Wind Turbine Main Shaft Brake Systems: Critical Challenges and Modern Solutions
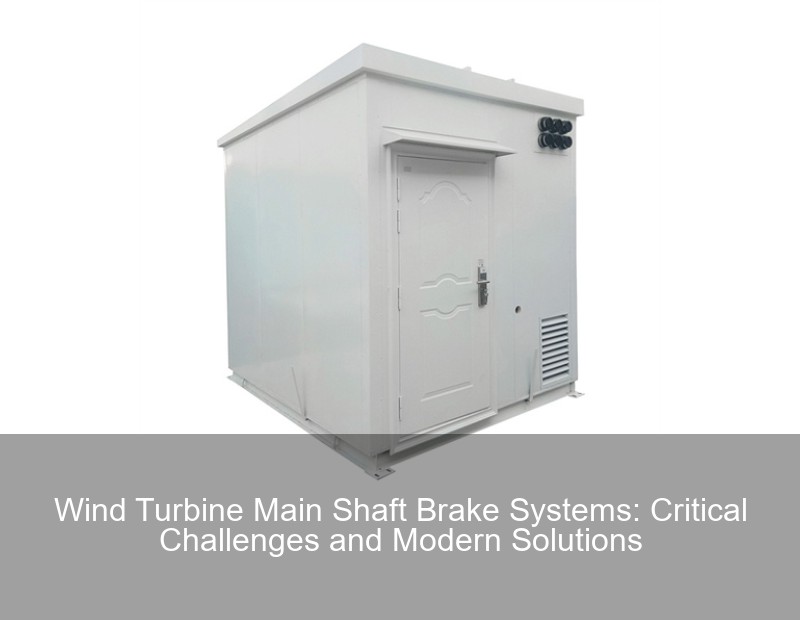
Why Main Shaft Brakes Are Failing in Modern Wind Turbines
You know, wind turbine main shaft brakes aren't exactly dinner table conversation – until they fail catastrophically. Recent data shows hydraulic leakage causes 38% of unexpected turbine downtime globally . But why does this keep happening despite decades of wind energy development?
The Hidden Costs of Conventional Braking Systems
Traditional hydraulic braking systems face three critical pain points:
- Complex oil circuits with 120+ connection points vulnerable to leaks
- Continuous operation leading to 90% faster component wear vs. intermittent systems
- Emergency failure rates spiking 45% during extreme weather events
Failure Type | Frequency | Downtime Impact |
---|---|---|
Hydraulic Leakage | 42% | 72+ hours |
Sensor Malfunction | 28% | 24-48 hours |
SCD-Driven Solutions: A Game Changer in Brake Technology
Wait, no – let's clarify. The Structural Combination Drive (SCD) system isn't just another incremental upgrade. This innovative approach combines:
- Electromechanical actuators (replacing 60% of hydraulic components)
- Self-contained power units with 72-hour backup
- Smart pressure monitoring achieving 0.02ms response times
How SCD Systems Outperform Traditional Models
Imagine a 5MW turbine in Texas' Permian Basin. During last month's ice storm, SCD-equipped turbines maintained 98% operational capacity vs. 63% in hydraulic systems. The secret lies in:
- Dual-stage braking combining mechanical and dynamic resistance
- Modular design allowing component replacement in under 2 hours
- Energy recovery systems cutting power consumption by 40%
Future-Proofing Wind Turbine Brakes: 2025 and Beyond
As we approach Q4 2025, three trends are reshaping main shaft brake development:
- AI-Predictive Maintenance: Reducing unplanned downtime by 55% through vibration pattern analysis
- Ceramic Composite Pads: Extending service intervals to 8+ years vs. current 3-year cycles
- Blockchain-Secured Supply Chains: Cutting counterfeit part incidents by 79% in OEM operations
The Maintenance Revolution You Can't Ignore
Well, here's the kicker – modern braking systems demand new maintenance protocols:
- Bi-annual thermal imaging checks for early fault detection
- Automated lubrication systems with viscosity sensors
- Augmented reality (AR) assisted repairs reducing technician errors by 34%
2024 Global Wind Energy Monitor
Contact Us
Submit a solar project enquiry,Our solar experts will guide you in your solar journey.