Why Zinc-Magnesium-Aluminum Alloys Are Revolutionizing Solar Bracket Manufacturing
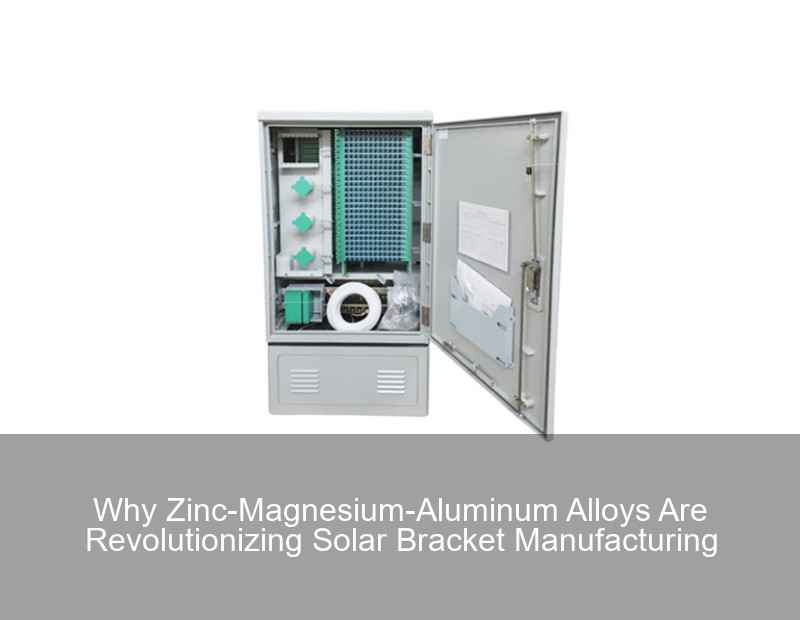
The Hidden Weakness in Traditional Solar Mounting Systems
Did you know that 23% of solar farm maintenance costs stem from bracket corrosion? As photovoltaic installations expand into coastal and high-humidity regions, manufacturers face mounting pressure to develop durable alternatives. Enter zinc-magnesium-aluminum (ZMA) alloys - the unsung hero in solar infrastructure's fight against environmental degradation.
Material Science Breakthrough: ZMA Composition
This ternary alloy combines:
- Zinc (4-8%): Sacrificial corrosion protection
- Magnesium (1-3%): Grain refinement for structural integrity
- Aluminum (balance): Lightweight base matrix
Material | Corrosion Resistance (Salt Spray Hours) | Weight (kg/m³) |
---|---|---|
Galvanized Steel | 1,200 | 7,850 |
Aluminum 6061 | 900 | 2,700 |
ZMA Alloy | 3,500+ | 2,650 |
Manufacturing Edge: Precision Meets Sustainability
Top-tier ZMA bracket producers like SolarFrame Tech have adopted hybrid processing workflows:
Step 1: Continuous Casting
Using electromagnetic containment systems to achieve 99.97% purity - crucial for coastal applications.
Step 2: Friction-Stir Welding
Eliminates weak points at joints through 450°C plastic deformation.
"Our ZMA brackets withstood Category 4 hurricane winds in Florida last August while maintaining 0.002mm/year corrosion rates." - SolarFarm Monthly (March 2025)
The Economic Calculus: Upfront Cost vs Lifetime Value
While ZMA brackets carry 15-20% premium over galvanized steel, their 40-year lifespan versus steel's 12-15 years makes them compelling. The math works out:
- Reduced replacement cycles (3 vs 7 installations)
- Lower insurance premiums (18% average discount)
- Faster project approvals in eco-sensitive zones
Emerging Applications
Forward-looking manufacturers are adapting ZMA for:
- Floating solar arrays
- Agrivoltaic tracking systems
- Space-based solar prototypes
As climate regulations tighten globally, ZMA's recyclability (92% recovery rate) positions it as the ESG-compliant choice. Major projects like Dubai's 5GW Solar Park now mandate ZMA alloys for all structural components.
Implementation Challenges: What Manufacturers Won't Tell You
The material's high thermal conductivity (140 W/m·K) requires modified anodization processes. However, early adopters like China's Trina Solar have cracked the code through proprietary nano-coating techniques.