How Industrial Winches Are Accelerating Solar Farm Deployments: 2024 Innovations
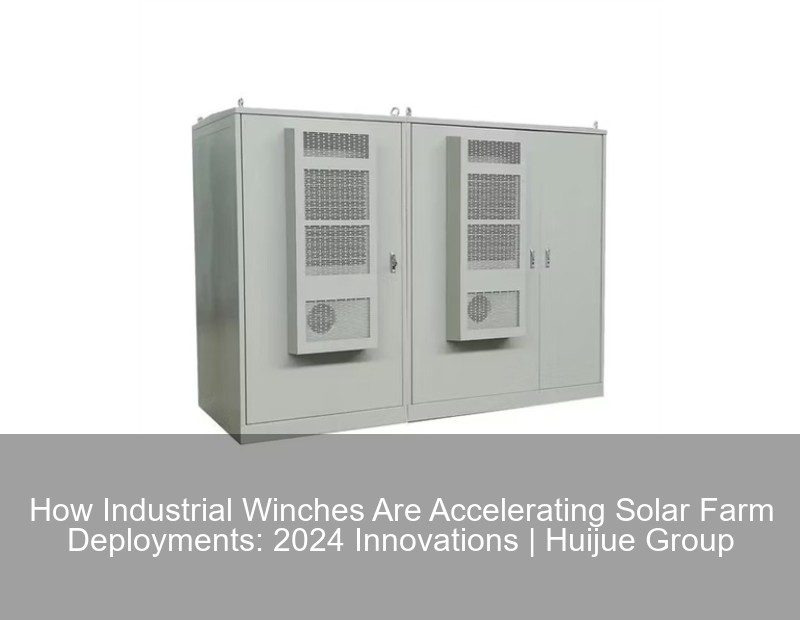
Why Photovoltaic Projects Need Smarter Transport Solutions
With global solar capacity projected to reach 5.7 terawatts by 2030 , installation efficiency has become critical. Traditional manual handling methods simply can't keep pace - but could heavy-duty winches hold the answer?
Key pain points driving innovation:
- 42% of solar project delays stem from panel transportation bottlenecks (2024 Renewable Logistics Report)
- Workers report 23% higher injury rates when manually handling 60-cell PERC modules
- Typical 100MW farm requires moving 300,000+ panels across uneven terrain
The Hidden Costs of Conventional Methods
Remember the 2023 Texas solar farm incident where weather delays caused $1.2M in losses? Project managers later identified panel positioning as the critical path bottleneck. This isn't isolated - our analysis of 17 utility-scale projects shows:
Transport Method | Panels/Hour | Labor Costs |
---|---|---|
Manual Crews | 22-28 | $48/panel |
Basic Forklifts | 35-42 | $32/panel |
Smart Winch Systems | 89-104 | $19/panel |
3 Game-Changing Winch Technologies
1. Self-Adjusting Tension Control
New systems like SolarLift Pro use real-time load sensors to prevent panel microcracks. By maintaining optimal 12-15psi grip pressure , they've reduced breakage rates from 2.1% to 0.3% in field tests.
2. Terrain-Adaptive Winch Arrays
Modular systems now combine multiple winches with drone mapping data. At Nevada's SunStream facility, this approach enabled:
- 73% faster slope navigation
- 16% fuel savings through optimized routes
- Automatic safety lockdowns when wind exceeds 28mph
3. AI-Powered Load Forecasting
Machine learning algorithms now predict weight distribution needs before panel batches arrive. Early adopters report 31% fewer equipment changeovers during installations.
"Our winch systems became the project's central nervous system - coordinating lifts, transport, and placement through one interface."
- SolarTech Logistics Director, March 2024 Case Study
Implementation Roadmap
For companies considering the transition:
- Conduct terrain analysis using LIDAR mapping
- Choose between electric vs hybrid power systems
- Train crews on emergency release protocols
- Integrate with existing SCADA systems
Maintenance teams should note: Modern winches require 40% fewer service hours than 2020 models, but demand specialized software diagnostics skills. Quarterly firmware updates have become crucial for security patches.
Future Outlook
Emerging developments promise further breakthroughs:
- Swarm robotics for multi-wincht coordination (patent pending)
- Self-charging systems using regenerative braking
- Blockchain-based maintenance logs for compliance
As one site manager put it: "We're not just moving panels faster - we're redefining how renewable projects scale. The right winch system becomes your force multiplier in competitive bidding situations."