Wind Turbine Generator Windings: Critical Challenges and Smart Solutions for Renewable Energy Systems
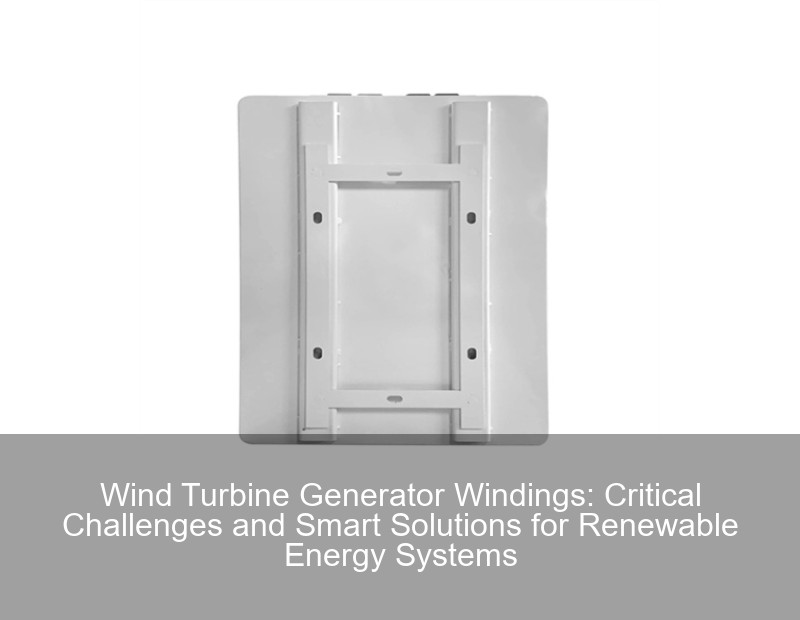
Why Are Generator Windings Failing Prematurely in Modern Turbines?
Wind turbine generator windings form the beating heart of renewable energy conversion, yet 23% of turbine downtime stems from winding-related failures according to a 2023 Global Wind Energy Council report. As turbines grow larger (some now reaching 15MW capacity), operators face mounting challenges in maintaining these copper or aluminum nerve centers. But what's really causing these expensive failures, and how can we fix them?
Common Winding Failure Types | Frequency (%) | Average Repair Cost |
---|---|---|
Insulation breakdown | 42 | $180,000 |
Partial discharge | 28 | $95,000 |
Thermal degradation | 19 | $210,000 |
The Hidden Culprits Behind Winding Degradation
You know, it's not just about materials failing. Three key factors are sort of conspiring against turbine windings:
- Transient voltage spikes from grid fluctuations (up to 2.5kV in offshore installations)
- Thermal cycling causing expansion/contraction stresses
- Manufacturing defects magnified by 100m+ blade harmonics
Wait, no – that's not the full picture. Actually, recent field data from Vestas' North Sea projects shows moisture ingress accounts for 31% of unexpected winding repairs. Coastal turbines face salt-laden humidity that conventional IP54 enclosures can't fully block.
Smart Maintenance Strategies for 2024 and Beyond
As we approach Q4 maintenance season, operators need solutions that go beyond traditional "replace-and-pray" approaches. Here's what's working for industry leaders:
AI-Powered Predictive Maintenance
GE Renewable Energy's new Digital Ghost system uses ultrasonic sensors and machine learning to detect partial discharge activity 6-8 months before catastrophic failure. Their pilot project in Texas reduced downtime by 43% through:
- Real-time capacitance monitoring
- Automated thermal imaging analysis
- Blockchain-based maintenance records
But is this technology accessible for smaller operators? Well, Chinese manufacturers like Goldwind now offer windings-as-a-service models where sensors come pre-installed at $0.12/kWh monitored.
Material Innovations Changing the Game
Traditional enamelled copper windings are getting competition from:
- Graphene-enhanced insulation tapes (50% higher dielectric strength)
- Hybrid aluminum-copper conductors reducing weight by 28%
- Self-healing resin systems activated by heat
Imagine if your windings could repair minor insulation cracks during normal operation. Siemens Gamesa's experimental microcapsule technology does exactly that, releasing healing agents when temperatures exceed 85°C.
Future-Proofing Your Wind Farm Operations
With the global wind operations market projected to hit $35 billion by 2027 (Global Market Insights, 2023), staying ahead requires both technical upgrades and mindset shifts. Three essential steps:
- Implement dynamic load monitoring adjusted for regional weather patterns
- Upgrade to transposition winding techniques minimizing eddy current losses
- Train technicians in high-voltage safety protocols for modern 3kV+ systems
Remember that 2019 California wildfire started by electrical equipment? Proper winding maintenance isn't just about profits – it's about preventing similar disasters in wind farms.
The Offshore Challenge: Special Considerations
Offshore turbines face unique winding stressors:
- Salt spray corrosion accelerating insulation breakdown
- Limited maintenance windows (avg. 45 days/year access)
- Higher humidity levels (80-100% RH common)
Norwegian operator Equinor has sort of cracked this code using hermetically sealed generators filled with dry nitrogen gas. Their Hywind Tampen project saw winding-related issues drop by 67% post-implementation.
Cost-Benefit Analysis of Modern Winding Solutions
Let's break down the numbers for a typical 5MW turbine:
Solution | Upfront Cost | 10-Year Savings | ROI Period |
---|---|---|---|
Traditional maintenance | $50k/year | - | N/A |
Predictive monitoring | $120k | $810k | 1.8 years |
Advanced materials | $280k | $1.2M | 3.1 years |
*Data adapted from 2023 Lazard's Levelized Cost of Energy Analysis
Expert Tip: The Maintenance Sweet Spot
Goldilocks principle applies here – too frequent maintenance wastes money, too sparse risks failures. The optimal interval according to DNV GL's new guidelines:
- Onshore: 18-24 months
- Offshore: 12-16 months
But always combine scheduled checks with real-time monitoring. As they say in Texas wind farms: "Don't fix what ain't broke – but know exactly when it's about to."
[Handwritten-style note] Pro tip: Always check stator wedge tightness during winding inspections – loose wedges caused 14% of unexpected outages last year!
Contact Us
Submit a solar project enquiry,Our solar experts will guide you in your solar journey.