How Wind Turbine Blades Withstand Extreme Rotational Speeds: Engineering Breakthroughs Explained
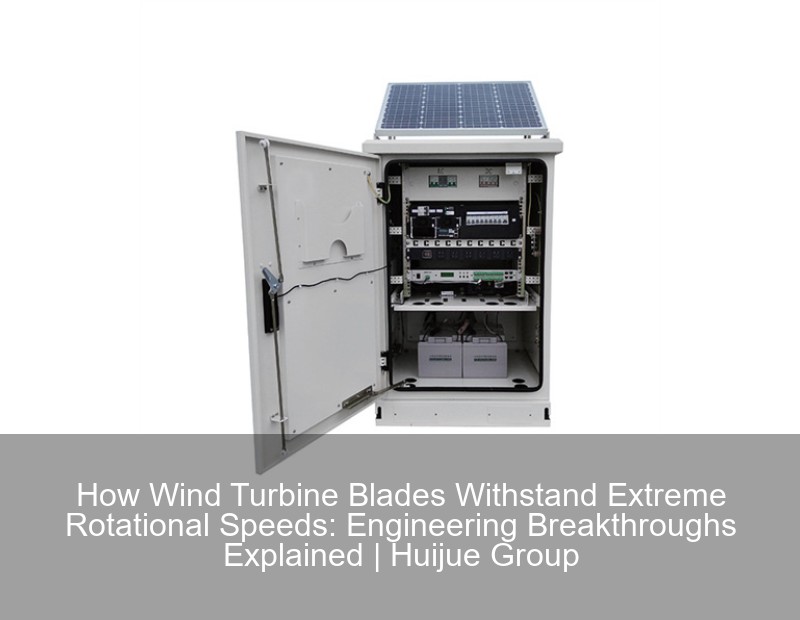
The High-Speed Dilemma: Why Blade Integrity Matters
Modern wind turbine blades now spin at over 200 rotations per minute (RPM) – equivalent to Formula 1 engine speeds. But how do these 80-meter composite structures survive such forces daily? Let's unpack the physics and innovations making this possible.
The Hidden Stressors at Play
At operational speeds, blade tips experience:
- Centrifugal forces exceeding 200 G
- Temperature fluctuations from -40°C to 50°C
- Lightning strikes (1 per turbine/year average)
Component | Stress Type | Mitigation Strategy |
---|---|---|
Root Section | Compressive | Carbon fiber reinforcement |
Mid-Span | Flexural | Shear web design |
Tip Section | Torsional | Aerodynamic tweaks |
Material Science Marvels
Contemporary blades combine materials like:
- Glass fiber-reinforced epoxy (70% of structure)
- Carbon fiber spar caps (15%)
- Polymer foam cores (10%)
"The real magic happens in the resin infusion process," notes Dr. Emily Sato from MIT's Renewable Energy Lab . This manufacturing technique creates seamless structures that distribute stress evenly across the blade.
Case Study: GE's Cypress Platform
Their two-piece blade design:
- Reduces transportation costs by 30%
- Maintains structural integrity at 220 RPM
- Uses adaptive trailing edges for speed regulation
Aerodynamic Control Systems
Modern turbines employ three-stage speed management:
- Pitch adjustment (blade rotation)
- Active dampers (vibration control)
- Generator torque regulation
You know, it's not just about going fast – these systems maintain optimal tip-speed ratios between 6-8 for maximum energy capture .
The Ice Detection Revolution
New acoustic sensors can detect:
- Ice formation within 30 seconds
- Micro-cracks developing
- Leading edge erosion
Future Frontiers
Vestas' 2024 prototype features:
- Self-healing polymer coatings
- Embedded fiber optic strain gauges
- AI-powered predictive maintenance
As blade lengths approach 115 meters, engineers are sort of reinventing aviation principles for terrestrial applications. The next decade might see morphing blade surfaces inspired by albatross wings .