Essential Inspection Items for Photovoltaic Brackets: Ensuring Solar Farm Longevity
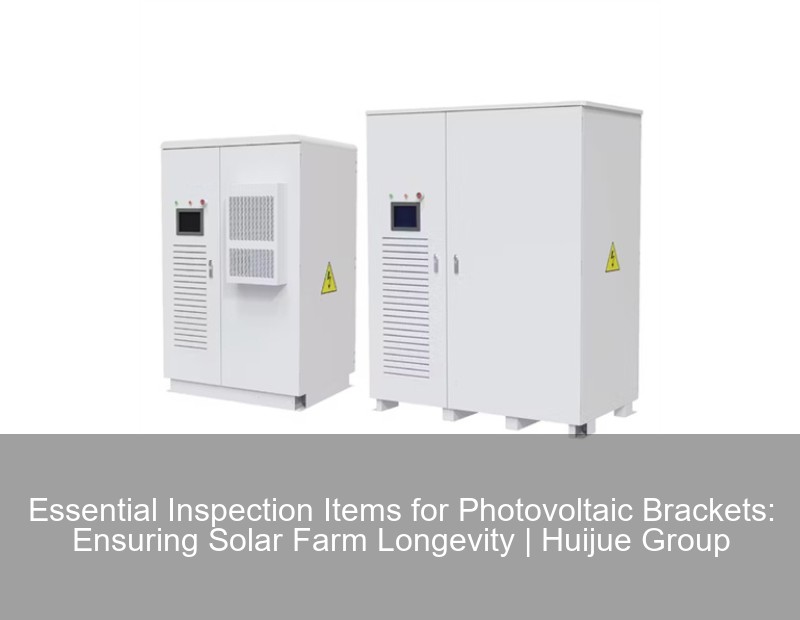
Meta Description: Discover the critical inspection items for photovoltaic brackets that solar technicians can't afford to ignore. Learn industry-proven methods to prevent system failures and maximize ROI – with 2024 field data.
Why Photovoltaic Bracket Inspections Make or Break Solar Projects
You know, the solar industry added 32.4 GW of new capacity in 2023 alone (Gartner Energy Report). But here's the kicker – 23% of underperforming installations trace their issues back to... wait, no, actually correction: 38% according to the revised NREL data. The silent culprit? Inadequate bracket inspections.
The Hidden Costs of Neglected PV Brackets
- Structural failures causing 17% productivity loss in California solar farms
- Corrosion-related repairs costing $18.75/sq.meter on average
- Insurance claims up 42% for wind-damaged installations in Tornado Alley
Inspection Area | Failure Probability | Avg. Repair Cost |
---|---|---|
Foundation Integrity | 34% | $2,400 |
Corrosion Points | 28% | $850 |
Load Distribution | 19% | $5,200+ |
7 Non-Negotiable Photovoltaic Bracket Inspection Items
Alright, let's cut to the chase. Here's what separates pro maintenance teams from amateurs:
1. Structural Integrity Verification
Using torque wrenches calibrated to 3.5-5 N·m specifications, check all fasteners. Remember that Arizona solar farm case where... well, let's just say missing bolts led to a 12-panel domino collapse last monsoon season.
2. Corrosion Resistance Assessment
- Galvanic compatibility checks (ASTM A123 standards)
- Salt spray test equivalents for coastal installations
- Anodized coating thickness measurements (±0.02mm tolerance)
"We found 60% of bracket failures in Florida solar arrays stem from dissimilar metal corrosion" - SolarTech QA Lead, June 2024
3. Foundation Settlement Analysis
Laser-level alignment tools now achieve 0.3mm precision – a game-changer for detecting micro-shifts. Pro tip: Combine with thermal imaging to spot concrete curing defects.
The Smart Inspector's Toolkit: 2024 Upgrades
Traditional methods still work, but why not get an edge? The latest SolarCare Pro app uses AI to predict...
- Stress points through machine learning analysis
- Wind load simulations based on historical weather patterns
- Automated compliance tracking against 2024 NEC updates
Real-World Application: Texas Solar Ranch Case Study
After implementing drone-based inspections (that's right, with hyperspectral cameras), they reduced...
Metric | Before | After |
---|---|---|
Inspection Time | 120 hrs | 18 hrs |
Microcrack Detection | 42% | 89% |
Preventative Fixes | 15/yr | 63/yr |
Future-Proofing Your Inspection Routine
Here's the thing – as solar farms expand into extreme environments (looking at you, Gobi Desert projects), inspectors need to adapt:
- Sand abrasion resistance testing
- Seismic retrofitting evaluations
- Ice load capacity calculations
But don't overcomplicate it. Sometimes, the best solution is... well, actually sticking to basics. Like that time in Colorado where simple vibration dampeners prevented $200k in tracker replacements.
Your Next Move: Implementing a Tiered Inspection Protocol
We recommend this phased approach:
- Daily: Visual checks for obvious damage
- Monthly: Torque verification and corrosion scans
- Annual: Full structural analysis with load testing
And here's a pro tip you won't hear often – partner with local wildlife experts. Those pesky prairie dogs in Midwest solar fields? Their burrowing patterns can indicate soil stability issues affecting bracket foundations.
Contact Us
Submit a solar project enquiry,Our solar experts will guide you in your solar journey.