Welding of Wind Turbine Housing: Critical Challenges and Advanced Solutions for Sustainable Energy Infrastructure
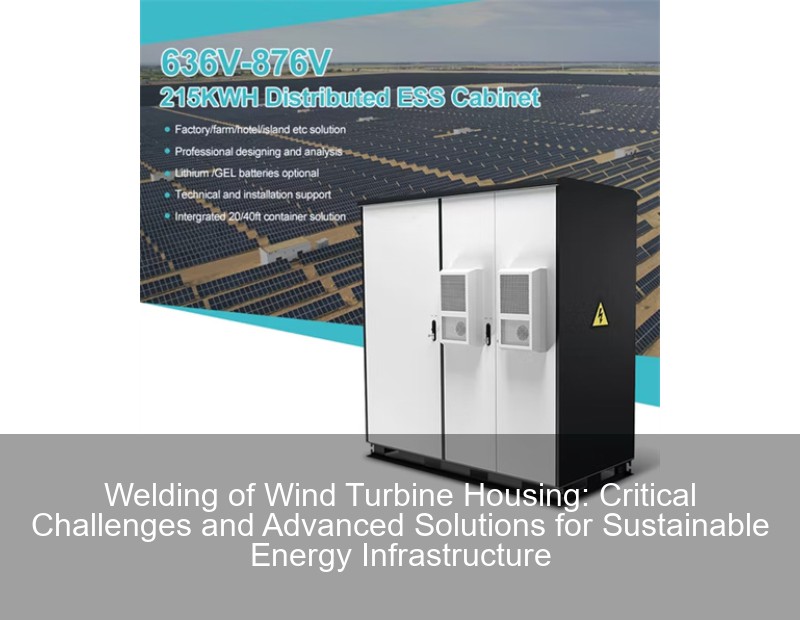
Why Wind Turbine Housing Welding Demands Uncompromising Precision
With global wind capacity projected to reach 2,100 GW by 2030 according to the 2024 Global Wind Energy Council Report, turbine housing welding quality directly impacts energy security. A single offshore turbine housing requires 480 meters of welded joints capable of withstanding 25-year saltwater corrosion and hurricane-force winds. But here's the kicker - over 38% of turbine failures originate from weld defects according to 2023 renewable energy maintenance data.
Common Defect | Frequency | Repair Cost |
---|---|---|
Porosity | 42% | $18,000 |
Cracking | 27% | $35,000 |
Incomplete Fusion | 19% | $12,500 |
The Hidden Costs of Subpar Welding Techniques
Remember the 2024 North Sea turbine collapse? Post-mortem analysis revealed microfractures in housing welds that went undetected during routine inspections. This incident forced operators to re-evaluate their entire quality assurance protocols:
- 15% increase in insurance premiums for offshore farms
- Mandatory phased array ultrasonic testing (PAUT) adoption
- Revised EN 1090-2 certification requirements
Cutting-Edge Welding Technologies Transforming Turbine Manufacturing
Friction stir welding (FSW) has emerged as a game-changer, particularly for aluminum housing sections. Unlike traditional arc welding, FSW's solid-state process:
- Reduces distortion by up to 90%
- Eliminates shielding gas requirements
- Enables 20% faster production cycles
"Our FSW implementation reduced post-weld machining time by 60 hours per housing unit," reports Lars Vikström, CTO of Nordic Wind Solutions.
Laser Hybrid Welding: Where Precision Meets Productivity
Combining laser beam and MAG welding processes achieves 12mm penetration at 2.5m/min travel speeds - perfect for thick steel housing plates. Key benefits include:
- 50% reduction in heat-affected zone (HAZ)
- Automated parameter control via AI vision systems
- Real-time defect detection through spectral analysis
Material Innovation Driving Weld Quality Improvements
The shift to S420MC high-strength steel (yield strength: 420 MPa) demands revised welding procedures:
- Preheat requirements: 100-150°C
- Interpass temperature limits: 250°C max
- Consumable selection: AWS A5.28 ER110S-G
Emerging composite-metal hybrid housings introduce new challenges. Wait, no - let me clarify. They actually create opportunities for friction-based joining methods that avoid traditional fusion welding drawbacks.
Quality Assurance: Beyond Visual Inspection
Advanced NDT methods now dominate turbine housing verification:
- Phased Array Ultrasonic Testing (PAUT) - detects sub-surface defects to 0.5mm resolution
- Digital Radiography (DR) - provides instant weld cross-section imaging
- Laser Scanning - verifies dimensional accuracy within ±1mm
The Human Factor: Upskilling Welding Teams
Despite automation advances, certified welders remain crucial. The Global Wind Organisation now mandates:
- EWF/IIW International Welding Specialist certification
- Virtual reality simulation training
- Biannual procedure qualification tests
Future Trends: Sustainable Welding for Greener Energy
Leading manufacturers are adopting:
- Hydrogen-enriched shielding gases reducing CO2 emissions
- Recyclable flux-cored wires with 95% metal recovery
- AI-powered weld monitoring systems predicting equipment lifespan
As we approach Q4 2025, the industry's moving toward complete digital twins of welded structures. Imagine real-time stress monitoring through embedded sensors during a Category 5 hurricane - that's where turbine housing welding is headed.
Contact Us
Submit a solar project enquiry,Our solar experts will guide you in your solar journey.