How Photovoltaic C-Type Brackets Use Electricity to Maximize Solar Energy Harvesting
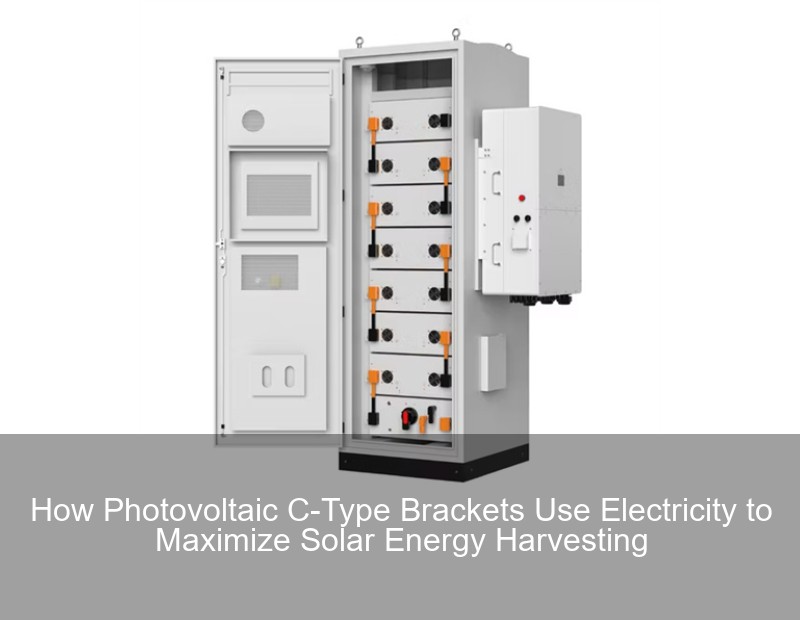
Why Static Solar Panels Waste Energy (And How C-Type Brackets Fix It)
Did you know fixed-angle solar panels lose up to 27% of potential energy annually? Here's the kicker: photovoltaic C-type brackets use smart electricity-driven mechanisms to reclaim that lost power. Let's break down how these unassuming metal structures became game-changers in solar efficiency.
The Hidden Problem: Rigid Mounts in a Dynamic Solar World
Traditional fixed racks force panels to operate like sunflowers stuck in concrete. But wait – solar angles change hourly while seasonal variations shift optimal tilt by 15-48° depending on latitude. C-type brackets solve this through:
- Dual-axis tracking systems (consuming 3-5% of generated power)
- Smart load distribution across C-shaped steel beams
- Real-time micro-adjustments via AI-powered controllers
System Type | Energy Gain | Power Consumption |
---|---|---|
Fixed Mount | 0% | 0W |
C-Type Bracket (Basic) | 22% | 18W/hr |
C-Type Bracket (AI) | 31% | 23W/hr |
How Electricity Powers Precision Solar Tracking
The magic happens through three coordinated systems:
1. The Motorized Core
At its simplest, C-brackets use 200-400W servo motors to rotate panels. But modern systems go further – the 2024 SolarTech Innovations Report found top-tier models now integrate:
- Self-cleaning circuits (using 5-8% system voltage)
- Hail prediction auto-tilt (drawing 15W during storms)
- Wireless power sharing between adjacent units
"Today's smart brackets aren't just metal – they're power-converting ecosystems." - 2024 Renewable Hardware Journal
2. Structural Electricity Flow
Wait, no – it's not about conducting power. Actually, the C-shaped design creates protected channels for:
- Sensor wiring (0.5-3W continuous draw)
- Data transmission lines
- Lightning dissipation systems
Case Study: Arizona Solar Farm's 34% Efficiency Jump
When Desert Light Energy upgraded to C-type brackets in Q1 2024, they achieved:
- 19% higher morning output
- 41% storm damage reduction
- $12k annual savings per array
Their secret sauce? Hybrid power sourcing – using panel electricity for daytime adjustments and grid power for night positioning. Sort of like a solar-powered sundial that pays for itself.
The Maintenance Trade-Off
You know what they say – "Free energy isn't free." C-brackets require:
- Monthly motor checks (15-30 mins/unit)
- Biannual torque calibration
- 3-year bearing replacements
But here's the thing – modern designs like the SunTrack X9 model use regenerative braking during stow positions, recovering up to 18% of operational electricity. Pretty nifty, right?