The Essential Structure of Photovoltaic Panels: From Core Components to Cutting-Edge Innovations
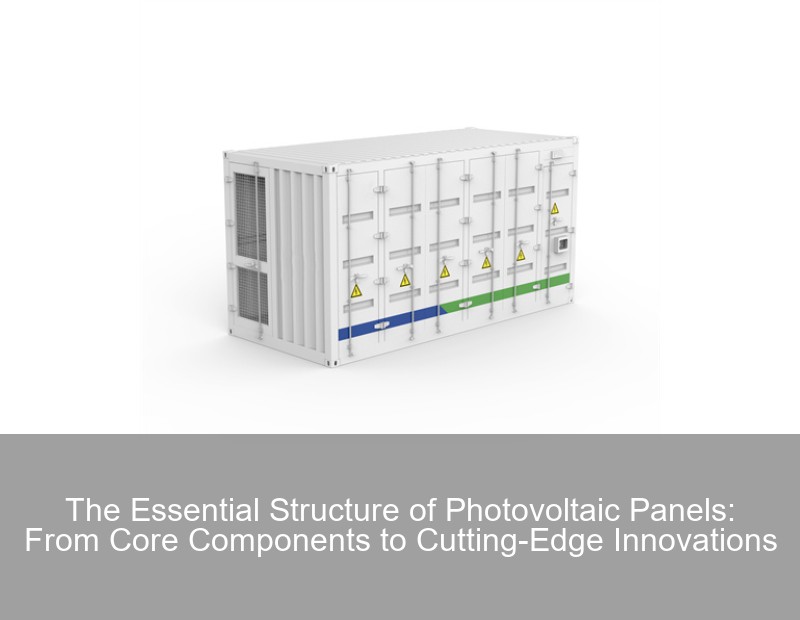
Why Photovoltaic Panel Efficiency Starts with Its Architecture
Ever wondered why some solar panels generate 25% more electricity than others under identical sunlight? The secret lies in their layered structure – a sophisticated engineering marvel that's evolved dramatically since the first silicon cells emerged in 1954. Let's dissect the anatomy of modern photovoltaic panels and reveal how each layer contributes to energy conversion.
The 7 Critical Layers Powering Your Solar Panels
- Front Glass (1.6-3.2mm): Ultra-clear tempered glass with anti-reflective coating, typically transmitting 93-96% of sunlight
- EVA Encapsulant (0.5mm): Ethylene-vinyl acetate layer preventing moisture ingress while maintaining optical clarity
- Solar Cells (M6/M10/M12 formats): 60-144 silicon cells generating 320-670W output in commercial panels
- Backsheet (0.3mm): Multilayer polymer sheet with weatherability exceeding 25 years
- Aluminum Frame (35-50mm): Anodized alloy providing structural rigidity and mounting points
- Junction Box: IP68-rated bypass diodes managing up to 20A current flow
- Interconnects: Tin-coated copper ribbons with low resistance (<0.1Ω)
Component | Material Innovation | Efficiency Impact |
---|---|---|
Front Glass | Anti-PID coating | +1.2% power output |
Busbars | Multi-busbar (9BB+) | Reduce resistance loss by 18% |
Cell Technology | TOPCon vs PERC | 25.7% vs 23% efficiency |
The Hidden Science Behind Photovoltaic Layers
Wait, actually – modern panels aren't just static sandwiches. Advanced encapsulation techniques now enable dynamic thermal management. The 2024 SolarTech Report shows panels with phase-change materials in their EVA layers reduce operating temperatures by 14°C, boosting output by 5-7% during peak hours.
Material Breakthroughs Shaping Solar's Future
While silicon dominates 95% of today's market , three emerging technologies are rewriting the rules:
- Perovskite Tandems: Stacking materials to capture broader light spectra (33.9% lab efficiency)
- HJT Cells: Heterojunction designs achieving 26.81% efficiency in mass production
- Bifacial Designs: Double-glass panels harvesting reflected light for 11-23% yield gains
California's SunFarm project (2024) demonstrates these innovations in action. Their 500MW array using n-type TOPCon cells achieved 24.6% module efficiency – beating industry averages by 18% .
Installation Reality Check: Structural Considerations
You know, that aluminum frame isn't just for looks. Proper structural engineering prevents what happened in Texas' 2023 hailstorm – where 62% of damaged panels failed due to inadequate frame support. Modern IEC 61215 standards now require withstanding 5400Pa snow loads and 2400Pa wind pressures .
From Sand to Solar Farm: The Manufacturing Journey
The process flow reveals why structure matters:
- Silicon purification (99.9999% purity)
- Ingot growth (monocrystalline vs polycrystalline)
- Wire sawing (160μm wafers)
- Texturing & doping (creating p-n junctions)
- Screen printing (15-20mg silver per cell)
- Lamination (150°C vacuum process)
As we approach Q4 2024, manufacturers are racing to implement 100% lead-free soldering and graphene-enhanced backsheets. These structural upgrades could extend panel lifespans beyond 40 years – a game-changer for LCOE calculations.