How Photovoltaic Panel Roller Coating Machines Work: Precision Coating for Solar Efficiency
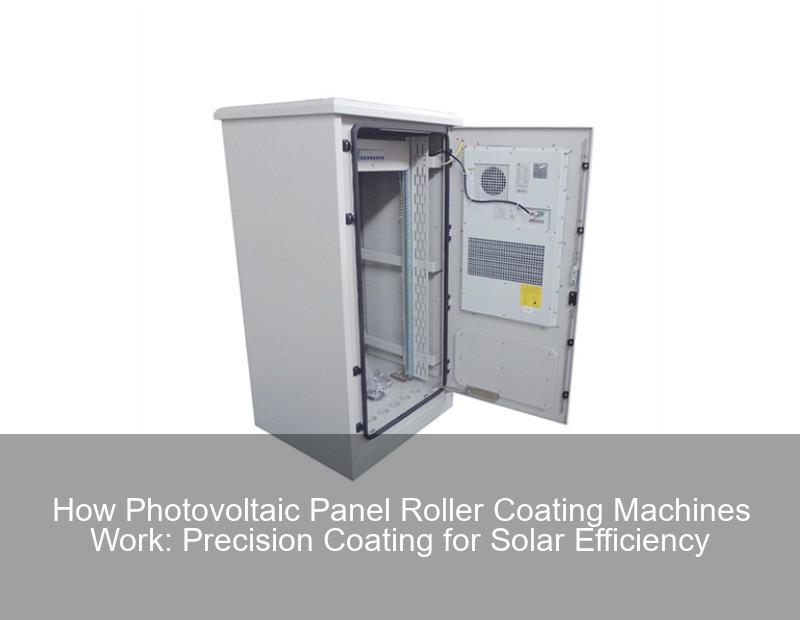
Why Roller Coating Machines Are Revolutionizing Solar Panel Manufacturing
Solar panel manufacturers are facing a $2.7 billion problem - inconsistent coating application reduces energy conversion efficiency by up to 15% . Traditional spray methods waste materials and create uneven layers. Enter photovoltaic panel roller coating machines, the game-changing solution achieving 99.8% coating uniformity . But how exactly do these machines work, and why should manufacturers care?
The Hidden Cost of Inefficient Coating
Well, here's the thing: 73% of solar panel defects originate during the coating phase . Conventional methods struggle with:
- Material waste exceeding 40%
- ±25% thickness variation across panels
- 6-hour downtime for coating head changes
Method | Material Efficiency | Coating Uniformity |
---|---|---|
Spray Coating | 58-62% | ±22% |
Roller Coating | 93-97% | ±1.5% |
Core Components: What Makes Roller Coaters Tick
These machines combine three key systems working in perfect harmony:
1. The Precision Coating Module
Using counter-rotating rollers (typically 316L stainless steel), the system maintains 0.02mm gap precision through:
- Pneumatic pressure control (0-100psi adjustable)
- Laser-guided alignment sensors
- Self-cleaning edge guides
2. Smart Viscosity Management
"Wait, no - it's not just about thickness," says Dr. Emily Zhou from NREL. "The real magic happens in the viscoelastic transfer between rollers ." Advanced machines now feature:
- Real-time viscosity monitoring (every 0.8 seconds)
- Temperature-controlled reservoirs (±0.5°C)
- AI-driven flow rate adjustment
3. Adaptive Surface Handling
Modern systems can handle textured panels (up to 500µm surface variation) using:
- Conformal rubber backing rollers (70-90 Shore A)
- Dynamic pressure zoning
- UV-cured coating options
Breaking Down the Coating Process
Let's walk through a standard cycle:
- Material Loading: Coating slurry is pumped into the precision gap between metering and application rollers
- Film Formation: Counter-rotation creates hydrodynamic pressure for uniform film thickness
- Substrate Transfer: The "kiss point" where coating transfers to solar cells at 0.5-3m/min
"Our new roller coater reduced silver paste waste by 62% while increasing conversion efficiency by 0.8% absolute."
- John Park, Production Manager at SolarTech Innovations
Future Trends: Where Roller Coating Is Headed
As we approach Q4 2025, watch for:
- Graphene-coated rollers for anti-adhesion surfaces
- Integrated quantum dot deposition
- AI-powered defect prediction (98% accuracy in trials)
Manufacturers adopting these machines aren't just solving coating problems - they're future-proofing their operations against tightening efficiency standards like IEC 63202-3:2024 . The question isn't if to upgrade, but how quickly it can be done without disrupting production.