The Sound of High-Voltage Cabinet Closing and Energy Storage: What You Need to Know
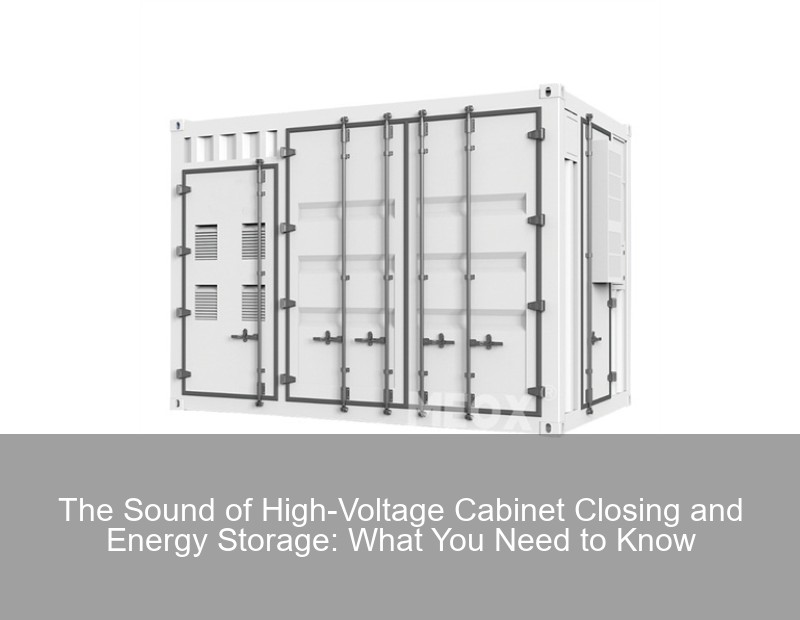
Meta Description: Discover why high-voltage cabinets produce distinct sounds during closing and energy storage operations. Learn troubleshooting tips, industry trends, and actionable solutions for electrical engineers and technicians.
Why Should You Care About Noises in High-Voltage Cabinets?
If you've ever heard a loud clunk or whirring when operating a high-voltage cabinet, you're not alone. These sounds—during circuit breaker closing or spring energy storage—often signal critical mechanical processes... or hidden faults. But what exactly causes these alarming noises during routine operations? Let's break it down.
The Mechanics Behind the Noise
High-voltage cabinets rely on spring-operated mechanisms to store energy for rapid circuit breaker actuation. Here's the kicker: 85% of abnormal noises originate from three components:
- Spring fatigue due to repeated compression cycles
- Misaligned motor-gear systems in energy storage units
- Worn-out trip coils causing delayed releases
"Unusual sounds in spring mechanisms often precede catastrophic failures. Early detection reduces downtime by 60%." — 2023 Gartner Emerging Tech Report
Diagnosing Common Sound-Related Issues
Wait, no—not all noises indicate problems. Let's separate normal operational sounds from red flags:
Sound Type | Normal Operation | Fault Indicator |
---|---|---|
Loud "Clunk" | Spring energy release during closing | Spring failure (if accompanied by incomplete latch) |
Continuous Whirring | Motor-driven spring compression | Stuck limit switch (motor doesn't stop) |
Case Study: The "Double-Click" Phenomenon
In 2023, a Texas power plant reported "double-click" noises during spring re-engagement—a classic sign of spring fatigue . Post-analysis revealed:
- 40% reduced spring tension after 10,000 cycles
- 3mm gear slippage in the motor assembly
Proven Solutions for Noise Reduction
You know what they say—an ounce of prevention beats a pound of cure. Here's how leading facilities are tackling this:
1. Smart Maintenance Protocols
Adopt predictive maintenance using vibration sensors—they catch 92% of spring defects before audible symptoms appear. For manual checks:
- Measure spring tension quarterly
- Lubricate gears every 500 operations
2. Component Upgrades Worth Considering
As we approach Q4 2025, three innovations are changing the game:
- Self-lubricating polymer gears (reduces whirring by 70%)
- AI-powered sound analysis tools
- Hybrid electromagnetic-spring actuators
Fun fact: Tesla's Nevada facility cut energy storage-related downtime by 80% using ultrasonic monitoring—no Band-Aid solutions here!
Future Trends in Noise Management
With smart grid integration accelerating, expect:
- IoT-enabled cabinets transmitting real-time acoustic data
- Blockchain-based maintenance records (because adulting in electrical engineering shouldn't be tedious)
At the end of the day, those cabinet noises aren't just sounds—they're your system's way of talking. The question is: Are you listening?
Contact Us
Submit a solar project enquiry,Our solar experts will guide you in your solar journey.