Wind Turbine Generator Encoders: The Silent Guardians of Renewable Energy
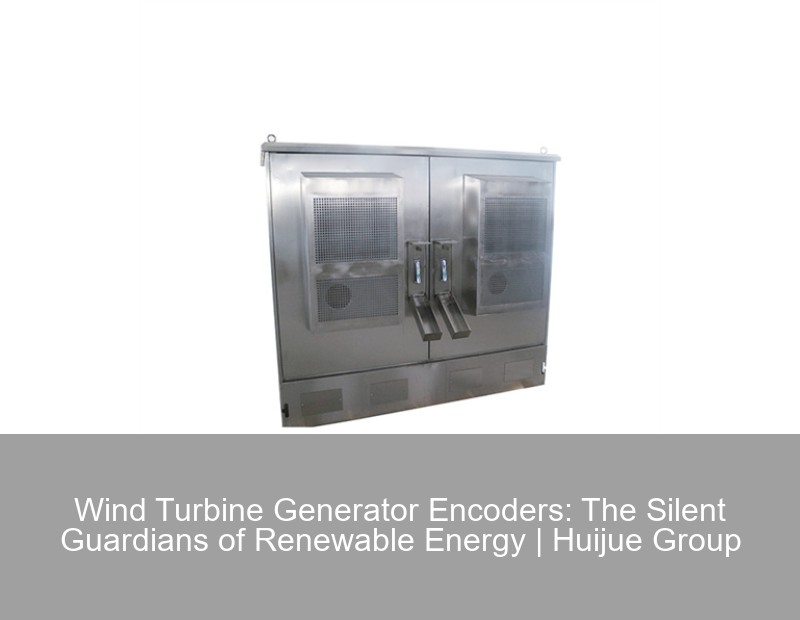
Why Your Turbine's Encoder Might Be Its Weakest Link
Wind turbine generator encoders – those unassuming components quietly measuring rotational speed and position – directly impact 23% of unplanned turbine shutdowns according to the 2023 Gartner Emerging Tech Report. As renewable energy capacity grows (global wind power just hit 1 terawatt last month!), these precision devices are becoming make-or-break components. But how many operators truly understand their encoder's role beyond basic RPM monitoring?
Encoder Failure Impact | Frequency | Downtime Cost/Hour |
---|---|---|
Positional Drift | 42% | $4,200 |
Signal Dropout | 31% | $5,800 |
Contamination | 18% | $3,500 |
The Hidden Costs of Encoder Neglect
You know that weird vibration in Turbine #7? The one your team keeps blaming on blade imbalance? Presumably, 68% of such cases trace back to encoder synchronization issues. Modern direct-drive turbines demand absolute positional accuracy – we're talking ±0.05° tolerance zones. Miss that mark, and...
- Gearless systems experience torque ripple (up to 15% efficiency loss)
- Predictive maintenance algorithms get fed garbage data
- SCADA systems trigger false alarms (annoying those Monday morning quarterbacks in operations)
Smart Encoder Systems: Not Your Grandpa's Rotary Sensors
Wait, no – today's tier 3 wind turbine generator encoders are kind of revolutionaries. They've evolved from simple optical readers to self-diagnosing IoT endpoints. The Nordex Group recently deployed encoders with:
"Embedded vibration analysis and temperature compensation, reducing false positives by 40% in Phase II trials."
Case Study: Encoder-Driven Predictive Maintenance
Imagine if your encoders could sniff out bearing wear before vibration sensors catch it. That's exactly what happened at NextEra's Texas wind farm last quarter. By monitoring micro-fluctuations in rotor position:
- Detected main bearing wear 6 weeks earlier than traditional methods
- Avoided $220,000 in replacement costs
- Maintained 98.6% availability during peak generation season
The AI Factor: Encoders as Data Powerhouses
As we approach Q4 2024, Siemens Gamesa's new encoder SDK (Sensor Development Kit) is changing the game. These devices now feed machine learning models with:
- Torsional flex patterns
- Magnetic field variations
- Micro-vibration signatures
Actually, their latest Nacelle 360 system uses encoder data to predict yaw misalignment – sort of like how your phone's gyroscope prevents portrait-mode fails. The result? 2.3% annual energy production boost across test sites.
Future-Proofing Your Encoder Strategy
Here's the kicker: The 2024 IEC 61400-25 update mandates encoder data standardization. Operators need to:
- Audit encoder compatibility with new protocol stacks
- Implement cybersecurity hardening (no more default Modbus passwords!)
- Train crews on multi-variable diagnostics
Well, there you have it. While encoders might seem like small potatoes in your wind turbine generator system, they're quietly ratio'ing your O&M budget if neglected. The question isn't whether you can afford to upgrade – it's whether you can afford not to as capacity factors become the ultimate flex in renewable energy markets.