Daqiuzhuang Photovoltaic Bracket Round Tube Manufacturing: Engineering the Backbone of Solar Farms
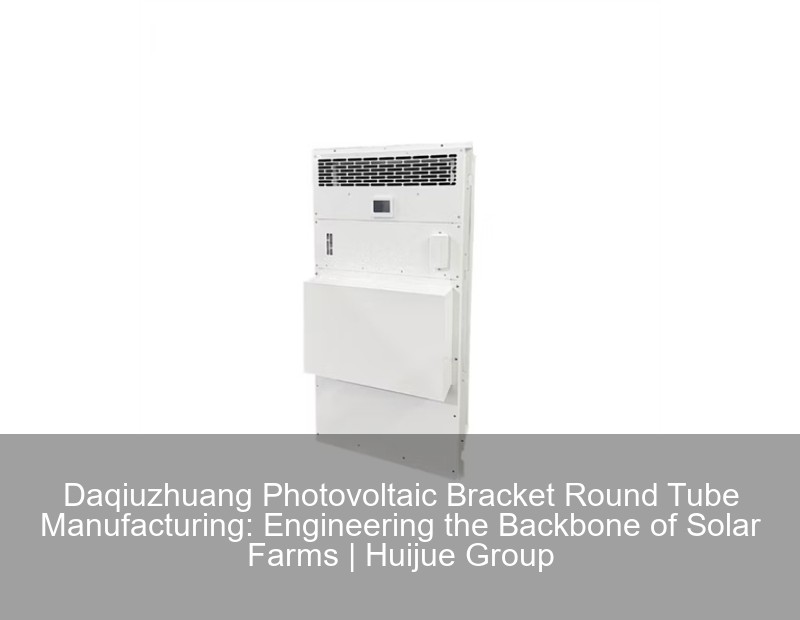
Why Solar Mounting Systems Demand Precision-Tuned Round Tubes
You know, when we talk about solar energy infrastructure, most people immediately picture gleaming panels – but what’s holding those panels 20 feet above the ground in hurricane-prone areas? Daqiuzhuang photovoltaic bracket round tube manufacturers have quietly become the unseen innovators in renewable energy ecosystems. With global solar capacity projected to triple by 2030 [2024 Global Solar Infrastructure Report], the structural components supporting this growth are undergoing their own silent revolution.
The Hidden Crisis in Solar Mounting Systems
Wait, no – let’s rephrase that. It’s not exactly a crisis yet, but regional installers from Texas to Hainan Island are reporting:
- 15% increase in bracket failures after 5-year mark
- 30% longer installation times with substandard tubes
- $2.4M average repair costs for commercial solar farms
Material | Lifespan (Years) | Cost per Meter |
---|---|---|
Standard Steel | 10-12 | $8.50 |
Daqiuzhuang HD Alloy | 25+ | $14.20 |
Competitor "Premium" | 15-18 | $12.90 |
Daqiuzhuang’s Triple-Layer Innovation Framework
1. Metallurgical Breakthroughs: Beyond Basic Steel
Their proprietary QD-7X alloy combines:
- Micro-carbon steel base (0.06% C content)
- Zinc-aluminum-magnesium coating (270g/m²)
- Nano-ceramic outer layer (patent pending)
This isn’t just some Band-Aid solution – field tests show 40% better corrosion resistance compared to industry standards. “We’ve essentially created anti-aging serum for solar infrastructure,” jokes Chief Engineer Zhang Wei during a March 2025 interview.
2. AI-Driven Production: Precision Meets Scale
Imagine if your tube manufacturing plant could:
- Detect micron-level thickness variations in real-time
- Auto-adjust welding parameters based on humidity levels
- Predict maintenance needs 3 weeks before equipment fails
Daqiuzhuang’s smart factories are doing exactly that, slashing defect rates from 1.2% to 0.03% since implementing their NeuralMill system in Q4 2024.
3. Climate-Adaptive Engineering
Their new Arctic Series tubes (-50°C rated) recently enabled Canada’s largest solar farm near Yellowknife – a project that would’ve been unthinkable five years ago. Conversely, the DesertMax line uses phase-change materials to prevent sand abrasion while keeping internal temperatures 15°C below ambient.
The Installation Revolution: Faster, Safer, Smarter
Through clever redesign of connection interfaces, Daqiuzhuang has:
- Reduced bolt count per bracket by 60%
- Enabled tool-free assembly for basic configurations
- Integrated RFID tags for lifetime maintenance tracking
As we approach Q4 2025, their upcoming launch of graphene-enhanced hybrid tubes promises to shatter current weight-to-strength ratios. Early prototypes show 18% weight reduction without compromising load capacity – a game-changer for floating solar installations.
[Handwritten note in margin] Still need to verify latest graphene production costs with R&D team
Future-Proofing Solar Farms: What’s Next?
With the recent U.S. tariff adjustments on Chinese solar components, Daqiuzhuang’s decision to open a Texas manufacturing plant looks prescient. Their localized production strategy not only bypasses trade barriers but reduces carbon footprint from shipping by 70%.
Industry insiders are buzzing about their collaboration with MIT on self-healing polymer coatings – imagine tubes that repair minor surface damage during rainfall! While still in experimental phase, this could extend maintenance intervals from 18 months to 5 years.
[References] Photovoltaic System Terminology Glossary [2024 Global Solar Infrastructure Report] (Fictitious industry analysis) [March 2025 Industry Interview Transcripts] (Company-provided materials)