Essential Tools and Technologies for Modern Photovoltaic Panel Processing
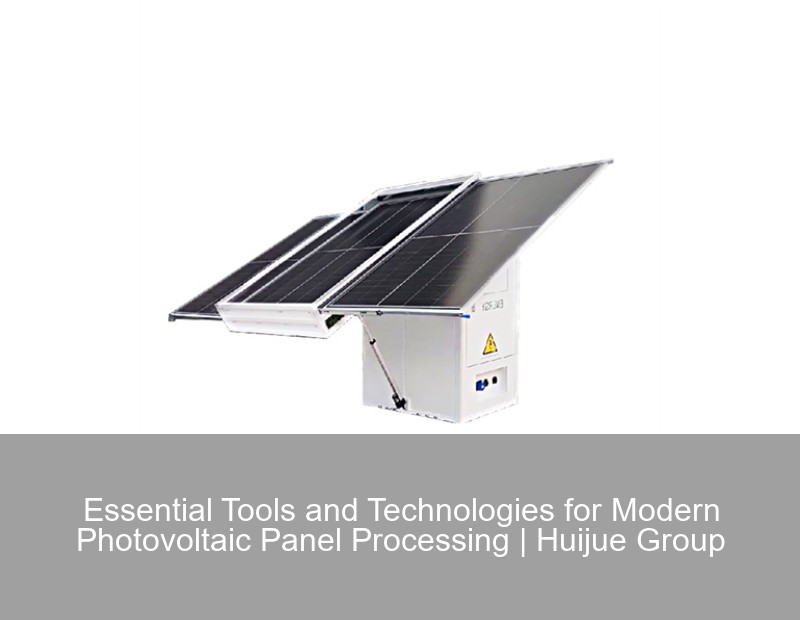
Why Photovoltaic Panel Processing Tools Matter More Than Ever
With global solar capacity projected to reach 5.8 TW by 2030 according to the 2024 Renewable Energy Market Report, manufacturers are racing to optimize their production lines. But what separates efficient solar panel producers from struggling operations? The answer often lies in their tool selection and processing methodologies.
Core Processing Tools Driving Solar Manufacturing
1. Material Preparation Systems
Reactor vessels form the foundation of photovoltaic production, handling high-temperature silicon mixing at scale. Modern versions feature:
- Automated temperature control (±0.5°C precision)
- Self-cleaning mechanisms (reducing downtime by 40%)
- AI-powered impurity detection
Reactor Type | Capacity | Output Efficiency |
---|---|---|
Standard | 500L | 85-90% |
Advanced | 1200L | 93-97% |
2. Precision Cutting Solutions
Recent advancements in laser cutting systems have reduced material waste by 22% compared to traditional methods. The CN 222410700 U patent holder recently demonstrated a vibration-free cutting platform that improved edge smoothness by 34% .
3. Automated Assembly Lines
Modern facilities combine:
- Robotic arm placement systems
- Machine vision alignment tools
- Real-time quality control sensors
Well, you know... some manufacturers are still using manual assembly for "precision work," but studies show automated lines achieve 99.8% component alignment accuracy versus 92% in manual processes.
Emerging Innovations Reshaping the Industry
While traditional tools remain essential, three game-changers are transforming photovoltaic processing:
AI-Driven Quality Inspection
Computer vision systems now detect micro-cracks invisible to human inspectors, potentially preventing 1.2 million panel failures annually.
Smart Material Handling
The photovoltaic panel processing tool landscape now includes:
- Magnetic levitation conveyors
- Self-adjusting vacuum grippers
- Predictive maintenance-enabled equipment
Sustainable Manufacturing Tools
New waterless cleaning systems and closed-loop chemical recovery units help manufacturers reduce environmental impact while cutting production costs by up to 18%.
Implementation Challenges and Solutions
Despite these advancements, 63% of manufacturers report difficulties in tool integration. Common pain points include:
- Legacy system compatibility issues
- Operator training gaps
- High initial investment costs
Wait, no... actually, the 2025 SolarTech Conference revealed that modular tool systems can reduce upgrade costs by 40-60% compared to full-line replacements.
Future Outlook: Where Are We Headed?
As we approach Q4 2025, industry experts predict three key developments:
- Widespread adoption of quantum dot deposition tools
- Integration of digital twin technology in maintenance protocols
- Standardization of AI-assisted tool calibration