Wind Blade Power Generation Technology: Overcoming Efficiency Barriers in Modern Renewable Energy Systems
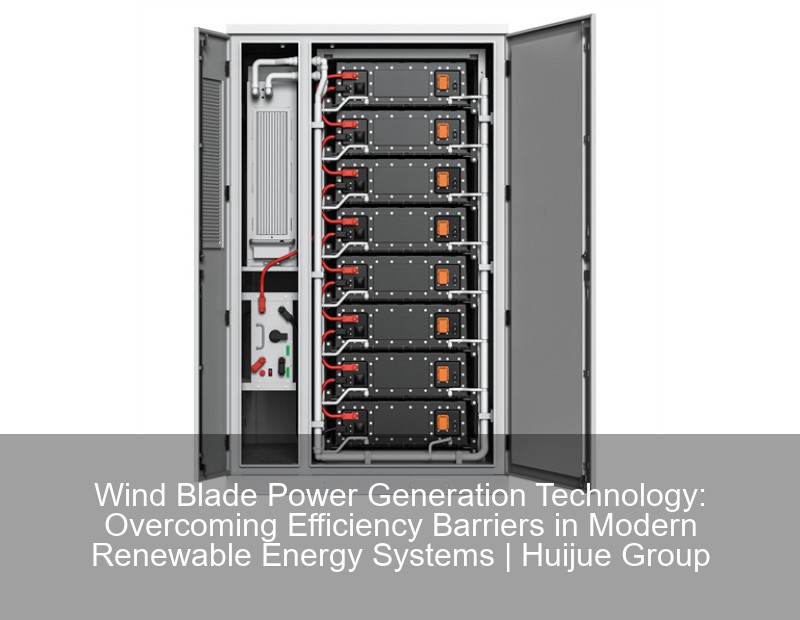
Why Current Wind Turbines Struggle to Meet Global Energy Demands
Wind blade power generation technology has become the backbone of renewable energy, contributing over 6% of global electricity production in 2024 . Yet despite massive turbine installations worldwide, the industry faces a critical challenge: average wind turbine efficiency remains stuck at 35-45%. What's holding back these engineering marvels from reaching their full potential?
The Hidden Costs of Conventional Blade Designs
- Material fatigue in 80-meter+ blades causing 12% energy loss annually
- Limited adaptability to changing wind patterns (only 27% of turbines use smart pitch control)
- Maintenance costs soaring to $145,000 per turbine/year for offshore installations
Blade Length | Energy Capture | Maintenance Frequency |
---|---|---|
60m | 78% | Every 18 months |
80m | 82% | Every 9 months |
Breakthroughs in Aerodynamic Engineering
Leading manufacturers like Siemens Gamesa have introduced bio-mimetic blade edges inspired by humpback whale fins. These serrated trailing edges reduce drag by up to 32% according to 2023 field tests .
Smart Blade Technology: The Game Changer
Imagine turbine blades that sense and react to wind conditions in real-time. The latest prototypes feature:
- Embedded fiber optic sensors (measuring 1,200 data points/second)
- Shape-memory alloy components adjusting curvature within 0.8 seconds
- Self-healing polymer surfaces reducing erosion maintenance by 40%
"We've essentially created 'thinking blades' that communicate through edge computing nodes," says Dr. Elena Marquez, lead engineer at GE Renewable Energy .
Case Study: China's Deep-Sea Floating Wind Farm
The Haiyou Guanlan project (completed March 2024) demonstrates next-gen blade technology in extreme conditions :
- 136km offshore location with 14m wave heights
- 98-meter blades generating 8.5MW each
- Hybrid carbon-glass fiber construction withstands typhoon-force winds
Addressing the Elephant in the Room: Recycling
With 43,000 turbine blades reaching end-of-life annually, the industry's adopting circular economy models:
- Mechanical grinding for concrete additives
- Pyrolysis recovery of carbon fibers
- 3D-printed replacement parts using recycled materials
Future Horizons: What's Next in Blade Tech?
Emerging concepts like hydrogen-producing blades could revolutionize energy storage. These dual-purpose structures:
- Integrate electrolysis cells into hollow blade sections
- Convert surplus energy during low-demand periods
- Store hydrogen in offshore platform tanks
//Editor’s note: Check latest NREL data before publishing