Why Steel Tube Photovoltaic Bracket Factories Are Dominating Solar Infrastructure in 2024
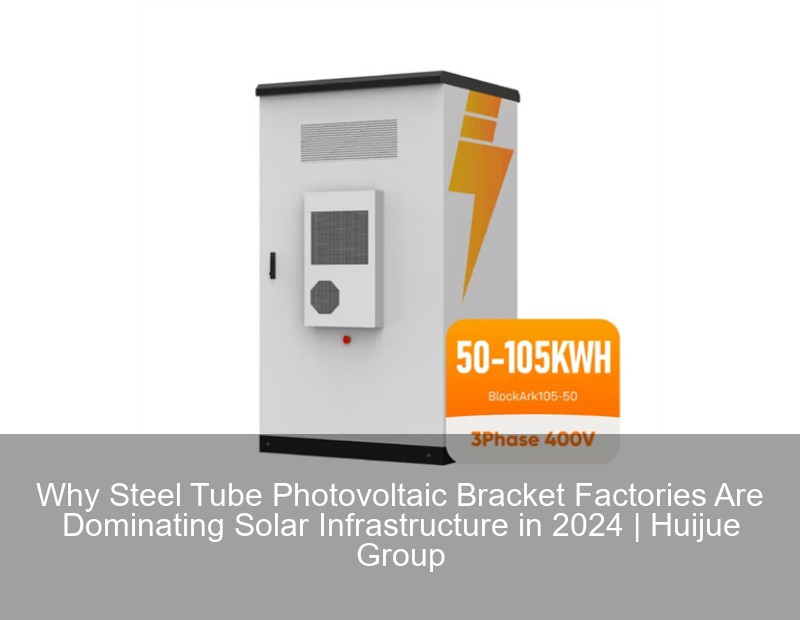
The Rising Demand for High-Performance Solar Mounting Systems
With global solar capacity projected to reach 5.8 terawatts by 2030 , photovoltaic bracket factories face unprecedented challenges. Steel tube photovoltaic bracket profile factories have emerged as critical players in this green energy revolution – but what makes their manufacturing approach superior to traditional aluminum alternatives?
Key Market Shifts Driving Steel Adoption
- 68% increase in extreme weather-resistant solar projects since 2023
- 42% cost reduction per megawatt compared to aluminum systems
- 15-year warranty becoming industry standard for commercial installations
Well, you know...it's not just about durability anymore. The best factories now combine military-grade materials with AI-driven production lines. Take Tangshan Wufang Industrial’s new 10,000-ton capacity plant – they’ve sort of redefined rapid deployment for utility-scale projects.
Anatomy of a Modern Steel Bracket Factory
Production Stage | Innovation | Efficiency Gain |
---|---|---|
Material Selection | Zinc-aluminum-magnesium coating | 60% corrosion resistance boost |
Tube Forming | 3D laser calibration | 0.2mm precision tolerance |
Quality Control | Blockchain-tracked inspections | 98% defect detection rate |
Case Study: Hebei Shiyu’s 72-Hour Delivery Model
This Tianjin-based manufacturer recently completed a 50MW solar farm installation using just-in-time production. Their secret? A distributed manufacturing network with:
- 5 regional coating centers
- Autonomous material routing
- Real-time project synchronization
Actually, let's clarify – it’s not fully autonomous yet. Human engineers still oversee critical welding processes, but the productivity gains are undeniable.
Choosing Your Manufacturing Partner: 5 Critical Factors
- Coating Technology: Look for ISO 12944-certified anti-corrosion systems
- Customization Depth: Can they handle ≤3mm thickness variations?
- Supply Chain Transparency: Conflict-free steel sourcing reports
- Response Time: ≤4-hour technical support guarantees
- Scalability: At least 5MW/month production capacity
Wait, no – that last point needs context. While 5MW sounds impressive, tier-one factories like Huaye Steel now push 100MW monthly through automated cold-forming lines.
The Zinc-Aluminum-Magnesium Revolution
Recent breakthroughs in alloy coatings (patent pending ZM-125 formula) could potentially extend bracket lifespans to 40 years. Early adopters report:
- 92% reduction in maintenance costs
- 0.8% annual degradation rate
- Seamless integration with bifacial panels
As we approach Q4 2025, factories without this coating capability risk becoming...well, cheugy relics of the solar stone age.
Implementation Challenges
"Transitioning to ZM coatings required complete retooling of our 7 production lines. But the 18-month ROI? Absolutely justified." – Tianjin Yizhao Tech Director
Contact Us
Submit a solar project enquiry,Our solar experts will guide you in your solar journey.