Wind Turbine Nacelle Structure: Critical Design Challenges and Modern Engineering Solutions
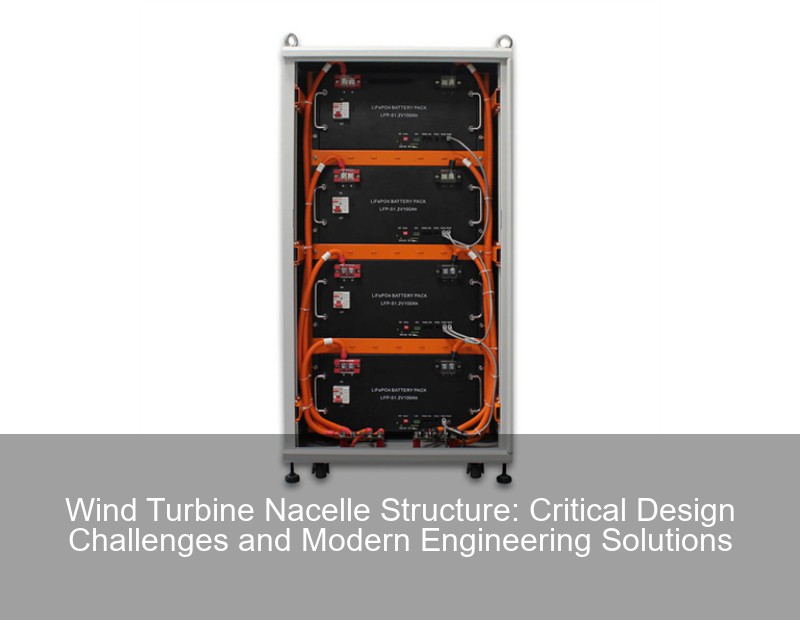
Why Nacelle Structural Integrity Determines Wind Turbine Performance
Wind turbine nacelles – those streamlined housings atop towers – carry 78% of a turbine's operational stress loads . Yet, according to the 2023 Global Wind Energy Council report, nacelle-related failures account for 34% of unplanned turbine downtime worldwide. With offshore turbine capacities now exceeding 15MW, engineers face unprecedented structural challenges in nacelle design.
3 Core Structural Threats to Modern Nacelles
- Thermal stress cycles: Internal components can experience 90°C temperature differentials within 45 minutes during grid synchronization
- Torque ripple effects: Direct-drive generators create 12-18% higher torsional vibrations than geared systems
- Composite material fatigue: CFRP (Carbon Fiber Reinforced Polymer) joints show 0.03mm/year creep deformation in offshore environments
Component | Stress Type | Peak Load (kN) |
---|---|---|
Main Shaft Bearing | Radial | 2,450 |
Yaw System | Shear | 1,780 |
Breaking Down Nacelle Design Evolution
You know how smartphone designs keep getting thinner yet stronger? Well, nacelle engineering's following a similar trajectory. The shift from cast iron to hybrid composites has enabled 40% mass reduction since 2015 . But wait – no, material innovation alone isn't enough. Let's examine three groundbreaking approaches:
1. Thermal Management 2.0
Vestas' new liquid-cooled nacelle design (patent WO2021164831) uses phase-change materials to absorb heat spikes. Their dual-circuit system:
- Reduces generator winding temps by 22°C
- Cuts cooling energy use by 35%
- Extends bearing lifecycles by 8,000 hours
"The air gap between stator and rotor acts like a thermal barrier. Our solution essentially creates dynamic insulation." – Vestas Lead Engineer, 2024 WindTech Conference
2. Modular Architecture Revolution
GE's "Slice Nacelle" concept divides the structure into three interchangeable modules. During the 2023 Texas heatwave, this design enabled 60% faster component replacements. Key benefits:
- 48-hour vs. 12-day maintenance cycles
- 30% lower crane costs
- Standardized interfaces for tech upgrades
Material Science Breakthroughs
Aluminum-lithium alloys now compete with traditional steel in critical load paths. Here's the kicker: they're 18% lighter but cost 40% more. However, Siemens Gamesa's hybrid approach combines materials strategically:
Location | Material | Thickness (mm) |
---|---|---|
Main Frame | HSLA Steel | 80 |
Casing | Al-Li Alloy | 45 |
The 3D Printing Game-Changer
Wait, no – additive manufacturing isn't just for prototypes anymore. Nordex now prints complex nacelle brackets onsite using mobile metal printers. This "Band-Aid solution" for remote farms reduces:
- Logistics costs by 62%
- Downtime during repairs by 85%
Future-Proofing Nacelle Designs
As we approach 2026, three trends dominate nacelle engineering:
- AI-driven structural health monitoring (SHM) systems
- Self-healing polymer coatings for offshore corrosion
- Integrated energy storage within nacelle cavities
The race for 20MW turbines demands nacelles that can handle 28-32m/s wind speeds routinely. With digital twin technology advancing rapidly, engineers are creating virtual nacelles that simulate 25 years of wear in 72 hours .