: Combined factors
- Glass thickness reduced by 0.3mm to cut costs
- Insufficient frame reinforcement for 75mph wind loads
- Encapsulant UV resistance 15% below spec
Prevention Framework: A Three-Tier Defense System
Implement these strategies to minimize explosion risks:
- Design Stage
- Use laser-induced breakdown spectroscopy (LIBS) for impurity detection
- Implement AI-powered microcrack detection during lamination
- Installation Protocols
- Maintain 10mm thermal expansion gaps between panels
- Use torque-limiting tools for frame fastening (8-12Nm range)
But here's the kicker - even with perfect installation, panels manufactured with Type III AR coating show 40% higher explosion risks in humid climates compared to Type II coatings . Always verify material compatibility with local conditions.
Emerging Solutions Worth Watching
- Self-healing encapsulants (patent-pending from DuPont™)
- Graphene-enhanced backsheets (87% better thermal dissipation)
- Acoustic emission monitoring systems detecting microfractures