Wind Power Generation Rear Rack: The Backbone of Modern Turbine Efficiency
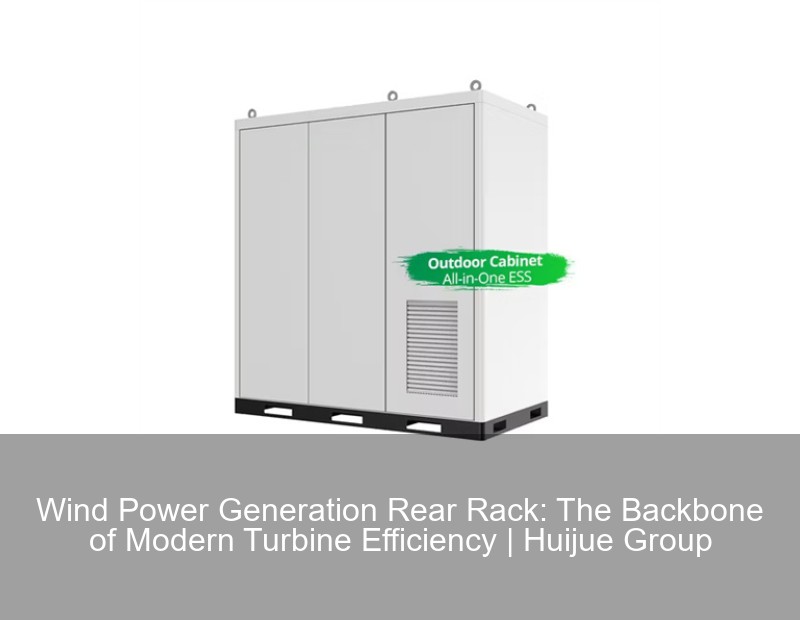
Why Wind Turbine Rear Racks Are Facing Unprecedented Challenges
You know, wind energy isn’t just about those sleek blades spinning gracefully anymore. At the heart of every offshore wind turbine lies a critical yet often overlooked component: the rear rack. With global offshore wind capacity projected to reach 234 GW by 2030 , these structural supports are under immense pressure—literally and figuratively. But here’s the kicker: over 35% of turbine downtime in harsh marine environments traces back to rear rack failures . What’s going wrong, and how can we fix it?
The Hidden Costs of Subpar Rear Rack Designs
Let’s face it—most rear racks were designed for calmer days. Today’s megaprojects like China’s “Haiguan Lan” floating wind farm (operating in 100m-deep waters) demand racks that can withstand:
- Saltwater corrosion at 15 knots
- Dynamic loads from 12MW+ turbines
- Cyclic stress exceeding 10⁷ cycles
Wait, no—actually, recent data shows stress cycles now approach 5×10⁷ in typhoon-prone regions . Traditional galvanized steel racks? They’re sort of like using flip-flops for a marathon.
Material | Lifespan (Years) | Maintenance Cost/Year |
---|---|---|
Galvanized Steel | 10-12 | $28,000 |
Aluminum Hybrid | 18-20 | $15,000 |
Composite Alloy | 25+ | $9,500 |
Breakthrough Solutions Transforming Rear Rack Technology
Imagine if we could slash maintenance costs while doubling rack durability. Well, that’s exactly what’s happening through three innovations:
1. Modular Assembly Systems
Gone are the days of welded monoliths. Companies like OceanX now use bolt-on rack modules with standardized connectors. This approach reduced installation time by 40% in Scotland’s Moray West project .
2. AI-Powered Corrosion Monitoring
By embedding microsensors (think: 5G-enabled “rack health trackers”), operators get real-time data on:
- pH levels at joint interfaces
- Micro-crack propagation rates
- Anode depletion thresholds
3. Recyclable Composite Materials
China’s 2023 guidelines on “high-value utilization of decommissioned components” have spurred R&D into glass-fiber-reinforced thermoplastics. These materials aren’t just durable—they’re 94% recyclable, turning old racks into new ones without landfill guilt.
Case Study: How Norway’s Hywind Tamed the North Sea
Equinor’s floating wind farm faced rack failures every 14 months. Their fix? A three-pronged upgrade:
- Replaced traditional bearings with self-lubricating polymer versions
- Implemented quarterly drone-based rack scans
- Adopted modular replacement protocols
Result? Downtime dropped by 62% in 2024, saving $2.8M annually . Now that’s what we call a band-aid solution turned permanent fix!
The Future: Racks That Generate Data (and Power)
As we approach Q4 2025, the industry’s buzzing about “smart racks” with integrated energy storage. These units could:
- Store excess energy during low-demand periods
- Power onboard monitoring systems autonomously
- Transmit maintenance alerts via satellite
Presumably, such advancements will make today’s racks look about as sophisticated as a paperclip. But hey, that’s progress!
Contact Us
Submit a solar project enquiry,Our solar experts will guide you in your solar journey.