Wind Turbine Blade Materials: The Engine Behind Renewable Energy Efficiency
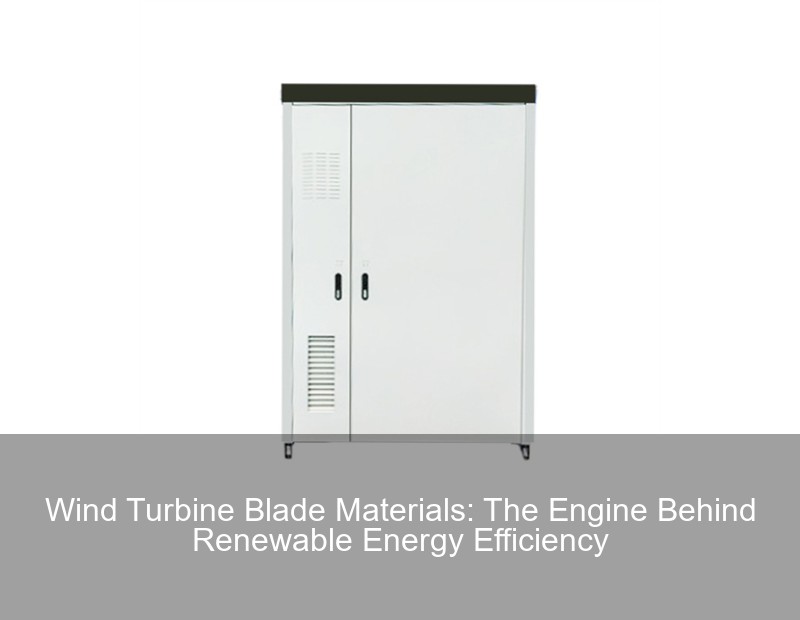
Why Do Wind Turbine Blade Materials Matter More Than Ever?
As global wind capacity surges toward 1,400 GW by 2025 (per the 2024 Global Wind Energy Council Report), the materials behind turbine blades have become a make-or-break factor. But what exactly makes these 80-meter-long giants withstand hurricanes, ice storms, and 20+ years of constant rotation?
The Core Materials Driving Today's Wind Revolution
Modern blades rely on three heavyweight contenders:
- Glass Fiber-Reinforced Plastic (GFRP): The industry workhorse, used in 68% of operational blades globally . Offers solid strength at $8-$12/kg.
- Carbon Fiber Composites (CFRP): The premium choice for blades over 90 meters. Despite costing $25-$40/kg, they reduce blade weight by 30% compared to GFRP .
- Sandwich Composites: Hybrid systems combining balsa wood cores with epoxy resins - a cost-effective solution for mid-sized turbines .
Material Showdown: Performance vs. Practicality
Material | Tensile Strength (MPa) | Cost per kg | Best For |
---|---|---|---|
GFRP | 1,200-1,600 | $8-12 | Blades under 80m |
CFRP | 2,500-3,500 | $25-40 | Offshore/ultra-long blades |
Epoxy-SMC | 800-1,100 | $6-9 | Mass-produced blades |
Wait, no—those epoxy-SMC numbers might surprise you. Actually, newer formulations now reach 1,400 MPa at $11/kg , making them serious competitors.
The Hidden Challenges in Blade Material Selection
Manufacturers face a brutal optimization puzzle:
- ▸ Lightning strikes: Carbon fiber's conductivity prevents $200k+ blade replacements
- ▸ UV resistance: Texas blade failures increased 12% after extreme UV exposure in 2023
- ▸ Recyclability: Only 15% of retired GFRP blades get recycled—a PR nightmare
"Choosing blade materials is like engineering a Formula 1 car that must last 20 years in a demolition derby." — Dr. Elena Marquez, 2024 WindTech Symposium
Emerging Innovations Changing the Game
Three cutting-edge developments demand attention:
- Bio-based Epoxies: Dow Chemical's 2024 SoyTurbo resin reduces curing time by 40% while using 30% renewable content
- Self-Healing Polymers: Microcapsule technology that automatically repairs microcracks (patent pending, GE Renewables)
- 3D-Printed Cores: Siemens Gamesa's new lattice structures increase stiffness-to-weight ratios by 18%
Future-Proofing Wind Energy: What's Next?
As turbine sizes balloon beyond 110 meters, material scientists are exploring radical solutions:
- ▸ Graphene-enhanced coatings improving erosion resistance
- ▸ Phase-change materials regulating blade surface temperatures
- ▸ AI-driven material combinations optimizing regional performance
The race is on—will next-gen materials finally crack the 20¢/watt barrier for onshore wind? With new thermoplastic resins entering trials this quarter, the answer might surprise us all.
Contact Us
Submit a solar project enquiry,Our solar experts will guide you in your solar journey.