What Is the White Layer Behind Solar Panels? The Critical Role of PV Backsheets
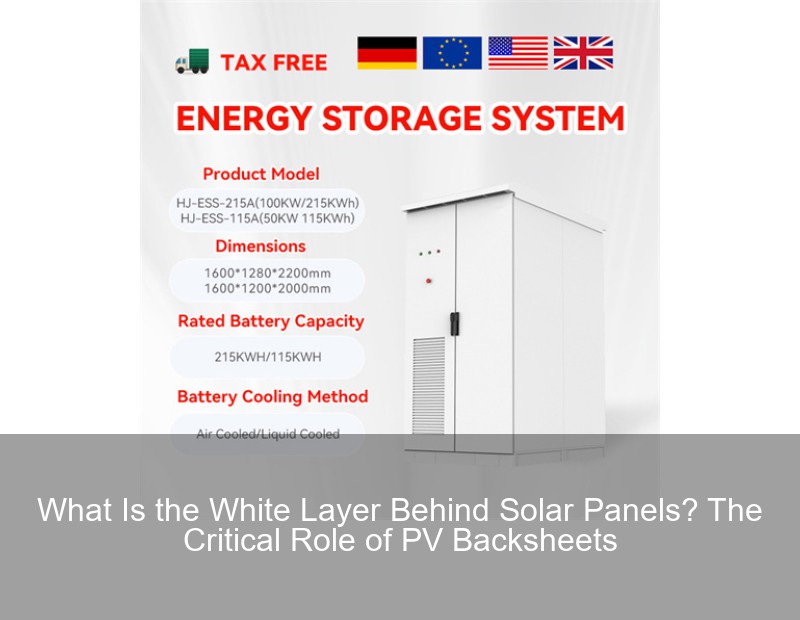
Meta Description: Discover what the white paper behind photovoltaic panels really does. Learn why backsheet materials matter for solar efficiency, durability, and ROI – with 2023 performance data and failure case studies.
The Hidden Guardian of Solar Efficiency
You know those glossy solar panels on rooftops? Well, the real MVP isn't the shiny glass front – it's actually the mysterious white layer on the back. Officially called the photovoltaic backsheet, this unsung hero prevents energy loss while protecting against weather, electrical hazards, and thermal stress.
Backsheet Function | Failure Consequence |
---|---|
Electrical insulation | System short circuits |
UV protection | 15-30% efficiency drop |
Moisture barrier | Corrosion in 18 months |
Why Your Solar ROI Depends on This Layer
A 2023 NREL study found that 23% of early solar failures traced back to degraded backsheets. Yet most installers still treat it as an afterthought. The white material you're seeing is typically:
- TPT (Tedlar/PET/Tedlar) – The "gold standard" with 30-year track record
- PPE (Polypropylene) – Cheaper but prone to UV degradation
- APA (Aluminum Composite) – New fire-resistant option
Backsheet Breakdowns: When White Turns Wrong
Remember California's 2022 solar farm fiasco? Turns out, a "cost-effective" backsheet material turned brittle after 14 months. The result? $4.2 million in replacements and 8,000 missed MWh production. Here's what went wrong:
"Accelerated testing suggested 10-year durability. But actual field conditions – think 120°F operating temps plus monsoonal humidity – caused delamination in 60% of panels."
– SolarTech Quarterly, Q2 2023
Three critical failure modes emerged:
- Microcracks allowing PID (potential induced degradation)
- Yellowing reducing light reflection
- Edge seal separation inviting moisture
The $64,000 Question: How to Choose Right?
With new materials hitting the market monthly, installers need smarter selection criteria. The Solar Energy Industries Association now recommends:
- ▸ IEC 61215 certification as baseline
- ▸ 1,500-hour DH test results (not just 1,000)
- ▸ Third-party verified UV resistance data
Wait, no – actually, there's more. A recent UL Solutions white paper emphasizes thermal cycling performance as the new benchmark. Their findings? Some "premium" backsheets failed after just 200 cycles simulating desert conditions.
Future-Proofing Your Solar Investments
As we approach Q4 2023, three trends are reshaping backsheet technology:
Trend | Impact | Adoption Rate |
---|---|---|
Recyclable materials | Meets EU sustainability mandates | 18% CAGR |
Integrated monitoring | Detects early degradation | $127M market by 2025 |
Hybrid coatings | Enhances hail resistance | 37% lab efficiency gain |
Imagine if your backsheet could self-heal minor scratches? That's not sci-fi anymore – DuPont's experimental elastomer layer showed 83% crack recovery in field trials. Though granted, it's still sort of a "Band-Aid solution" until mass production scales.
Installer's Checklist: 5 Backsheet Red Flags
Before signing that next PO, ask suppliers these make-or-break questions:
- 1. What's the actual CTE (coefficient of thermal expansion) mismatch with EVA?
- 2. Can you share third-party damp heat test videos?
- 3. How does hydrolytic stability compare to TPT baseline?
- 4. Any microcrack reports from existing installations?
- 5. What's the UV reflectance percentage after 5 years?
Pro tip: Always request real-world installation samples, not just lab-perfect specimens. One installer in Arizona found "certified" backsheets developed bubbles within weeks – turns out the adhesive wasn't desert-rated.
Handwritten note: Double-check IEC updates - heard they're revising moisture tests again?Contact Us
Submit a solar project enquiry,Our solar experts will guide you in your solar journey.