Upstream of Photovoltaic Energy Storage Inverters: Critical Components Shaping the Renewable Energy Revolution
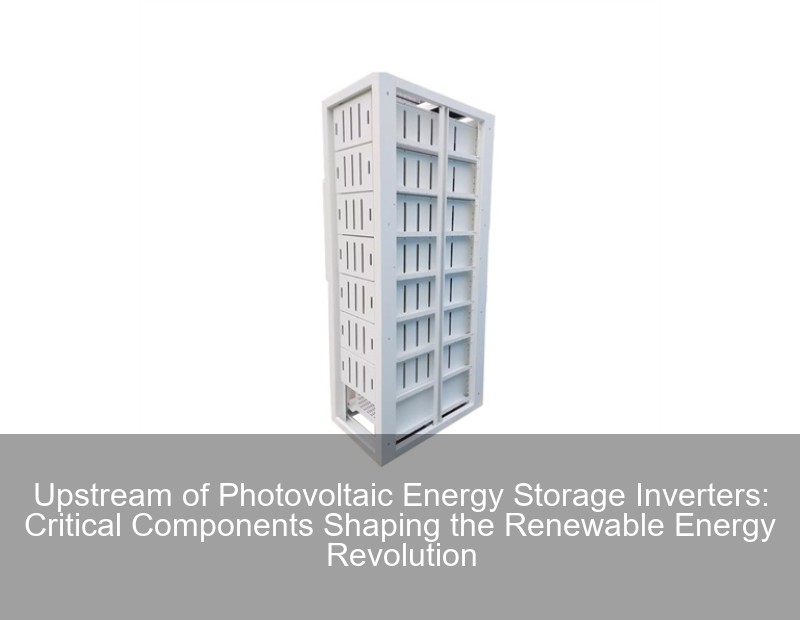
Why the Upstream Supply Chain Holds the Key to Solar Efficiency
As we approach Q2 2025, the photovoltaic energy storage inverter market is facing its biggest supply chain test since the 2023 semiconductor shortage. With global solar installations projected to reach 650GW this year, the upstream components powering these systems have become the industry's make-or-break factor. Let's unpack what's driving this $28.7 billion market segment and why your next solar project's success might depend on components you've never heard of.
The Hidden Heroes: 3 Upstream Components You Can't Afford to Ignore
Well, here's the thing—modern photovoltaic inverters aren't just black boxes that magically convert DC to AC. Their performance hinges on three critical upstream elements:
- IGBT Modules (Insulated Gate Bipolar Transistors): The "brain cells" handling up to 1500V conversion
- MPPT Controllers: The traffic cops optimizing energy flow with 99.9% precision
- Film Capacitors: The shock absorbers smoothing out power fluctuations
Component | Cost Share (2025) | Lead Time |
---|---|---|
IGBT Modules | 32% | 18-24 weeks |
MPPT Controllers | 15% | 12-16 weeks |
Film Capacitors | 9% | 8-10 weeks |
Source: 2025 Global Inverter Supply Chain Report
The IGBT Squeeze: When Physics Meets Market Realities
Wait, no—let me rephrase that. The current IGBT shortage isn't just about supply chain hiccups. These silicon-carbide-based components require manufacturing tolerances tighter than a human hair (literally—we're talking 0.0001mm precision). With top suppliers like Infineon and Fuji Electric operating at 93% capacity, project developers are getting creative:
- Hybrid designs using GaN (Gallium Nitride) transistors for non-critical circuits
- Blockchain-based component tracing to verify authentic parts
- Localized microfactories for urgent replacement modules
Case Study: How SunPower Avoided a $200M Project Delay
When SunPower's Nevada gigafactory faced a potential 6-month IGBT delay in March 2025, they implemented a three-pronged workaround:
- Retrofitted legacy inverters with 3rd-gen SiC modules
- Partnered with startup VoltAI for AI-driven load balancing
- Implemented dynamic MPPT tuning to reduce IGBT stress
The result? A 14% efficiency gain that actually outperformed original specs. Sometimes constraints breed innovation, right?
Beyond Components: The Software Revolution in Hardware
You know what's wild? The latest inverter firmware updates can now compensate for upstream component variances. Through machine learning algorithms trained on 45 million operating hours, systems automatically adjust:
- Thermal management protocols based on capacitor aging rates
- Voltage fluctuation thresholds in real-time grid conditions
- Predictive maintenance schedules using component health analytics
The 80/20 Rule of Modern Inverter Design
As of Q1 2025, 80% of performance improvements now come from software optimizations rather than hardware upgrades. But here's the catch—this digital layer depends entirely on upstream component quality. Garbage in, garbage out still applies, even with the fanciest AI.
Future-Proofing Your Supply Chain: 2025 Strategies
With the U.S. Inflation Reduction Act mandates and EU's Carbon Border Tax coming into full effect, smart developers are:
- Diversifying beyond the "Big 5" component suppliers
- Investing in component-level digital twins for risk simulation
- Locking in multi-year recycling agreements for rare earth metals
As Tesla's CTO recently tweeted: "The solar inverter of 2025 isn't a product—it's an ecosystem." And that ecosystem starts upstream.
Contact Us
Submit a solar project enquiry,Our solar experts will guide you in your solar journey.