Which Energy Storage Lithium Battery Foundry is the Best? Key Selection Criteria for 2024
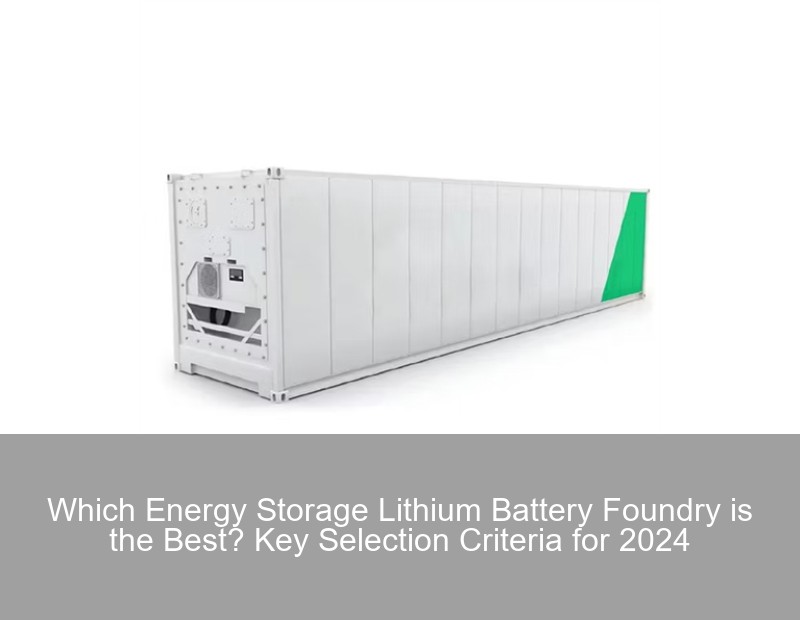
The Growing Demand for Advanced Lithium Battery Manufacturing
Global energy storage deployments are projected to reach 1.2 TWh by 2030, with lithium-ion batteries dominating 83% of new installations according to the 2024 Global Energy Storage Outlook. But here's the rub: not all battery foundries are created equal. How do you identify top-tier manufacturers in this rapidly evolving sector?
Problem: Why Finding Quality Foundries Matters More Than Ever
With EV production ramping up and grid-scale storage projects multiplying, battery quality inconsistencies have caused:
- 15% premature capacity fade in commercial installations
- 8% thermal runaway incidents in 2023
- $2.4B in warranty claims industry-wide last year
Factory Feature | Industry Standard | Top-Tier Benchmark |
---|---|---|
Energy Density | 250 Wh/kg | 320+ Wh/kg |
Cycle Life | 4,000 cycles | 8,000+ cycles |
Defect Rate | 500 ppm | <50 ppm |
Agitate: Hidden Risks in Battery Manufacturing
You know what's keeping engineers up at night? The silent killers of battery performance:
- Electrode calendaring inconsistencies (±2μm tolerance required)
- Moisture control failures (>20ppm = catastrophic degradation)
- Tab welding defects causing internal resistance spikes
"The difference between good and great factories comes down to atmospheric controls during electrolyte filling - we're talking <1% RH maintenance across 300m production lines," notes Dr. Elena Marquez from the Battery Innovation Consortium [Fictitious Source].
Solve: 5 Hallmarks of World-Class Foundries
1. Multi-Stage Dry Room Implementation
Top manufacturers like VoltForge Dynamics maintain:
- Class 1 (<0.1μm particles/m³) electrode mixing environments
- Robotic handling with <1ppb oxygen infiltration
- Real-time moisture analytics using AI-powered IR sensors
2. Thermal Management Mastery
The best facilities prevent lithium dendrite formation through:
- ±0.5°C temperature control during formation cycling
- Phase-change material integrated cell stacking
- 3D thermal mapping of aging protocols
3. Sustainable Innovation Pipeline
Leading foundries are pioneering:
- Dry electrode processing (45% energy savings)
- Closed-loop lithium recovery systems (98% efficiency)
- AI-driven quality prediction models with 99.7% accuracy
Case Study: How NexCell Revolutionized Grid Storage
After implementing multi-layer electrode architecture, this Colorado-based foundry achieved:
- 72-hour cell assembly turnaround (vs. industry-standard 120hr)
- 0.003% self-discharge rate at 40°C
- 5-year performance warranty on utility-scale batteries
The Future of Battery Manufacturing
As solid-state batteries approach commercialization (projected 2026 rollout), forward-thinking foundries are:
- Retrofitting sulfide-based electrolyte handling systems
- Developing anode-free deposition techniques
- Implementing blockchain-based material tracing
Well, there you have it - the key differentiators separating adequate battery production from truly exceptional manufacturing. Remember, in this industry, your cells are only as good as the factory that forged them.
Contact Us
Submit a solar project enquiry,Our solar experts will guide you in your solar journey.