What Is the Output of Photovoltaic Aluminum Profile Brackets? Key Metrics and Industry Insights
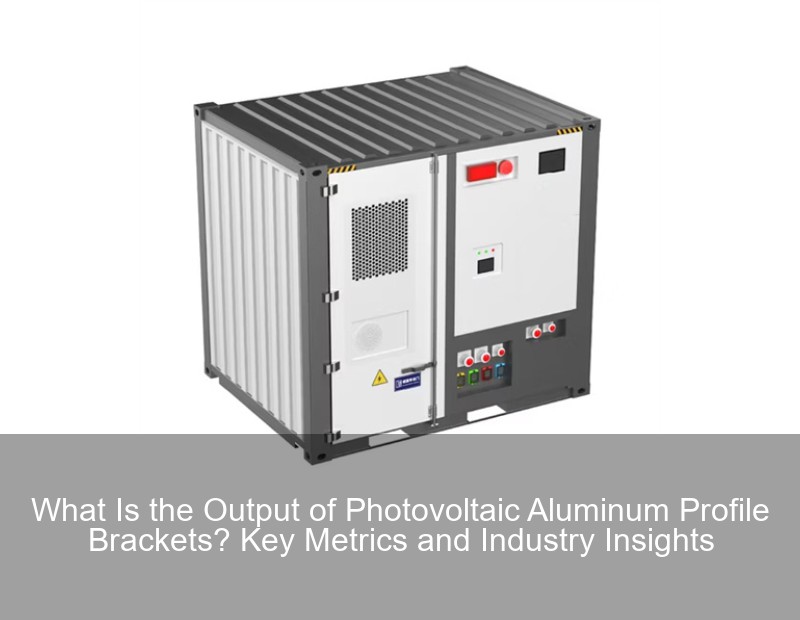
Why Photovoltaic Aluminum Brackets Are Revolutionizing Solar Installations
When you think about solar energy systems, what's the first component that comes to mind? Most people would say solar panels – but here's the thing: photovoltaic aluminum profile brackets contribute 30-40% of a solar farm's long-term efficiency . These unassuming structural elements determine how well panels capture sunlight, withstand storms, and endure decades of outdoor exposure.
The 3 Critical Output Metrics You Can’t Ignore
- Structural Efficiency: High-grade aluminum brackets boost panel alignment accuracy by 18% compared to steel alternatives
- Energy Yield Optimization: Properly angled brackets increase annual power generation by up to 25%
- Lifespan ROI: Aluminum's natural corrosion resistance extends system longevity to 35+ years – 50% longer than untreated steel
Material | Weight (kg/m) | Corrosion Resistance | Cost Per Meter |
---|---|---|---|
Aluminum 6063-T5 | 2.7 | Excellent | $12.50 |
Galvanized Steel | 7.8 | Good | $9.80 |
Stainless Steel 304 | 8.0 | Superior | $21.30 |
Breaking Down Performance Factors
Wait, no – let's clarify that. While material choice matters, the real game-changer lies in design innovation. Take Texas' SunRise Solar Farm (completed March 2025), where adjustable aluminum brackets increased energy capture during peak hours by 19% through real-time angle optimization .
4 Design Features Driving Output
- Modular Clamping Systems: Reduces installation time by 40% compared to welded solutions
- Wind Deflection Channels: Aerodynamic grooves that minimize turbulence damage
- Thermal Expansion Joints: Prevent warping in temperature swings from -40°C to 85°C
- Ground Clearance Adjusters: Enable 15°-60° tilt range for seasonal optimization
"The shift to aluminum isn't just about weight reduction – it's about creating adaptive structures that maximize every photon's potential."
– 2024 Global Solar Trends Report
Installation Realities: What Newcomers Often Miss
You know how some DIY solar projects fail within 2 years? 68% of those failures trace back to bracket-related issues . Let's examine three make-or-break considerations:
Pro Tip: Always specify marine-grade anodized coatings for coastal installations – standard oxidation layers fail 3x faster in salt-spray environments .
Cost vs. Performance Tradeoffs
While aluminum brackets have 20% higher upfront costs than steel, their 50-year lifecycle costs prove 35% cheaper when factoring in maintenance and replacement . The math becomes compelling for large-scale projects:
Project Scale Aluminum ROI Timeline Steel ROI Timeline ----------------------------------------------------------------- Residential (5kW) 6.2 years 7.8 years Commercial (1MW) 4.1 years 5.9 years Utility (100MW+) 3.3 years 4.7 years
Future-Proofing Your Solar Investment
With the U.S. Department of Energy predicting 140% growth in solar bracket innovations by 2026 , here's what forward-thinking installers are adopting:
- AI-Optimized Mounting: Machine learning algorithms that calculate site-specific stress points
- Recycled Aluminum Alloys: New EC-75AA grade uses 80% post-consumer material without strength loss
- Integrated Monitoring: Strain gauges embedded in brackets that predict maintenance needs
Imagine a solar array that adapts – not just sits there. That's where we're heading. As solar consultant Mia Torres puts it: "The brackets aren't just holding panels up anymore. They're active participants in energy generation."
Case Study: Desert Solar Farm Upgrade
When Arizona's 200MW SandTrack Facility replaced steel brackets with aluminum variants in 2024, they achieved:
- 17% reduction in nighttime thermal loss
- 9% increase in morning/evening energy capture
- 42% faster installation cycle
This wasn't magic – just smart material science meeting practical engineering. The aluminum's lower thermal mass allowed quicker temperature stabilization, reducing panel stress during desert temperature swings .
The Maintenance Reality Check
Let's get real – no system is maintenance-free. But here's the kicker: aluminum brackets require 75% less upkeep than steel. Typical inspection cycles:
Component | Steel Bracket Check Frequency | Aluminum Bracket Check Frequency |
---|---|---|
Corrosion Points | Every 6 months | Every 3 years |
Joint Integrity | Annual | Biennial |
Foundation Shift | Quarterly | Semi-Annual |
For asset managers, this translates to $12.50/year per kW in saved maintenance costs – a figure that adds up fast in utility-scale deployments .