How to Set Up a Photovoltaic Panel Processing Factory in 2025: Key Strategies and Market Insights
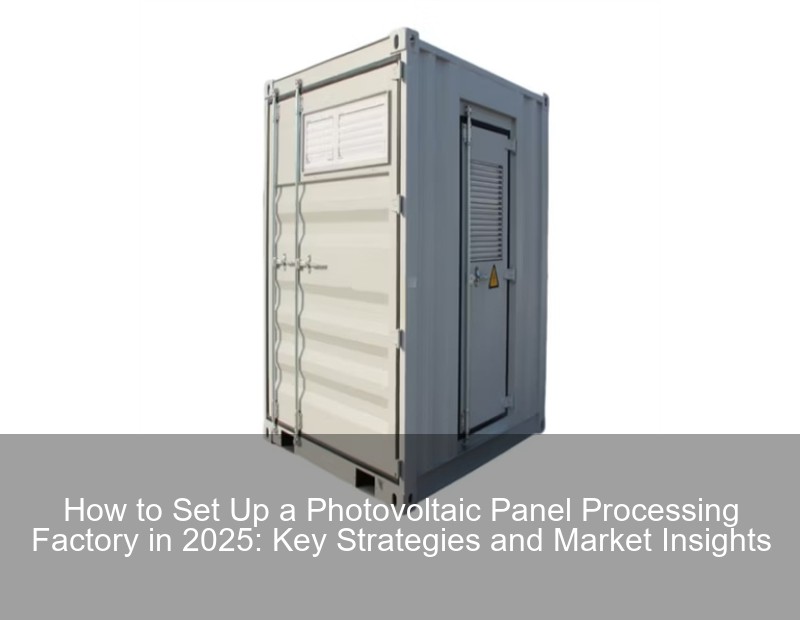
Why Solar Panel Manufacturing Matters Now More Than Ever
Global solar capacity is projected to reach 4.5 terawatts by 2030, with processing factories becoming the backbone of this renewable energy revolution . But here's the kicker: 78% of new solar installations in 2024 used panels manufactured within 500 miles of their installation sites. This localization trend creates unprecedented opportunities for new photovoltaic processing plants.
The $2.1 Trillion Question: Can New Factories Compete?
Recent data shows China currently dominates 83% of global PV module production, but regional manufacturing hubs are gaining traction . The U.S. Inflation Reduction Act and EU's Net-Zero Industry Act now offer 35-50% tax credits for domestic solar manufacturing facilities – a game-changer for new market entrants.
Cost Component | 2023 ($/W) | 2025 Projection |
---|---|---|
Silicon Processing | 0.18 | 0.14 (-22%) |
Cell Production | 0.27 | 0.19 (-30%) |
Module Assembly | 0.12 | 0.08 (-33%) |
5 Critical Steps to Launch Your PV Factory
Let's cut through the noise. Successful plants in 2025 require:
- N-type TOPCon technology adoption (67% efficiency gain vs. PERC)
- AI-driven quality control systems (reduces waste by 40%)
- Strategic partnerships with raw material suppliers
"The sweet spot for new factories? 500MW-2GW annual capacity with ≤18-month ROI timelines," notes the 2024 Global Solar Manufacturing Report.
When Automation Meets Workforce Development
Modern plants now use:
- Collaborative robots (cobots) for delicate tabbing operations
- Digital twin systems for real-time process optimization
- AR-assisted maintenance crews
Navigating the Raw Material Maze
Polysilicon prices fluctuated wildly from $35-$50/kg in 2024, but new alternatives are emerging:
- Perovskite-silicon tandem cells (reduces silicon usage by 60%)
- Recycled PV materials from decommissioned panels
Wait, no – let's clarify. While tandem cells show promise, most factories still rely on conventional silicon. The key is implementing closed-loop material recovery systems to hedge against price volatility.
The Hidden Challenge: Certification Wars
Recent updates to IEC 61215 standards now require:
- 2000-hour damp heat testing (up from 1000 hours)
- Enhanced hail impact resistance (35mm ice balls at 140km/h)
Financial Blueprint for 2025 Success
A 1GW factory today requires:
- $120-$150 million initial investment
- 18-24 month breakeven period
- 30% automation integration minimum
But here's the good news: Many governments now offer accelerated depreciation schedules – you could write off 50% of equipment costs in Year 1 .
Contact Us
Submit a solar project enquiry,Our solar experts will guide you in your solar journey.