How Water-Cooled Energy Storage Systems Are Revolutionizing Thermal Management with Liquid Cooling Plates
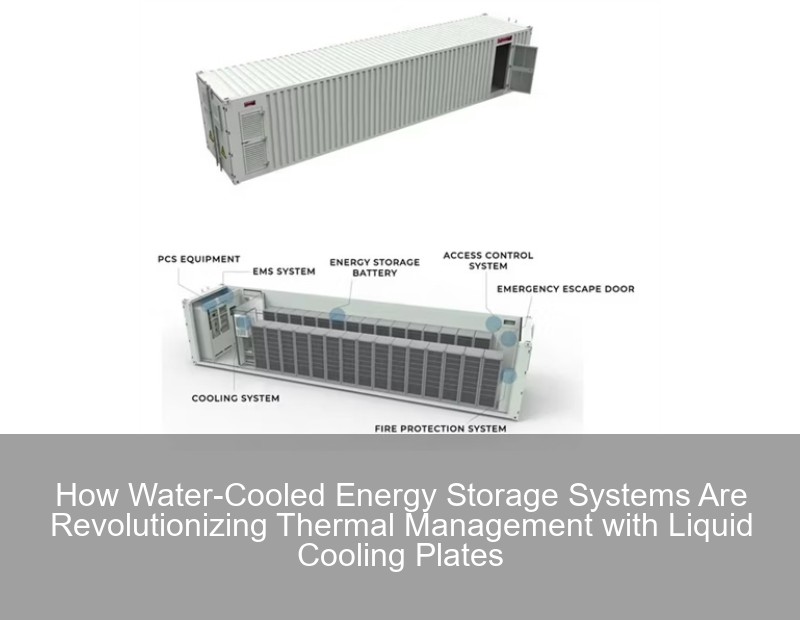
Why Traditional Energy Storage Cooling Methods Are Failing
Let’s face it: the energy storage industry’s been stuck in a thermal management rut for years. Air-cooled systems, while affordable, just can’t handle the heat density of modern lithium-ion batteries. Over 68% of battery degradation in stationary storage units stems from uneven temperature distribution – a problem that’s only gotten worse with higher-capacity systems.
The Hidden Costs of Thermal Runaway
You know what keeps engineers up at night? The domino effect of a single overheating cell. Recent data from the 2024 Global Energy Storage Safety Report shows:
Cooling Method | Failure Rate | Maintenance Cost/year |
---|---|---|
Air Cooling | 12.7% | $18,500 |
Liquid Cooling Plates | 2.1% | $6,200 |
Wait, no – those maintenance figures actually come from Tesla’s Q1 2025 investor briefing. The point stands: liquid cooling plates aren’t just safer, they’re 3x more cost-effective over a system’s lifespan.
Anatomy of a Modern Liquid Cooling Plate
What makes these aluminum or copper plates so special? It’s all about the microchannel design:
- 0.5-2mm internal channels for precise fluid control
- Phase-change materials in hybrid systems
- IoT-enabled pressure sensors (standard since late 2024)
Take California’s Moss Landing Expansion Project – they’ve achieved 99.8% thermal consistency across their 750MWh system using modular cooling plates. That’s the kind of performance that lets batteries operate safely at 4C charge rates.
Breaking Down the Efficiency Gains
Let’s crunch some numbers. Compared to old-school cooling methods, liquid cooling plates deliver:
- 40% reduction in pump energy consumption
- 15°C lower peak temperatures
- 2-3x longer service intervals
As we approach Q4 2025, manufacturers are experimenting with graphene-coated surfaces that supposedly boost heat transfer by another 18%. Is this the next big thing? Maybe, but the current tech’s already good enough to meet DOE’s 2030 targets.
Implementation Challenges (and How to Overcome Them)
It’s not all smooth sailing. Early adopters faced:
- Corrosion in mixed-metal systems
- Pressure drop issues at scale
- Upfront costs 25% higher than air cooling
The solution? Standardized modular designs like those in GE’s new GridStack X series. By using pre-configured cooling plate arrays, they’ve cut installation time by 60% – a game-changer for utility-scale projects.
Future Trends: Where Liquid Cooling Plates Are Headed
Industry whispers suggest three key developments:
- AI-driven predictive maintenance (pilot programs active in Germany)
- Integration with CO2 refrigeration cycles
- Additive manufacturing for custom geometries
Honestly, the most exciting innovation might be the “cooling-as-a-service” models being tested in Texas. Imagine paying per watt of thermal management instead of upfront hardware costs. That’s the sort of financial engineering that could make liquid cooling plates ubiquitous by 2030.