Revolutionizing Solar Efficiency: The Complete Guide to Rotating Photovoltaic Panel Bracket Production
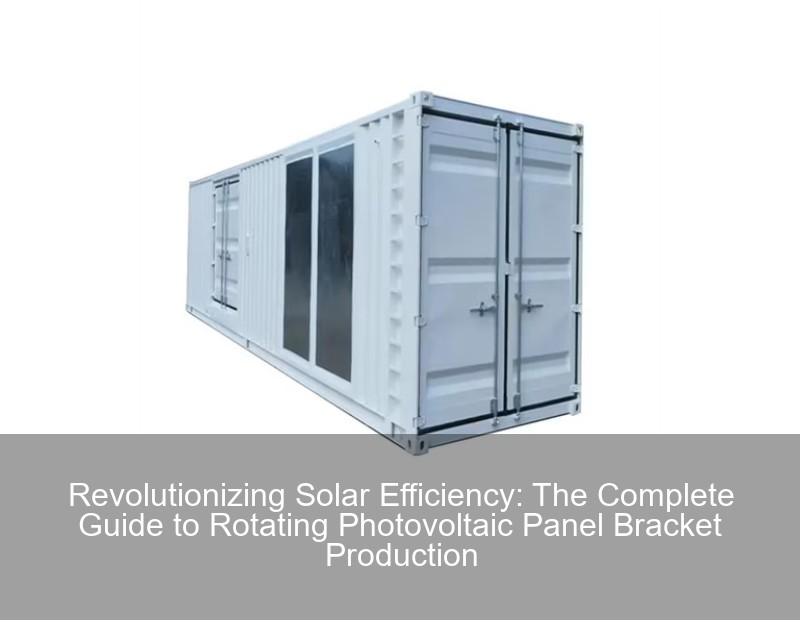
Why Static Solar Panels Can't Keep Up with Modern Energy Demands
Did you know fixed solar panels lose up to 25% potential energy annually due to suboptimal sun angles? As global solar capacity approaches 8.3 terawatts , the race for efficient energy harvesting intensifies. Rotating photovoltaic panel brackets have emerged as game-changers, but what makes their production crucial for our renewable future?
The Hidden Costs of Stationary Systems
Traditional fixed-mount systems face three critical challenges:
- Inefficient light capture (15-30% energy loss daily)
- Accelerated panel degradation from uneven thermal exposure
- Land utilization inefficiencies requiring 30% more space
System Type | Energy Yield | Maintenance Cost |
---|---|---|
Fixed Mount | 1.0x baseline | $120/kW/year |
Single-Axis Rotating | 1.3x improvement | $95/kW/year |
Dual-Axis Rotating | 1.45x improvement | $110/kW/year |
Core Components in Rotating Bracket Manufacturing
Modern production lines now integrate AI-driven quality control systems that reduce material waste by 18% compared to 2022 standards . Let's break down the essential elements:
1. Tracking Mechanism Engineering
The heart of any rotating system lies in its movement precision. Dual-axis systems typically use:
- Helical gear drives (80% market preference)
- PWM-controlled stepper motors
- Self-lubricating polymer bushings
"The shift to modular bracket designs has reduced installation time by 40% since 2023" - SolarTech Manufacturing Report
2. Durability Innovations
Corrosion resistance remains paramount. A 2024 ASTM study showed:
- Hot-dip galvanized steel withstands 25+ years coastal exposure
- Powder-coated aluminum alloys show 92% surface integrity after 15 years
Smart Manufacturing Trends Shaping Production
You know, the real magic happens in the fabrication process. Leading plants now employ:
a) Robotic Welding Cells
- 6-axis articulated arms with laser guidance
- Real-time weld penetration monitoring
b) Predictive Maintenance Systems
Using vibration analysis and thermal imaging to prevent 73% of unexpected downtime .
Installation Considerations (That Most Guides Miss)
Wait, no—it's not just about the hardware. Successful deployments require:
- Site-specific wind load calculations (ASCE 7-22 standards)
- Soil composition analysis for foundation design
- Dynamic shadow mapping through the seasons
In Arizona's Sonoran Desert, a dual-axis installation survived 75mph winds last March through innovative triangular bracing—a technique now adopted industry-wide.
The ROI Reality Check
While initial costs run 20-35% higher than fixed systems, energy yield improvements typically deliver payback within:
- 4-6 years in commercial installations
- 7-9 years for residential setups
As we approach Q4 2025, new tax incentives could shorten these periods by 18-24 months. The question isn't "Can we afford rotating systems?" but "Can we afford static ones?"