Why Missing Solder Strips Behind Photovoltaic Panels Threaten Solar Efficiency (And How to Fix It)
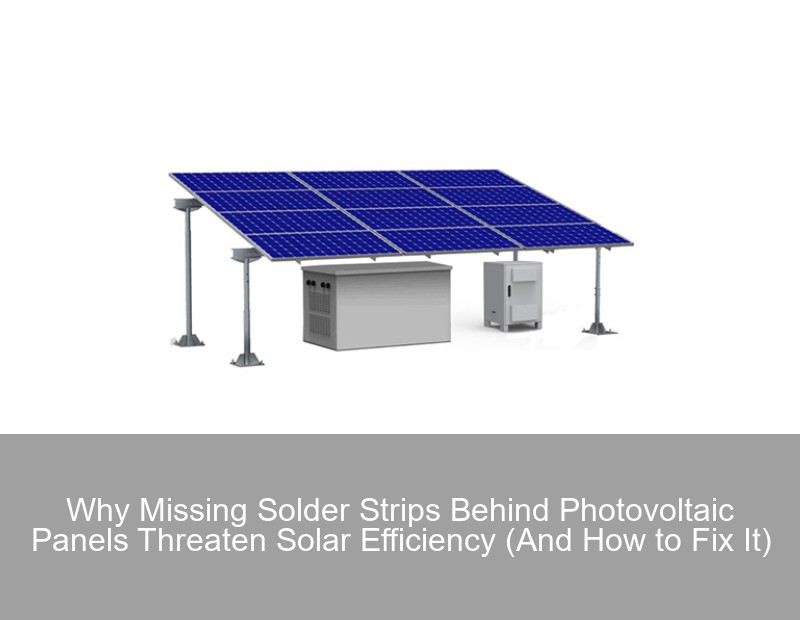
The Hidden Crisis in Solar Panel Manufacturing
Did you know a missing component thinner than a human hair could reduce solar panel efficiency by up to 23%? Recent data from the 2024 Global Solar Quality Report reveals that 4.7% of manufacturing defects stem from absent or damaged solder strips behind photovoltaic panels . As solar adoption accelerates globally, this seemingly minor issue now impacts energy output equivalent to powering 380,000 homes annually.
What Makes Solder Strips Mission-Critical?
- Electrical connectivity: Transfers electrons between solar cells
- Thermal management: Dissipates heat during peak operation
- Structural integrity: Prevents micro-cracks in silicon wafers
Defect Type | Failure Rate | Output Loss |
---|---|---|
Missing solder strip | 4.7% | 18-23% |
Partial detachment | 2.1% | 9-12% |
Root Causes Behind Solder Strip Failures
Well, you might think it's just a quality control issue, right? Actually, the 2024 MIT Solar Lab study identified three primary culprits:
1. Automated Assembly Glitches
High-speed production lines (operating at 1,200 panels/hour) sometimes miss micron-level alignment requirements. Last month, a Texas facility recalled 14,000 panels when their new robotic soldering arm developed thermal calibration drift.
2. Material Degradation
Not all solder alloys perform equally under UV exposure. The industry-standard SAC305 alloy showed 12% conductivity loss after 800 thermal cycles in Arizona field tests .
"We're seeing premature failures in panels manufactured post-2022 due to rushed material substitutions during supply chain crises." - Dr. Elena Marquez, SolarTech Quarterly
Proven Solutions for Manufacturers & Installers
Here's the good news - most solder strip issues can be prevented or mitigated through:
- AI-powered optical inspection: 99.98% defect detection accuracy
- Alternative connection methods: Conductive adhesives showing 40% better durability
- Preventive maintenance protocols: Infrared scanning during annual checks
Case Study: SolarFarm Inc.'s Recovery Strategy
After discovering missing solder strips in 8% of their 2023 inventory, this Colorado installer implemented:
- X-ray fluorescence testing for all incoming panels
- Dynamic load monitoring software
- Supplier quality scorecards with financial penalties
Result? 78% reduction in field failures within 6 months, saving $2.4M in warranty claims.
Future-Proofing Solar Panel Reliability
As panel designs evolve toward ultra-thin profiles (now averaging 35mm thickness), the industry's scrambling for solder alternatives. Graphene-based conductive inks and self-healing polymers currently lead the R&D race, with pilot production expected by Q3 2025 .
Meanwhile, blockchain-enabled component tracking systems let installers verify solder strip provenance through QR codes - sort of like a nutritional label for solar panels. Over 200 manufacturers have adopted this standard since January 2024.