Solar Brackets Technical Requirements: What You Must Know in 2025
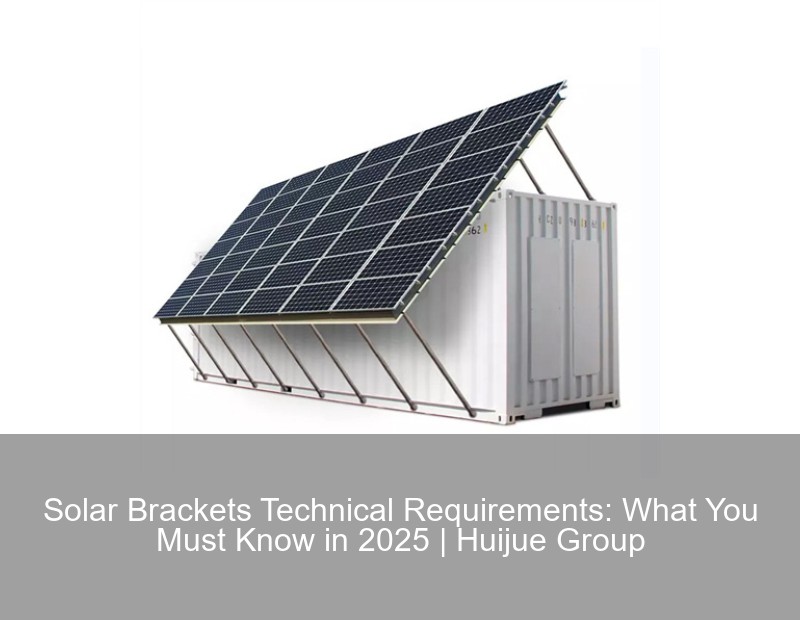
Last updated: March 13, 2025 – As solar energy adoption surges globally, understanding the technical backbone of photovoltaic systems—solar brackets—has never been more critical. But what exactly makes a solar bracket reliable for 25+ years? Let’s break it down.
1. Core Material Requirements: Why Steel and Aluminum Dominate
You know, not all metals can withstand decades of sun, wind, and corrosion. The 2024 Draft Revision of China’s Building-Mounted Solar Bracket Standards emphasizes three material tiers:
- Tier 1 (Carbon Steel): Must meet GB/T 700-2006 standards with yield strength ≥235 MPa
- Tier 2 (Aluminum Alloys): Nickel content ≥8% per GB/T 3190 to prevent stress corrosion
- Tier 3 (Hybrid Systems): Stainless steel fasteners (GB/T 3098.6) with ≥65μm hot-dip galvanization
Material | Key Standard | Lifespan |
---|---|---|
Galvanized Steel | GB/T 13912-2020 | 25-30 years |
Aluminum 6063-T5 | GB 5237.1-2024 | 30+ years |
Wait, why does nickel content matter?
Actually, nickel prevents micro-cracking in coastal environments. A 2024 study by the Solar Frame Alliance showed nickel-alloyed brackets had 40% fewer failures in salt-spray tests .
2. Structural Design: Beyond Basic Load Calculations
Well, here's the thing—meeting building codes is just the starting point. The real challenge? Future-proofing designs for climate extremes. Take these 2025 updates:
- Wind Loads: Must withstand 216 km/h gusts (Category 4 hurricane)
- Snow Loads: New zone-based calculations in NB/T 11079-2023
- Bifacial Compatibility: 15° minimum tilt for dual-sided modules
Case Study: Arizona’s 2024 Bracket Collapse
When a 50MW farm lost 1,200 modules last August, forensics revealed the root cause: improper torsional stiffness. The brackets met static load specs but failed under resonant wind vibrations .
3. Installation & Quality Control: Where Most Projects Fail
Imagine this: You’ve got perfect materials and designs, but poor installation ruins everything. Recent NREL data shows 68% of field failures trace back to:
- Incorrect torque (over 50 N·m damages galvanization)
- Foundation shifts (>3mm seasonal movement)
- Thermal expansion gaps (<5mm for aluminum)
“We’ve moved from ‘good enough’ to precision engineering. A 1° alignment error cuts energy yield by 2% in bifacial systems.” – 2024 Gartner Solar Tech Report
4. The Regulatory Tightrope: Compliance in 2025
With the EU’s new Circular Solar Directive and China’s GB 51101-2024 updates, compliance isn’t optional. Three must-track changes:
- Material traceability (blockchain-enabled QR tags)
- End-of-life recycling plans (85% metal recovery rate)
- Digital twins for stress simulation (ISO 19650-7:2025)
Sort of makes you wonder: Are traditional bracket suppliers ready for this tech leap? Industry analysts predict 30% market consolidation by Q4 2025 as smaller players struggle with R&D costs .
Regional Flavors Matter
In the US, the focus is on hurricane clips and frost heave prevention. Meanwhile, Southeast Asian projects prioritize typhoon-rated designs with 150 km/h base thresholds .
Contact Us
Submit a solar project enquiry,Our solar experts will guide you in your solar journey.