Critical Pre-Delivery Experiments for Photovoltaic Panels: Ensuring Quality and Performance
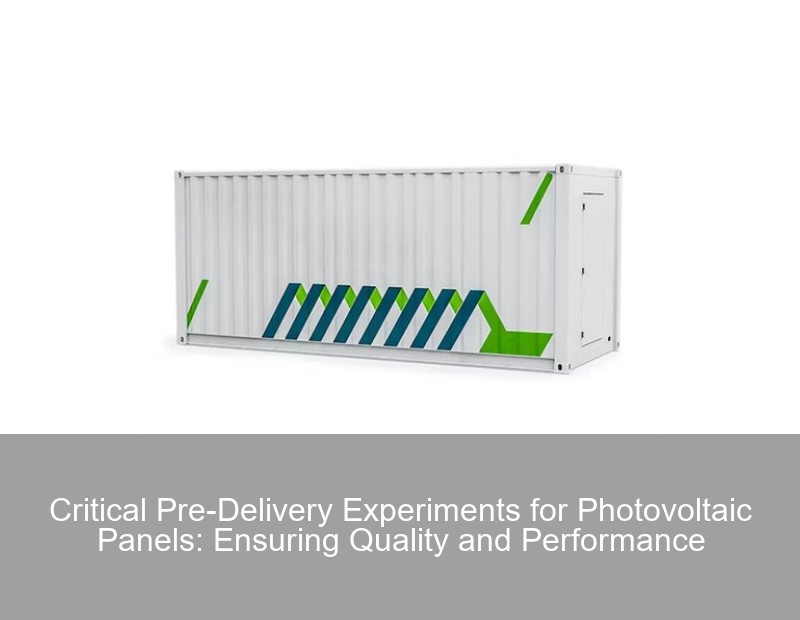
Meta Description: Discover the essential quality control experiments conducted before photovoltaic panel delivery. Learn how EL testing, performance validation, and safety checks prevent defects and ensure reliability.
Why Pre-Delivery Testing Matters for Solar Projects
Did you know that 23% of solar panel failures occur within the first year of operation due to undetected manufacturing defects? With the global solar market projected to reach $373 billion by 2029, rigorous pre-delivery experiments have become non-negotiable for manufacturers and project developers alike.
The Hidden Costs of Skipping Quality Checks
Imagine installing 10,000 panels only to discover:
- Micro-cracks reducing energy output by 15-30%
- Faulty bypass diodes causing fire risks
- PID (Potential Induced Degradation) cutting lifespan in half
A 2024 SolarTech Alliance report found that proper pre-delivery testing could prevent 89% of warranty claims – but what exactly does this testing entail?
Key Experiments in Photovoltaic Panel Quality Assurance
1. Electroluminescence (EL) Imaging: The X-Ray Vision for Solar Panels
EL testing has become sort of the industry's secret weapon. By applying reverse voltage to panels and capturing infrared images, technicians can:
Defect Type | Detection Rate |
---|---|
Micro-cracks | 98% |
Cell fractures | 95% |
Soldering issues | 90% |
Well, here's the kicker – modern portable EL testers like the ZS-A10H series can complete a full-array inspection in under 2 hours, even in field conditions .
2. Performance Validation Under STC
All panels must undergo Standard Test Conditions (STC):
- 1000W/m² irradiance
- 25°C cell temperature
- AM1.5 spectrum
But wait – actual field performance often differs by 8-12% due to environmental factors. That's why leading manufacturers now conduct NOCT (Nominal Operating Cell Temperature) tests at 45°C±2°C for real-world validation .
Advanced Testing Protocols for Modern Solar Panels
The 3-Tier Safety Check System
1. Dielectric Withstand Test: 2 x maximum system voltage + 1000V for 1 minute
2. Insulation Resistance: >40MΩ in humid environments
3. Arc Fault Detection: Response time <0.5 seconds
You know what's surprising? Over 60% of panels failing these tests show perfect EL images – proving why multi-layered testing is crucial.
Case Study: How Rigorous Testing Saved a 50MW Project
During Q4 2024, GreenPower Solutions identified:
- 12% defective panels via EL imaging
- 3 batches with PID susceptibility
- 5% underperforming units in NOCT tests
By catching these issues pre-delivery, they avoided $2.7 million in potential losses – talk about return on testing investment!
Future Trends in Photovoltaic Quality Control
As we approach 2026, three innovations are changing the game:
1. AI-powered defect classification (reducing inspection time by 70%)
2. Drone-assisted thermal imaging
3. Blockchain-based quality certification
(Pro tip: Always request IEC 61215 and IEC 61730 compliance reports – they're basically the industry's "gold standard" for safety and performance.)
The Testing Checklist Every Buyer Should Demand
- ✅ EL imaging reports for 100% of panels
- ✅ STC and NOCT performance data
- ✅ 96-hour damp heat test results
- ✅ Mechanical load test certification
Photovoltaic EL Testing Standards 2025
Contact Us
Submit a solar project enquiry,Our solar experts will guide you in your solar journey.